Farm Star XHB-1120 User Manual
Page 14
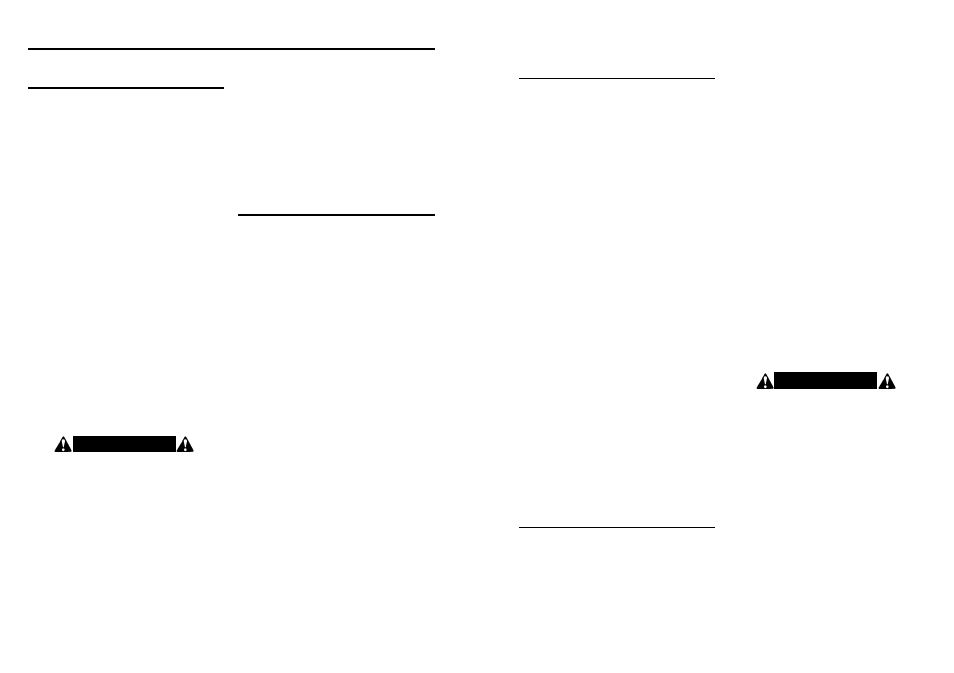
T R A C T O R R E Q U I R E M E N T S
A N D P R E PA R AT I O N
The XHB Series Rear Blades will fit Category II,
Category II Quick Hitches and some Category III N Quick
Hitches. These blades are designed for use on tractors
from 60 to 120 horsepower.
The model XHB-1096 (8ft.) blade is recommended for
tractors from 60 to 120 hp. The model XHB-1120 (10 ft.)
blade is recommended for tractors from 70 to 110 hp.
Check the tractor’s 3 point hydraulic lift system. It
should operate up and down smoothly and hold its posi-
tion when set. Refer to your tractor owner’s manual or
dealer for any adjustments necessary to put the 3 point
hydraulic lift system in good working order. (I&T shop
manuals will list most specifications and adjustment
instructions - available from most farm equipment
dealers.)
Check the hydraulic system. Be sure the tractor
hydraulic oil and filter have been serviced according to
the tractor manufacturer’s recommendations.
Tractor should be equipped with stabilizer bars,
adjustable sway chains, or sway blocks to keep the
implement from swinging side to side.
If blade is to be controlled hydraulically, then tractor
must be equipped with remote hydraulic outlets. If blade
offsets, angle, and tilt are to be operated hydraulically,
then tractor must have three (3) pair of remote connec-
tions. Adjustable mechanical links are available for all
three control locations if desired.
Smaller size tractors may need front counter weights to
counter-balance the weight of the implement.
It is recommended that the tractor be equipped with a
Rollover Protection System (ROPS) and a seat belt that
is used.
A S S E M B LY A N D M O U N T I N G
Assembly requirements will vary depending on how the
rear blade was shipped. Generally, most model XHB-
1096 (8 ft.) blades are shipped assembled while the
model XHB-1120 are shipped as two bundles on one pal-
let. The type of truck used and the amount of room on the
truck at the time of shipment determines how the blade
was shipped.
If your blade requires assembly, follow these steps:
1. Do not attempt to lift heavy parts or assemblies. Use
a hoist, crane, forklift, or similar safe mechanical
device.
2. Preview the assembly instructions and the exploded
views of the blade in your operator’s manual and
become familiar as to how the parts or assemblies go
together.
3. Have good blocking material available.
4. Select an area for assembly that is clean and free
from debris.
5. Assemble the 3 pt. hitch mount (Ref. #1) to the front of
the main swing arm (Ref. #2). The 1.75” diameter pin
(Ref. #9) has a
3
/
8
” x 3” roll pin installed at the top of
the pin with a 1.75” I.D. machinery bushing (Ref. #10)
between the roll pin and the top of the hitch mount.
It may be necessary to remove the paint from the
front pivot pin prior to installation. If so, it is recom-
mended that the pin be repainted after assembly.
A
3
/
8
” x 4” cotter pin (Ref. #12) is installed at the bot-
tom of the 1.75” front pivot pin to lock it in position.
6. Assemble the moldboard head (Ref. #3) to the mold-
board (Ref. #4). Grease the pivot pin (Ref. #5) before
assembly. Lock the pivot pin into position with the
5
/
8
”
x 2” bolt (Ref. #6).
H Y D R A U L I C S
If you are using one or more hydraulic cylinders to con-
trol the adjustment of the rear blade, refer to the
schematic drawing showing the proper cylinder, fittings,
hose, and relief valve arrangement.
All of the double-acting hydraulic cylinders require 90˚
hydraulic swivel type fittings. Use a good quality
hydraulic thread sealant. (DO NOT USE TEFLON TAPE
as small pieces of tape can cause hydraulic problems in
your tractor and hydraulic valves.)
NOTE: The use of the optional hydraulic cross-over relief
valve is highly recommended. This provides protection
for both the rear blade and the tractor. If the blade hits a
solid object and the pressure in the cylinders goes above
the relief valve setting, then the valve opens and allows
the blade to swing away from the solid object. This
reduces the impact shock on the blade and the tractor.
See separate schematic for cross-over relief valve
installation.
Route the hoses as shown on the drawing. Make sure
that the hoses are properly routed so they will not be
pinched or snagged as the blade is adjusted or raised
and lowered by the 3 pt. hitch. Loops are provided on the
blade frame to hold hoses away from the main pivot loca-
tions. Use nylon tie-straps to fasten hoses securely so
they will remain in their correct position and not drop
down where they could be pinched or sheared.
NOTE: Keep hydraulic connections tight. Repair leaky
hose or connections as soon as you discover them. Keep
cylinders and hoses free from internal contamination.
Never leave a disconnected hose end open. DO NOT
over tighten fittings as this could break the cylinder port
threads or the hydraulic fittings.
NOTE: The location of the remote hydraulic connections
on tractors vary considerably. The hoses provided are to
fit most tractor make and model applications. If the hoses
are too long, then coil up the excess carefully and fasten
with nylon tie-straps in a safe location. If the hoses prove
to be too short, then add a short section of good quality
hose with proper fittings.
A S S E M B LY A N D M O U N T I N G
(continued)
7. Remove the 2” hex nut (Ref. #15) from the top of the
main spindle and the washer (Ref. #16).
8. Set the moldboard head assembly in an upright posi-
tion and block securely.
Install the optional ratchet jack between the lugs on
the moldboard (Ref. #4) and the moldboard head
(Ref. #3) and adjust the jack so the head assembly is
vertical or block the head assembly into a vertical
position.
Grease the entire 3.0” diameter main pivot spindle.
9. Using a mechanical lift, raise the assembly of the 3
pt. hitch and swing arm above the blocked up mold-
board and head assembly.
Insert the parking stand (Ref. #18) in the square
socket provided and pin in the “up” position.
Now lower the swing arm onto the 3” diameter main
pivot spindle. Install the washer and secure with the
2” hex nut but allow the swing arm to pivot on the 3”
main spindle. Install the
3
/
8
” x 4” cotter pin (Ref. #12).
10. Install the mechanical adjustment links (optional) or
the hydraulic cylinders (4” x 16”) between the lugs
and pin.
NOTE: If using hydraulic cylinders, the offset control
cylinder should have the cylinder end pinned to the 3
pt. hitch and the rod end pin to the swing arm. The
moldboard angle control cylinder body end should be
pinned to the swing arm lug and the rod end pinned
to the plate on the moldboard head.
The 3” x 8” tilt cylinder should have the cylinder body
pinned to the moldboard head and the rod end to the
lug on the right hand side of the moldboard.
11. If you are using mechanical adjustment links, you
are ready to attach the blade to your tractor. If using
hydraulic cylinder, refer to the hydraulics section.
The XHB Series Rear Blades may be manually or
hydraulically controlled for offset, angle, and tilt.
The remote hydraulic cylinders (Accessory Equipment)
available from your Worksaver dealer are designed to be
used in conjunction with your tractor hydraulic system.
The cylinders and hoses are designed for a maximum
system pressure of 2500 PSI.
The owner may substitute his own double acting
hydraulic cylinders for main frame offset, moldboard
angle, and moldboard tilt adjustment in lieu of the
cylinders supplied by the dealer. HOWEVER, the recom-
mended cylinder specifications for main frame offset and
moldboard angle is 4” bore, 16” stroke ASAE with 2”
diameter rod. The clevis pins are 1.25” diameter. The
recommended cylinder specifications for the moldboard
tilt is 3” bore, 8” stroke ASAE with a 1.25” diameter rod
and 1.0” diameter clevis pins.
C A U T I O N !
Be sure your tractor is in good condition. Read all
the safety precautions and make sure all tractor
operators are familiar with the safety rules of
operation.
W A R N I N G !
Escaping hydraulic fluid under pressure can pene-
trate the skin, causing serious injury.
DO NOT use your hand to check for leaks. Use a
piece of cardboard or paper to search for leaks.
Stop engine and relieve pressure before connecting
or disconnecting lines.
Tighten all connections before starting engine or
pressurizing lines.
If any fluid is injected into the skin, obtain medical
attention immediately, or gangrene may result.
I N S T R U C T I O N S
13
I N S T R U C T I O N S
(continued)
14