Trouble shooting guide – Blagdon Pump B50 W1 User Manual
Page 6
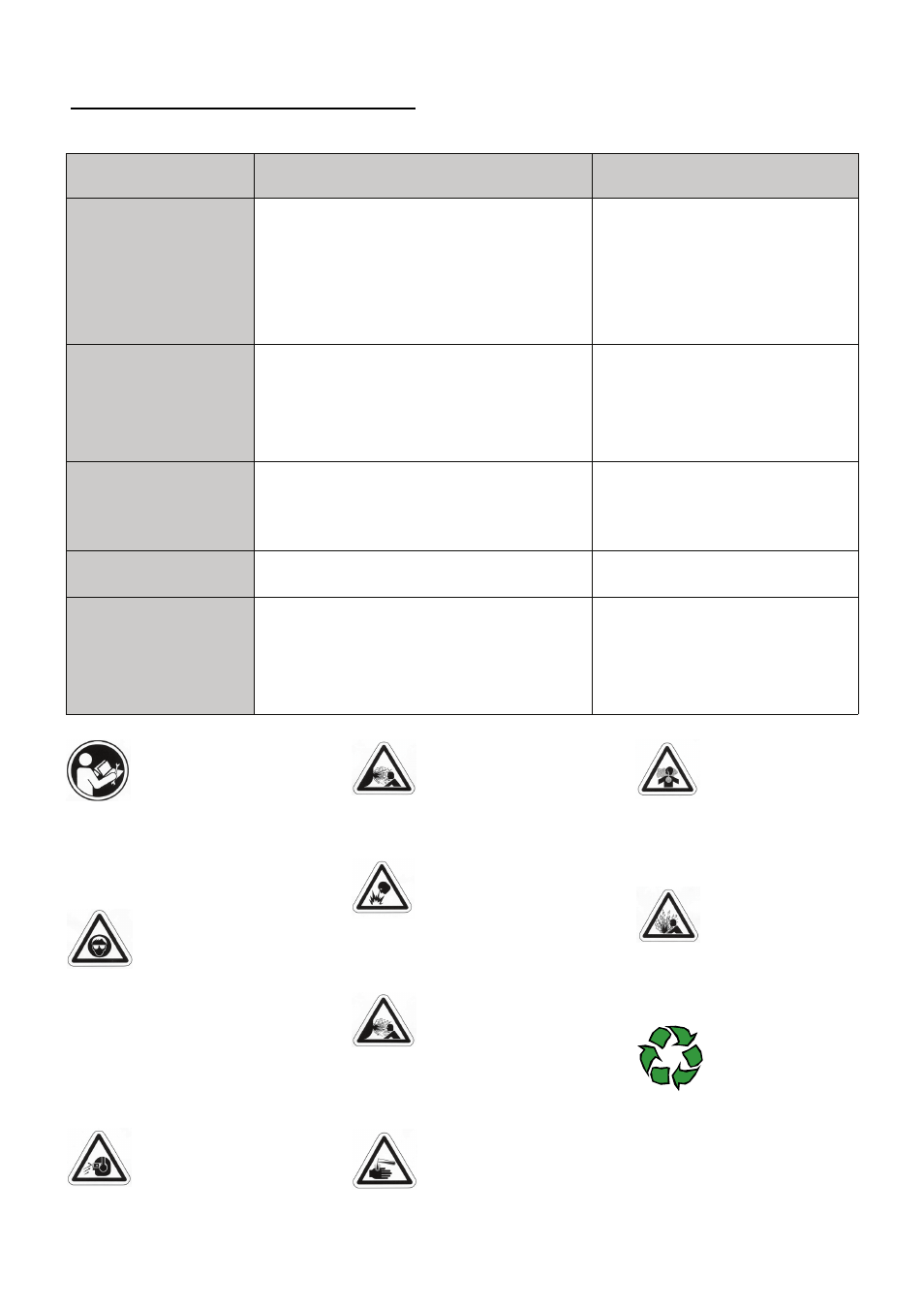
TROUBLE SHOOTING GUIDE
NOTE :- Check all solutions before dismantling the pump.
Read these safety warnings
and instructions in this manual
completely, before installation
and start-up of the pump. It is
the responsibility of the purchaser to retain
this manual for reference. Failure to comply
with the recommendations stated in this
manual will damage the pump, and void
factory warranty.
WARNING!
Before doing any maintenance
on the pump, be certain all
pressure is completely vented
from the pump, suction, discharge, piping,
and all other openings and connections. Be
certain the air supply is locked out or made
non-operational, so that it cannot be started
while work is being done on the pump. Be
certain that approved eye protection and
protective clothing are worn all times in the
vicinity of the pump. Failure to follow these
recommendations may result in serious
injury or death.
WARNING!
Before pump operation, in-
spect all gasketed fasteners
for looseness caused by gas-
ket creep. Re-torque loose fasteners to
prevent leakage. Follow recommended
torques stated in this manual.
CAUTION!
When used for toxic or
aggressive fluids, the pump
should always be flushed
clean prior to disassembly.
WARNING!
Take action to prevent static
sparking. Fire or explosion can
result, especially when
handling flammable liquids. The pump,
piping, valves, containers or other
miscellaneous equipment must be
grounded.
WARNING!
Before maintenance or repair,
shut off the com-pressed air
line, bleed the pressure, and
disconnect the air line from the pump. The
discharge line may be pressurized and must
be bled of its pressure.
WARNING!
This pump is pressurized
internally with air pressure
during operation. Always make
certain that all bolting is in good condition
and that all of the correct bolting is
reinstalled during assembly.
IMPORTANT!
In the event of diaphragm
rupture, pumped material may
enter the air end of the pump,
and be discharged into the atmosphere. If
pumping a product which is hazardous or
toxic, the air exhaust must be piped to an
appropriate area for safe disposition.
WARNING!
Airborne particles and loud
noise hazards. Wear ear and
eye protection.
WARNING!
RECYCLING
M a n y c o m p o n e n t s o f
BLAGDON air operated
double diaphragm pumps are
made of recyclable materials.
We encourage pump users to recycle worn
out parts and pumps whenever possible,
after any hazardous pumped fluids are
thoroughly flushed.
PROBLEM
CAUSE
SOLUTION
Pump will not start
Air valve assembly malfunction/Siezure
Obstructed fluid line.
Obstructed diaphragm chamber.
Diaphragm failure causing fluid & excessive air to be
expelled through the exhaust.
Diaphragm seal failure.
Air valve system malfunction.
Air connected to exhaust.
Check carrier for freedom of movement. -
Clean, re-grease & replace.
Clean line or increase line size.
Remove obstruction.
Replace diaphragm.
Replace shaft seals.
Check all seals in valve chest assembly.
Re-connect to air inlet.
Erratic flow
Diaphragm failure on one side.
Valve ball not seating.
Suction leakage.
Diaphragm failure causing fluid & excessive air to be
expelled through the exhaust.
Diaphragm seal failure.
Air valve system malfunction.
Replace diaphragm.
Check and remove obstruction.
Check and correct.
Replace diaphragm.
Replace shaft seals.
Check all seals in valve chest assembly.
Pump strokes but will not
discharge
Excessive suction lift.
Suction line leakage.
Valve ball not seating correctly or damaged.
Suction line or strainer clogged.
Diaphragm failure.
Shorten suction line.
Check and correct.
Check and remove obstruction / replace.
Clear.
Replace diaphragm.
Fluid discharged from air
exhaust
Diaphragm Failure.
Loose frontplate.
Replace diaphragm.
Re-Torque to manual specifications.
Intermittent stroke rate
Over lubrication
Diaphragm shaft seal failure.
Air valve system malfunction.
Valve ball not seating / partially obstructed.
Shut-down pump. Remove air connection
into pump & introduce a small quantity of de-
greasing agent into air valve and replace
line. Run pump until clear.
Replace seals.
Check all seals in valve chest assembly.
Clear obstruction.
HG-CF-1109 Rev. D – 03.11.11
Page 6