CONTREX CX-1102 User Manual
Page 4
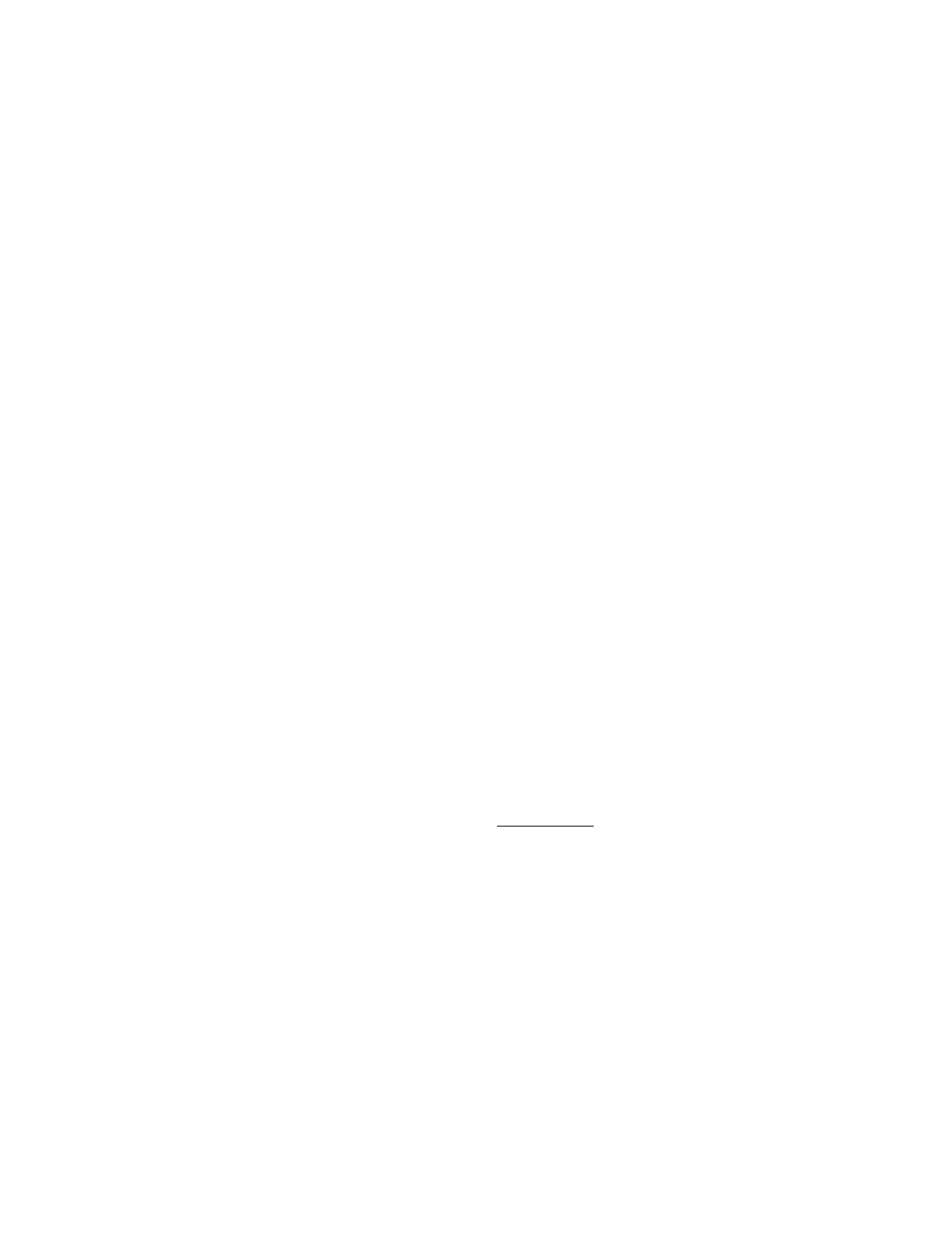
Page 2
•
Dancer Electrical Design: The analog electrical signal from the dancer should be stable, repeatable,
noise-free, and linear with respect to dancer movement. It can be a potentiometer, or some non-contact
analog sensor. Sonar or ultrasound detectors on a free loop web may not be acceptable due to
instability or low resolution.
The electrical signal does not necessarily have to traverse the entire 0 to 5 vdc range over the dancer
range of physical motion. It must traverse at least a 1 volt minimum electrical range, and more voltage
swing would improve resolution and accuracy of calculations.
•
Axle vs Surface encoders: Axle encoders are simpler to install, and usually have a more rugged
mounting location.
Surface traction-wheel or idler- roll mounted encoders may yield more accurate surface speeds, but are
more cumbersome to mount. Web-breaks, or web slippage can cause undesirable results.
•
Use of Traction-Wheel or Idler-Roll encoders: Choose “Fixed Diameter” configuration option, just
as though that axis is a fixed nip-roll design. A Traction-Wheel with a 1-foot circumference is entered
as a 3.82 inch diameter roll. (12 inch/
π
)
•
Roll RPM vs Motor RPM: The CX-1102 never asks how fast the motor can go. RPM always refers
to the speed of the roll axle. Please study the mechanical design of the machine to understand the gear
reduction between motor, encoder and roll axle. Only the top axle RPM, and the Gear Reduction from
encoder to axle are parameter entries in the CX-1102.
•
Accel/Decel Rates: Adjust the Accel/Decel rates in the motor drive (amplifier), on each axis, to their
fastest rates (shortest time), to allow the CX-1102 command signals to promptly generate a correct
response from the motor. However, adjust the Accel/Decel rates in the CX-1102 to more gentle ramps
to allow the dancer trim to work smoothly and effectively at startup.
•
Safety Stops/Inhibits/Enables: The CX-1102 has Drive Enable open collector outputs, to be used (via
pilot relays if needed) to enable/disable the motor drive. This is important since there are situations
where the CX-1102 is trying to hold an axle in a “live zero”, or “active stopped”, H-Stop state. At
other times the axis is turned off (disabled). While the drive enable function could be part of some
external process control scheme, it is best to let the CX-1102 control the drives as required by the
internal control algorithms. Having said this, also consider SAFETY. The CX-1102 stop commands
are solid state items. Overall system safety would require interlocked, external, pushbuttons, contacts,
etc. to effect a disconnect type of safety stop. CX-1102’s “live zero” may appear to be a stopped
condition, but would NOT be safe to enter the machine for thread-up, jam clearing, etc.
•
Web Stretch: Greatest accuracy is obtained with Non-extensible webs. Some minor (<2%) web
stretch, or shrinkage, is usually acceptable but may affect line speed accuracy. If web stretch is
expected, enter the anticipated stretch value into Stretch % (CP-220) to normalize the dancer trim
effect.
•
Unipolar (Non-reversible) Drives: The CX-1102 is typically used with bi-directional (reversible)
drives. It can accommodate unipolar drives (or brake in limited cases), only with appropriate design
considerations. The unipolar drive axis must have sufficient gearbox friction to prevent back-driving,
or overhauling loads. That is, it must prevent being pulled backwards, or pulled forwards faster than it
intended to go, due to web tension. Otherwise, the dancer position cannot be maintained properly.