Wwa ar rn niin ng g – CM-ET Lodestar User Manual
Page 26
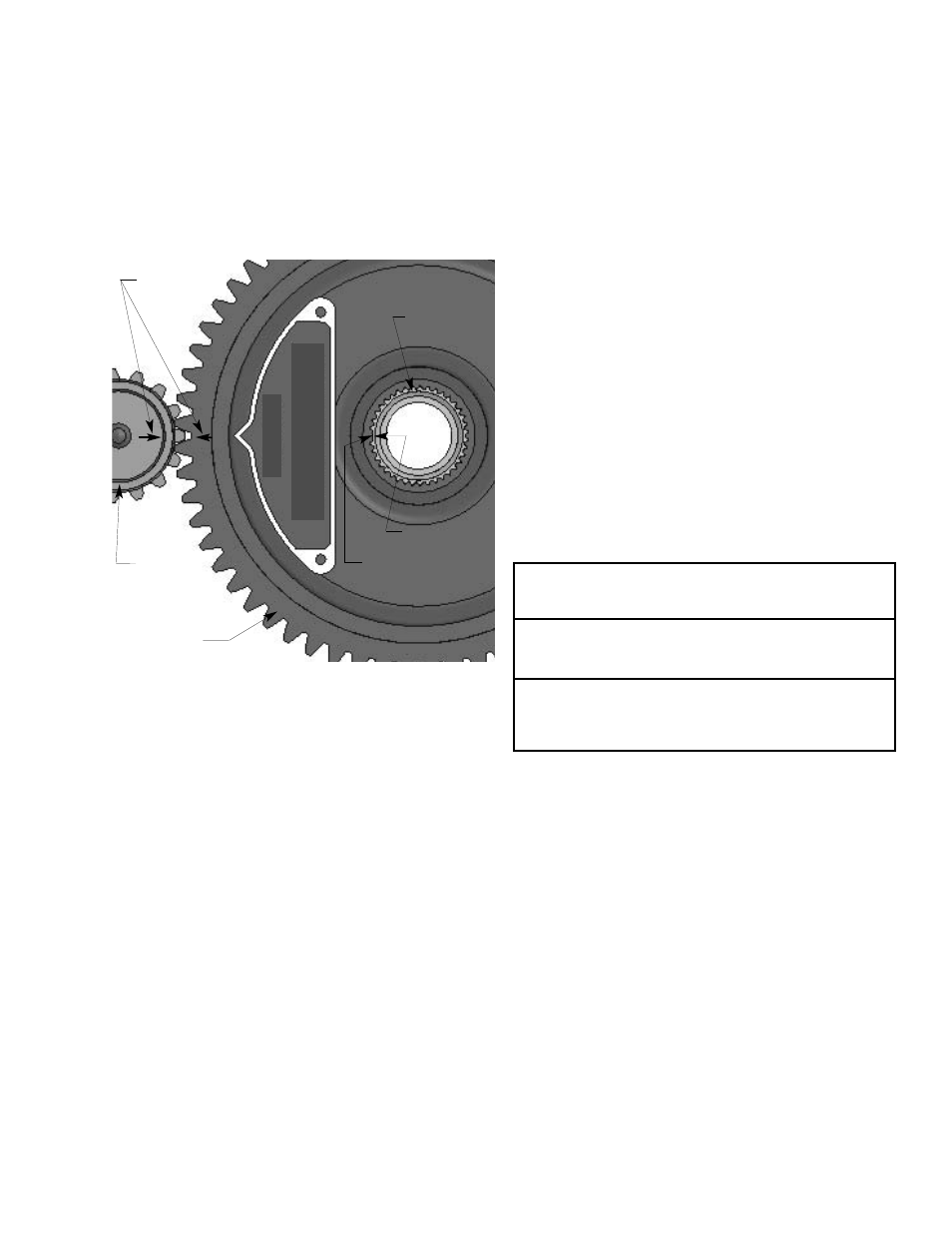
GEARING
Models LL & RR have a special Liftwheel Gear (627-303)
and Intermediate Pinion (627-325).
If the gear train in these hoists is disassembled, the following
steps must be observed in order to properly orient the three
parts when reassembling:
1. Assemble liftwheel gear to liftwheel.
NOTE: These parts have their splines keyed in such
a way that they will go together only one way. See
Figure 20.
Figure 22. Non-Circular Gearing
2. To install the intermediate pinion, align the arrows that
are stamped on the pinion and liftwheel gear so they
point toward each other.
3. Check operation of gear train by rotating the pinion four
(4) complete revolutions; liftwheel gear will turn one (1)
complete revolution and the arrows will again be aligned
as shown. If the arrows do not align or there is binding
between the gear teeth, repeat the above steps.
4. For gearing lubrication instruction, see page 16.
FASTENERS
Models B, C & F tighten motor housing cover screws (627-
108) to where they have a minimum breakaway torque of
5.423 Nm (48 pound inch) and the brake attaching screws
(627-253) have a 5.649 Nm (50 pound inch) minimum break-
away torque.
Models J, L, R, LL & RR tighten limit switch bracket attach-
ing screws (627-220), motor end bell attaching screws (627-
411), brake attaching screws (627-253) and hexagonal brake
stud (627-265) to where they have a minimum breakaway
torque of 5.649 Nm (50 pound inch). The liftwheel gear nut
(627-305) should be tighten to a seating torque of 115.245
Nm (85 pound feet).
LOWER HOOK BLOCK PIN
When removing or installing the lower hook pin (627-764),
care must be taken so as to prevent damaging the pin
and/or hook block. These pins are tapered groove pins and
as a result, they can only be removed in one direction. To
remove the pin, a V-Block, drift and hammer (or slow acting
press) are required. The drift should be the same diameter
as the pin (5/16” diameter (7.94mm) for Models B, C & F
and 3/8” (9.52mm) diameter for Models J, L, R, LL & RR,
and it should be placed on the small end of the pin. The
small end of the pin is the end opposite the end on which the
3 grooves are visible. Place the hook block in the V-Block
and drive the pin out using the drift and a hammer or slow
acting press.
To re-install the pin, the parts must be arranged the same as
they were when the pin was removed. To do this, use the
small end of the pin as a gage. First check the holes in the
hook block body and determine which hole is the largest.
Place the hook body in the V-Block with the larger hole on
top. Next, check each end of the hole in the lower hook
chain block (627-775) and determine which end is the
largest. Place the chain in the slot of the chain block and
insert the chain block, with the large hole on top, into the
hook block body. Align the holes in the hook block body with
the hole in the chain block and insert the small end of the pin
in the hole. Push the pin in by hande until it stops and then
use a hammer or slow acting press to drive the pin into posi-
tion so that the end of the pin is flush with the outside surace
of the hook block body.
22
W
WA
AR
RN
NIIN
NG
G
Use of improper lower hook chain block pin as well as
improper installation of the pin can cause the pin to break
and allow the load to fall.
T
TO
O A
AV
VO
OIID
D IIN
NJ
JU
UR
RY
Y A
AN
ND
D P
PR
RO
OP
PE
ER
RT
TY
Y D
DA
AM
MA
AG
GE
E::
Use only CM supplied, special high strength lower hook
chain block pin to attach the chain to the lower hook block
and install the pin as directed above.
V
!!
Intermediate
Pinion 627-325
Liftwheel Gear
627-303
Arrows Must Be
Aligned As Shown
Liftwheel
627-302
Missing Tooth Space
In Liftwheel Gear
Spline
Missing Tooth In
Liftwheel Spline
CAUTION
A
T
ASSEMBL
Y
ARROWS
ON
GEAR & PINION
MUST
LINE UP