Cr a – Zero-Max Stainless Steel Single flex six bolt Composite Disc Couplings User Manual
Page 2
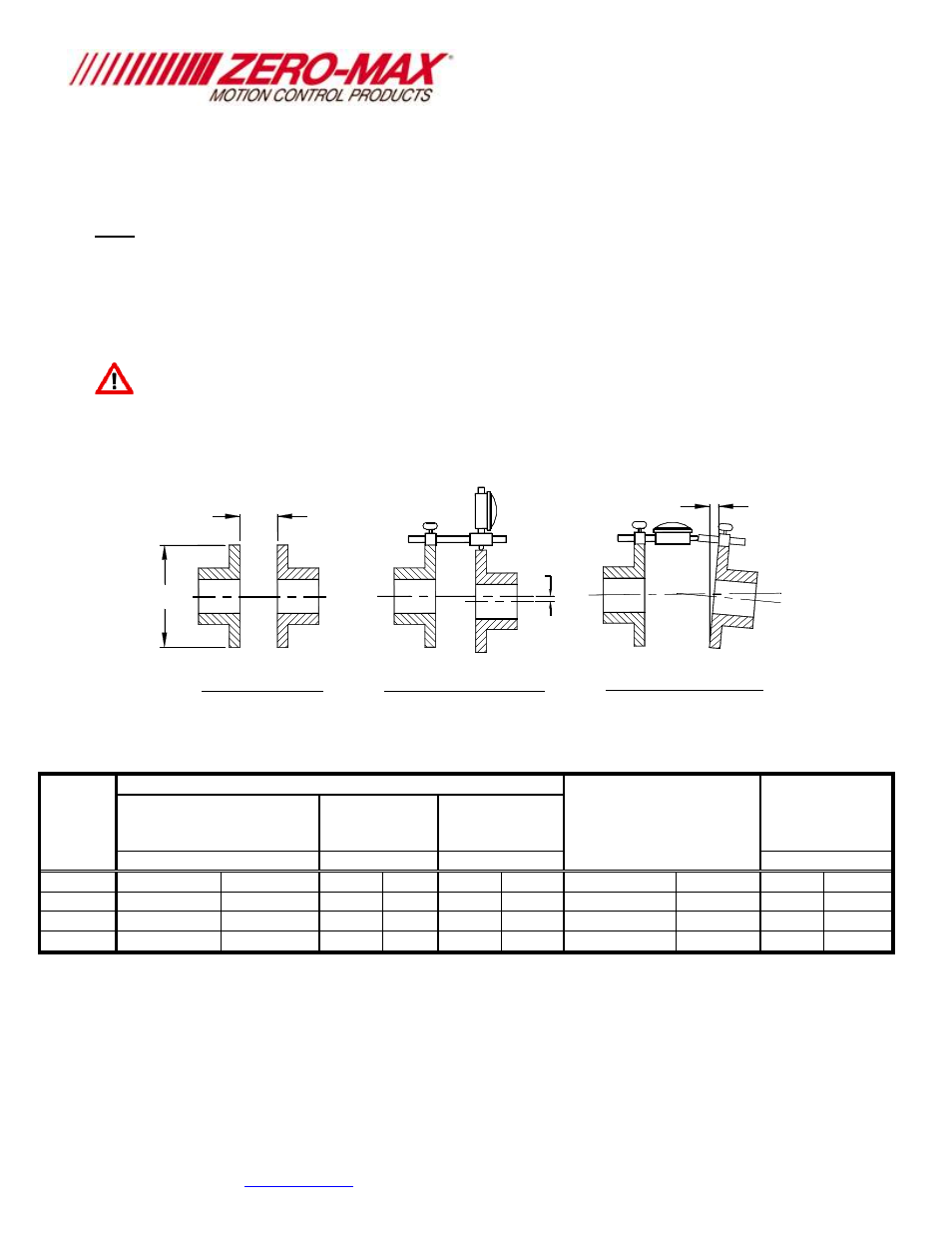
13200 Sixth Avenue North Minneapolis, MN 55441-5509 PHONE (763) 546-4300 FAX (763) 546-8260 DOC NO.: 6AXX-SS-INST Rev B
TOLL FREE 1-800-533-1731
www.zero-max.com
Revised on 5/2/12
8. Tighten the locknuts per the Table 1 tightening torque specifications. Tighten the locknuts of one hub, then those
of the other hub to approximately ½ the stated torque value. Next repeat the process but tightening to the full
torque value. It is also recommended to apply torque on the locknut, not the bolt. Re-check and tighten all
fasteners after several hours of operation to ensure proper tightening.
Note: Aligning the shafts as closely as possible at the time of initial installation will reduce noise and allow the
coupling extra capacity for misalignments and loads which will occur during operation over the life of the connected
equipment. Installing and operating the coupling at higher degrees of misalignment are possible, but will reduce
the life of the composite disc pack. Contact Zero Max with additional questions.
Coupling and shaft alignment should be checked periodically due to foundation settling, equipment shifting, etc.
Alignment should be re-checked after the first several hours of operation.
*Caution: Rotating equipment is potentially dangerous and should be properly guarded. It is the
responsibility of the machine builder, user or operator to follow all applicable safety codes and provide a
suitable guard. Make sure the machine is “locked out” and cannot be accidentally started during
installation or maintenance of coupling.
C ± X
A
R
DIAGRAM 2
CHECK PARALLEL MISALIGNMENT
DIAGRAM 1
CHECK ANGULAR MISALIGNMENT
DIAGRAM 3
CHECK HUB SEPARATION
Ø
D
Table 1
Alignment and Assembly Specifications for Stainless Steel Single Flex Series 6Axx-ss
Recommended maximum installed misalignments
Unit
C
R
A
Tightening Torque
Outside
Diameter
See Diagram 1
See Diagram 2
See Diagram 3
(Dry values)
D
Model
Inch
mm
Inch mm Inch mm
Inch mm
6A30-SS
0.460
0.017 11.680.43 0.003 0.08 0.026 0.66
95
in
lb
10.7Nm 3.00 76.2
6A37-SS
0.522
0.023 13.260.58 0.004
0.10
0.033
0.83
230 in lb
26 Nm
3.75
95.3
6A45-SS
0.582
0.030 14.780.76 0.005
0.13
0.039
1.00
38 ft lb
51 Nm
4.50
114.3
6A52-SS
0.646
0.037 16.410.94 0.006
0.15
0.046
1.20
38 ft lb
51 Nm
5.25
133.4
C