Electric drive motor, Leveler leg, Controls – atwood Landing Legs User Manual
Page 2: Switches
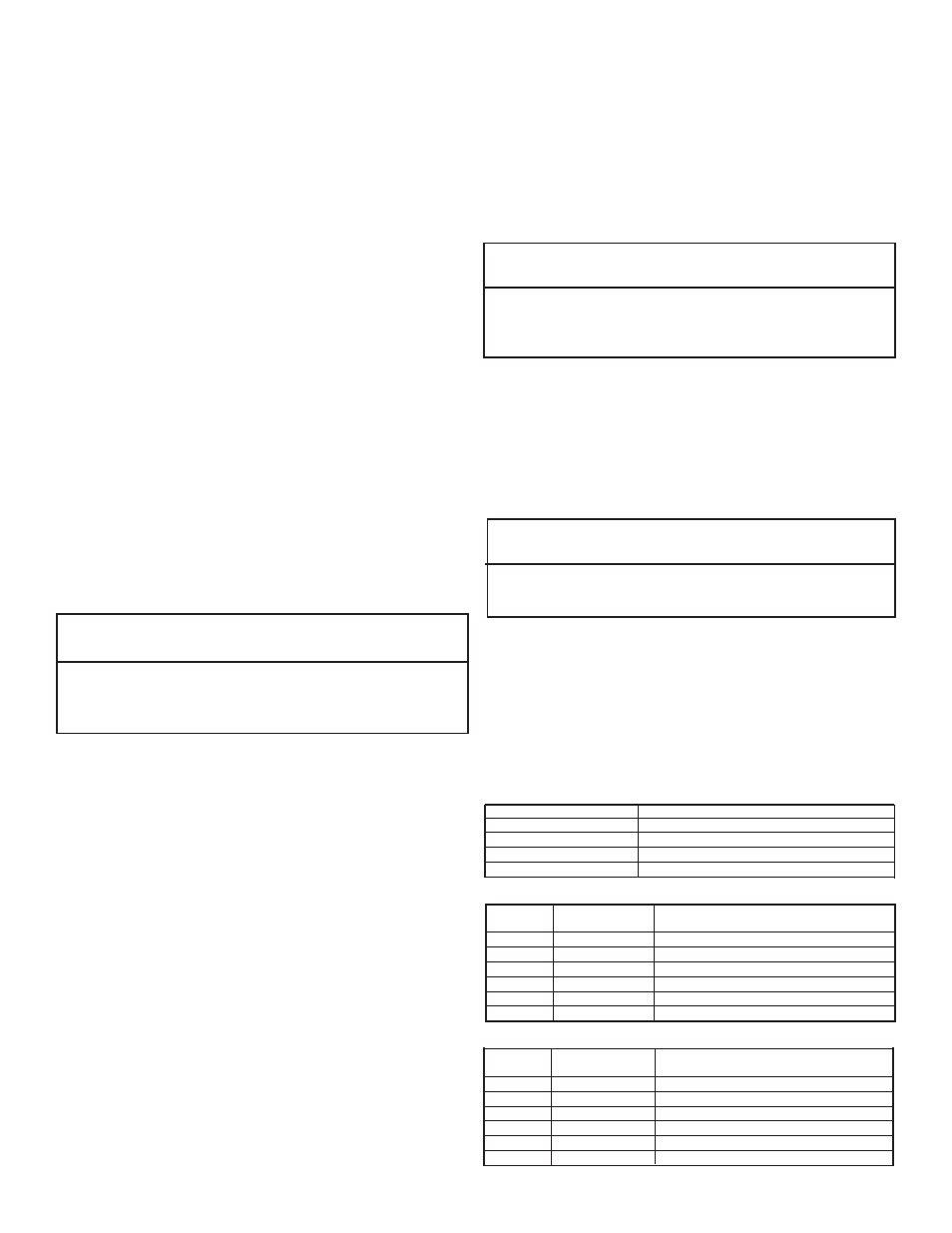
2
driven leg with 1/4˝ x 1-1/8˝ long screw and lock nut. To prevent rattle
between tubes, tack weld 1˝ square tube to 3/4˝ square tube (
FIG
3-F).
10.
NOTE
: Two motor landing leg sets may not need an outside access
point for the manual override if you orient the legs so the drive
shaft faces forward (toward the compartment door) or inward.
Mark location for hand crank hole through frame (
FIG
5-A) and side
wall (
FIG
5-B) and drill 1-3/32˝ minimum diameter hole for structural
composite flange alignment tube (
FIG
4-B &
FIG
5). Slide alignment
tube (
FIG
5-C) through hole and over drive pin in crank shaft until it
contacts the gear box (
FIG
5-D or 1-B). Attach flange (
FIG
5-E) of
alignment tube to side wall with the three #8 sheet metal screws. If
flange does not contact the side wall, shorten alignment tube to allow
a flush fit. Use a tube cutter to shorten tube. Orient the weep hole on
the flange so it is on the bottom.
NOTE
: On open frame trailers, build a bracket to hold the alignment tube
(
FIG
3-G).
11. Check operation of landing legs by inserting slotted end of handle
through alignment tube and engage the end of landing leg crank
shaft. Rotate crank handle counter-clockwise. Check to see if both
legs are extending equally.
Electric Drive Motor
NOTE
: Use the Atwood Electric Motor on Atwood 5th Wheel Landing
Legs only. Do not use on other manufacturer’s legs. The Direct Drive
legs already have the motor installed.
1.
LANDING LEGS
: The 12VDC electric drive motor must be installed on
the inside of the gear box located on the same side of the trailer from
which the landing legs are now hand cranked (
FIG
1). Two motor sets
will have a motor on each leg.
2. Put slotted coupling of motor over end of shaft (
FIG
1-A) on gear box.
3. Secure motor to gear box with two 1/4˝ dia. x 3-1/2˝ long rounded slot-
ted head machine screws (
FIG
1-D). Thread screws into the two tapped
holes in gear box. Use lock washers (
FIG
1-E) under screw heads.
ƽ
WARNING
VEHICLE CAN MOVE OR COLLAPSE
• Never exceed the rated capacity of the leveler as stated on its label.
• Levelers are not designed to be used as jacks. Do not use levelers
to lift the vehicle during tire changes, axle work or other servicing.
The tires must stay on the ground.
Leveler Leg
1. Prior to installation, retract the levelers so the foot pads are within
1/2˝ to 1˝ from the end of the outer housing (
FIG
6-A).
2. Position leveler vertically against frame so base of foot is above the
departure angle when vehicle is loaded to its maximum GVWR (
FIG
6-
B). The departure angle is an imaginary line between the bottom of
the tires and the bottom of the rear bumper.
3.
FOR SQUARE TUBE LEVELEGS
TM
, weld the frame bracket (
FIG
6-E) to frame
(
FIG
6-F). Fit the Leveleg bracket (
FIG
6-G) around the Leveleg, engag-
ing one tab below the bracket (
FIG
6-J) and the other tab above the
bracket (
FIG
6-K). Attach the Leveleg bracket to the frame bracket
with a 3/8˝ carriage bolts and 3/8˝ nuts.
4. Lubricate the bolts and torque to 20 ft-lbs.
5.
CROSS BRACE ATTACHMENT
- Attach top cross brace brackets (
FIG
6-L) to
each landing leg under the tab on the landing leg using 3/8˝ carriage
bolts and 3/8˝ nuts and torque to 20 ft-lbs. Have top cross brace
brackets facing opposite directions. Attach each cross brace tube to
each attached bracket using the 5/16-18 bolts and nuts. Do not tight-
en the bolts and nuts. Let the other ends of the tubes rest on the foot
of the opposite landing leg. Put 5/16-18 bolt thru center of cross
brace tubes and put the nut on the bolt, but do not tighten. Place
lower cross brace bracket (
FIG
6-M) on landing leg facing the oppo-
site direction as the top cross brace bracket that is on that landing
leg. Slide the lower bracket up and attach the cross brace tube end
to the cross brace bracket with
5/16-18 bolt and nut. Put 3/8˝ carriage bolts and nuts on cross brace
brackets and tighten to 20 ft-lbs. Insure lower brackets do not prevent
landing leg from fully retracting. Tighten all 5/16-18 nuts to 12 ft-lbs.
6. Consult MPD 87920 for wiring instructions and integration with
remote controls.
Controls
REMOTE CONTROL
2-motor and 4-motor Remote Control Systems are available to use in place
of switches. Installation and Operation instructions refer to MPD 87920.
SWITCHES
ƽ
WARNING
EXPLOSION
• Most switches are not ignition protected. DO NOT install these in
areas which require ignition protected devices (such as battery or
propane tank storage compartments). Only the Ignition Protected
Switch is approved for installation in these compartments.
1. Choose a smooth, flat surface on which to mount the electrical
switch. Protect from environment by mounting inside an access door
or protected exterior surface. Cut and deburr hole in panel through
which wires will pass. Protect wires from edge of hole by using
grommets or strain relief bushing (not furnished). Installing the
switch on an uneven surface (for example “Mesa” aluminum siding)
can cause binding between switch panel and switch. This binding
can cause switch to stick. Make sure the switch panel does not bind
or pinch the switch body.
ƽ
WARNING
MOVING PARTS CAN CRUSH OR CUT
• Switches must be located so operator can not operate landing legs
and be in contact with moving parts of cross shaft or motor at the
same time.
2. For the single switch, cut either a rectangular hole or a 1-5/8˝ dia.
hole. For the three switch panel, cut a 5-1/2˝ wide by 2-3/4˝ tall
opening. Pass wires through hole from front.
3. Remove fuse from fuse holder until installation is complete and all
connections are made.
4. Position panel with the gasket side against the mounting surface. It
is recommended to use sealing screws to prevent moisture intrusion.
Do not cut the wire tie located under the heat shrink tubing. Wires
will spread and can pull off the terminals.
LANDING GEAR SINGLE SWITCH WIRING CHART
LENGTH
-
WIRE COLOR
POINT OF TERMINATION
48
˝
RED
-
FUSE & HOLDER
+
12VDC BATTERY TERMINAL
48
˝
BLACK
CHASSIS GROUND OR
-
BATTERY TERMINAL
84
˝
RED
RED MOTOR LEAD
84
˝
BLACK
YELLOW MOTOR LEAD
LANDING GEAR THREE SWITCH WIRING CHART
LENGTH
WIRE COLOR
WIRE NOMENCLATURE
POINT OF TERMINATION
24
˝
RED
+
DRIVER MOTOR
RED MOTOR LEAD OF DRIVER SIDE LANDING LEG
24
˝
BLACK
-
DRIVER MOTOR
YELLOW MOTOR LEAD OF DRIVER SIDE LANDING LEG
24
˝
BLACK
BATTERY GROUND
CHASSIS GROUND OR
-
BATTERY TERMINAL
24
˝
RED
+
12 VDC BATTERY
POSITIVE
+
12 VDC BATTERY TERMINAL
24
˝
BLACK
-
PASSENGER MOTOR
YELLOW MOTOR LEAD OF PASSENGER SIDE LANDING LEG
24
˝
RED
+
PASSENGER MOTOR
RED MOTOR LEAD OF PASSENGER SIDE LANDING LEG
DIRECT DRIVE LANDING GEAR THREE SWITCH WIRING CHART
LENGTH
WIRE COLOR
WIRE NOMENCLATURE
POINT OF TERMINATION
24
˝
RED
+
DRIVER MOTOR
YELLOW MOTOR LEAD OF DRIVER SIDE LANDING LEG
24
˝
BLACK
-
DRIVER MOTOR
RED MOTOR LEAD OF DRIVER SIDE LANDING LEG
24
˝
BLACK
BATTERY GROUND
CHASSIS GROUND OR
-
BATTERY TERMINAL
24
˝
RED
+
12 VDC BATTERY
POSITIVE
+
12 VDC BATTERY TERMINAL
24
˝
BLACK
-
PASSENGER MOTOR
RED MOTOR LEAD OF PASSENGER SIDE LANDING LEG
24
˝
RED
+
PASSENGER MOTOR
YELLOW MOTOR LEAD OF PASSENGER SIDE LANDING LEG