Gorman-Rupp Pumps PAV3C60C-B-E10 575/3 All serial numbers User Manual
Page 48
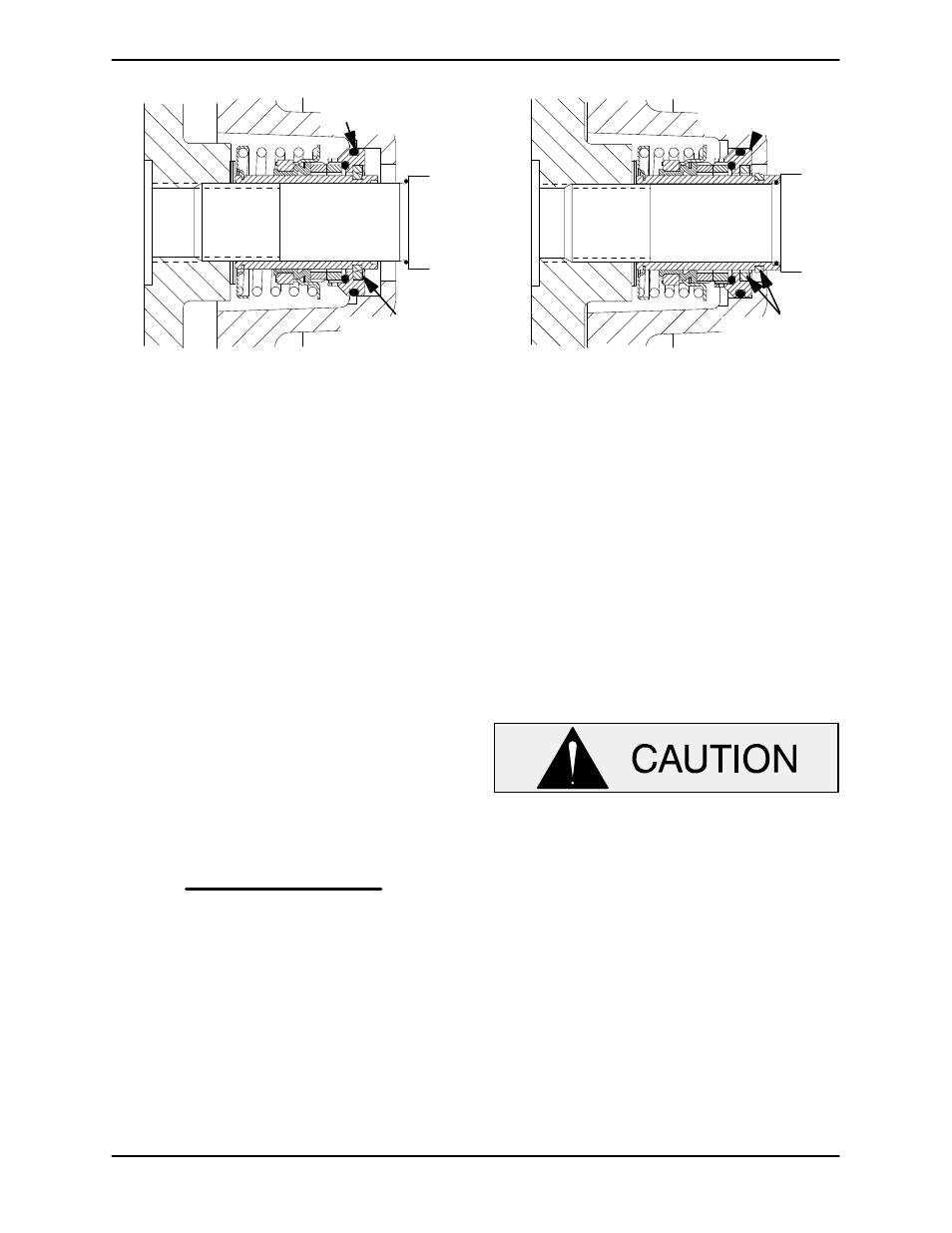
OM-06502
PA SERIES
MAINTENANCE & REPAIR
PAGE E - 21
O‐RING ENGAGED
WITH SEAL PLATE
BORE
SHEAR RING
(UNSHEARED)
Figure 10. Seal Partially Installed
Immobilize the impeller shaft by wedging a block of
wood between one of the impeller vanes and the
ground.
Install the impeller washer (23). Apply a small
amount of `Never‐Seez' or equivalent anti‐lock
compound on the threads of the impeller screw
(23) and use the impeller screw to press the impel
ler onto the shaft. This action will press the station
ary seat into the seal plate bore.
NOTE
A firm resistance will be felt as the impeller presses
the stationary seat into the seal plate bore.
As the stationary seat becomes fully seated, the
seal spring compresses, and the shaft sleeve will
break the nylon shear ring. This allows the sleeve
to slide down the shaft until seated against the
shaft shoulder. Continue to use the impeller screw
to press the impeller onto the shaft until the impel
ler, shims and sleeve are fully seated against the
shaft shoulder (see Figure 11).
STATIONARY SEAT
FULLY SEATED IN
SEAL PLATE BORE
SHEAR RING
(SHEARED)
Figure 11. Seal Fully Installed
A clearance of .025 to .040 inch (0,64 to 1,02 mm)
between the impeller and the seal plate is recom
mended for maximum pump efficiency. Measure
this clearance and add or remove impeller adjust
ing shims as required.
Torque the impeller screw to 90 ft. lbs. (12,4 m.
kg.).
Remove the wood block used to prevent shaft rota
tion.
If necessary to reuse an old seal in an emer
gency, carefully separate the rotating and station
ary seal faces from the bellows retainer and sta
tionary seat.
A new seal assembly should be installed
any time the old seal is removed from the
pump. Wear patterns on the finished faces
cannot be realigned during reassembly.
Reusing an old seal could result in prema
ture failure.
Handle the seal parts with extreme care to prevent
damage. Be careful not to contaminate precision
finished faces; even fingerprints on the faces can
shorten seal life. If necessary, clean the faces with a
non‐oil based solvent and a clean, lint‐free tissue.
Wipe lightly in a concentric pattern to avoid
scratching the faces.
Carefully wash all metallic parts in fresh cleaning
solvent and allow to dry thoroughly.