Gorman-Rupp Pumps PAV3B60C-3TNV70 1433753 and up User Manual
Page 39
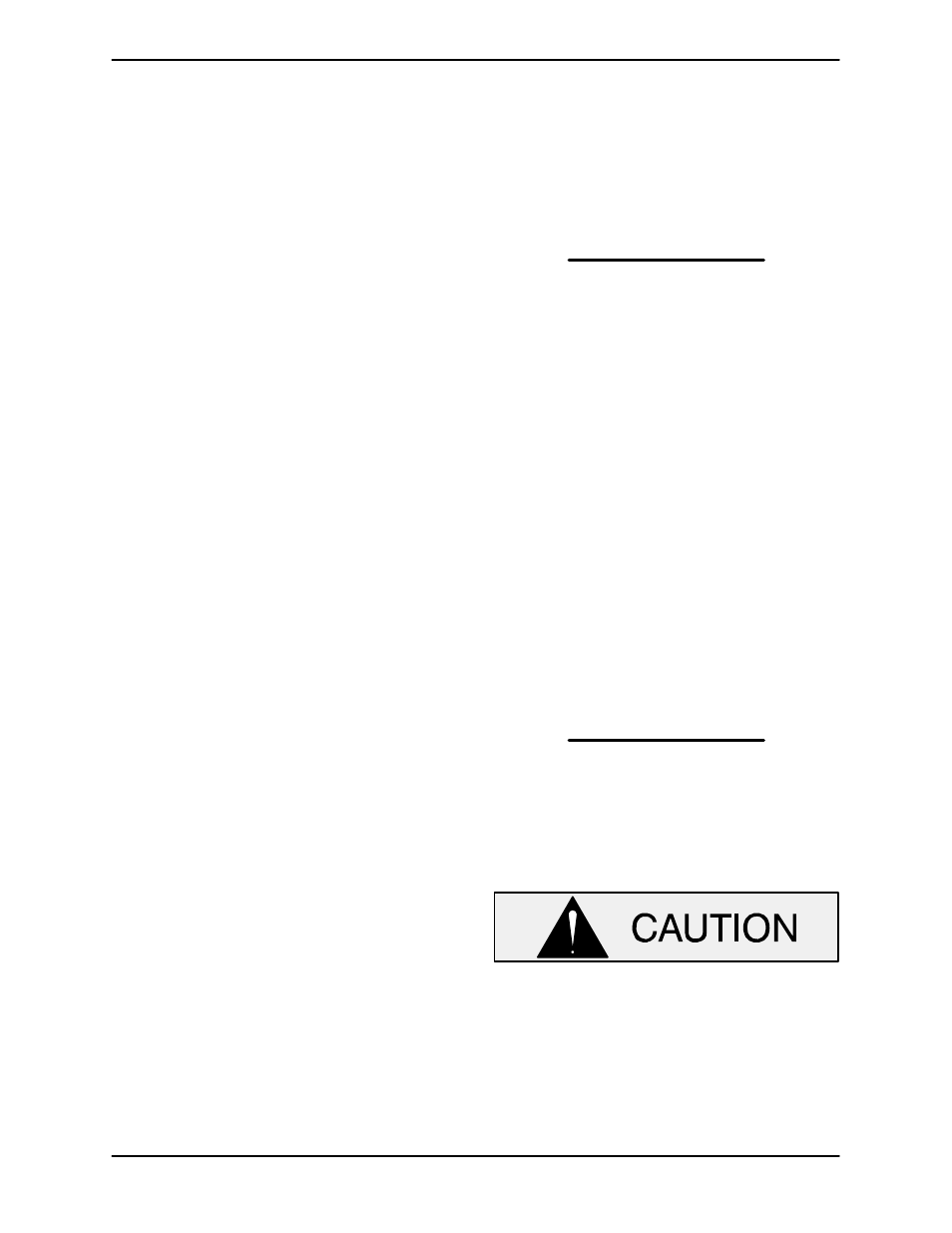
OM-06260
PA SERIES
MAINTENANCE & REPAIR
PAGE E - 21
Position the flap valve adaptor in the mounting slot
in the flange and secure the assembly with the
check valve pin (16).
Reinstall a new flange gasket (21). Apply “Loctite
No. 242 Threadlocker” or equivalent compound on
the threads of the the studs (25) in the discharge
elbow. Lower the discharge elbow over the flange
and pump casing and slide the studs down
through the holes. Secure the parts with the hard
ware (5 and 37).
Priming Hopper Reassembly And Installation
(Figures 2 and 6)
Clean and inspect the components of the priming
valve. Inspect the linkage and ensure the orifice
button squarely engages the valve seat. Replace
the orifice button if required (see Priming Cham
ber Removal and Disassembly for orifice button
removal).
Gorman‐Rupp provides replacement parts for the
cover gasket and the orifice button. If any of the
other priming valve components are worn or dam
aged, they must be replaced before reinstalling the
priming chamber. For additional parts and service
instructions for the valve, Contact the Val‐Matic
Valve and Manufacturing Corporation, or go to
www.valmatic.com on the World Wide Web. Ref
erence Val‐Matic Model Number 25.5.
After servicing the priming valve components, rein
stall the priming valve cover gasket and secure the
cover to the valve body with the previously re
moved hardware.
Clean the strainer screen (8) and install it in the
suction spool. Install the priming hopper gasket (4)
and secure the priming hopper and hopper cap
(10) to the suction spool with the previously re
move hardware (11 and 12).
Reconnect the air discharge tubing to the priming
chamber assembly.
LUBRICATION
(Figure 4)
Seal Assembly
Before starting the pump, remove the vented plug
(16) and fill the seal cavity with approximately 36
ounces (1 liter) of SAE No. 30 non‐detergent oil or
to the center of the sight gauge (23A). Clean and
reinstall the vented plug. Maintain the oil level at the
middle of the sight gauge.
NOTE
The white reflector in the sight gauge must be posi
tioned horizontally to provide proper drainage.
Bearings
(Figure 4)
The bearing housing was fully lubricated when
shipped from the factory. Check the oil level regu
larly through the sight gauge (23)
and maintain it at
the midpoint of the gauge. When lubrication is re
quired, remove the pipe plug (14) from the elbow
(15) and add SAE No. 30 non‐detergent oil through
the opening. When lubricating a dry (overhauled)
intermediate, fill the bearing cavity with approxi
mately 15 ounces (0,44 liter) of oil, or to the middle
of the sight gaute (23). Clean and reinstall the pipe
plug. Do not over‐lubricate the bearing housing.
Over‐lubrication can cause the bearings to over‐
heat, resulting in premature bearing failure.
NOTE
The white reflector in the sight gauge must be posi
tioned horizontally to provide proper drainage.
Under normal conditions, drain the bearing hous
ing once each year and refill with clean oil. Change
the oil more frequently if the pump is operated con
tinuously or installed in an environment with rapid
temperature change.
Monitor the condition of the bearing lubri
cant regularly for evidence of rust or mois
ture condensation. This is especially im
portant in areas where variable hot and
cold temperatures are common.
For cold weather operation, consult the factory or a
lubricant supplier for the recommended grade of
oil.