Gorman-Rupp Pumps T6A65S-B /F,/FM User Manual
Page 14
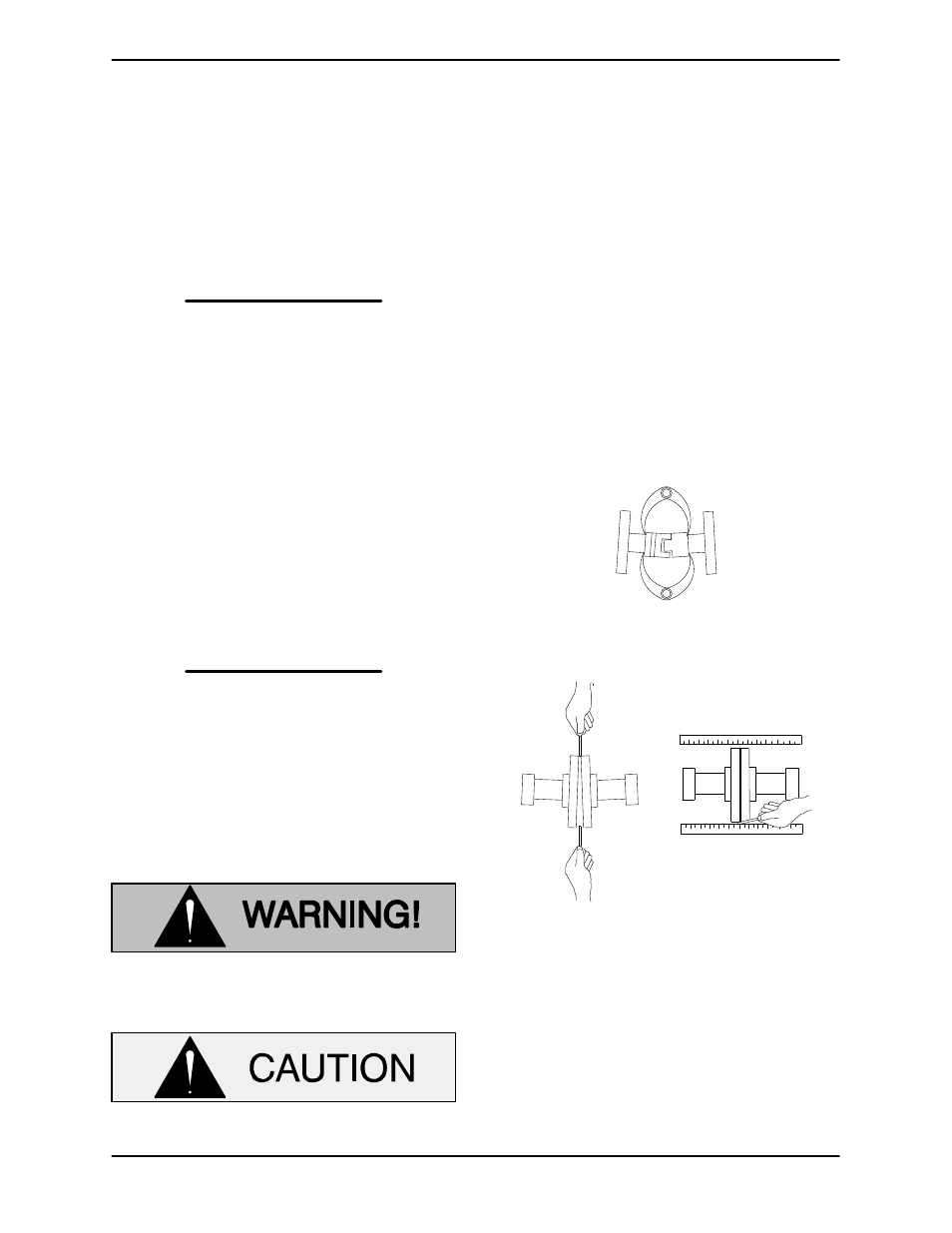
OM-05453
SUPER T SERIES
PAGE B - 7
INSTALLATION
NOTE
For multiple pump installations, it is recommended
that each Air Release Valve be fitted with an inde
pendent bleeder line directed back to the wet well.
If multiple Air Release Valves are installed in a sys
tem, do not direct bleeder lines to a common mani
fold pipe. Contact your Gorman‐Rupp distributor or
the Gorman‐Rupp Company for information about
installation of an Automatic Air Release Valve for
your specific application.
ALIGNMENT
The alignment of the pump and its power source is
critical for trouble‐free mechanical operation. In
either a flexible coupling or V‐belt driven system,
the driver and pump must be mounted so that their
shafts are aligned with and parallel to each other. It
is imperative that alignment be checked after the
pump and piping are installed, and before opera
tion.
NOTE
Check Rotation, Section C, before final alignment
of the pump.
When mounted at the Gorman‐Rupp factory, driver
and pump are aligned before shipment. Misalign
ment will occur in transit and handling. Pumps
must be checked and realigned before operation.
Before checking alignment, tighten the foundation
bolts. The pump casing feet and/or pedestal feet,
and the driver mounting bolts should also be tightly
secured.
When checking alignment, disconnect
the power source to ensure that the
pump will remain inoperative.
Adjusting the alignment in one direction
may alter the alignment in another direc
tion. check each procedure after altering
alignment.
Coupled Drives
When using couplings, the axis of the power
source must be aligned to the axis of the pump
shaft in both the horizontal and vertical planes.
Most couplings require a specific gap or clearance
between the driving and the driven shafts. Refer to
the coupling manufacturer's service literature.
Align spider insert type couplings by using calipers
to measure the dimensions on the circumference
of the outer ends of the coupling hub every 90
_.
The coupling is in alignment when the hub ends
are the same distance apart at all points (see Fig
ure 4).
Figure 4. Aligning Spider‐Type Couplings
Figure 5. Aligning Non‐Spider Type Couplings
Align non‐spider type couplings by using a feeler
gauge or taper gauge between the coupling halves
every 90
_. The coupling is in alignment when the
hubs are the same distance apart at all points (see
Figure 5).
Check parallel adjustment by laying a straightedge
across both coupling rims at the top, bottom, and
side. When the straightedge rests evenly on both
halves of the coupling, the coupling is in horizontal