Gorman-Rupp Pumps 12B22-B 1059806 thru 1343819 User Manual
Page 29
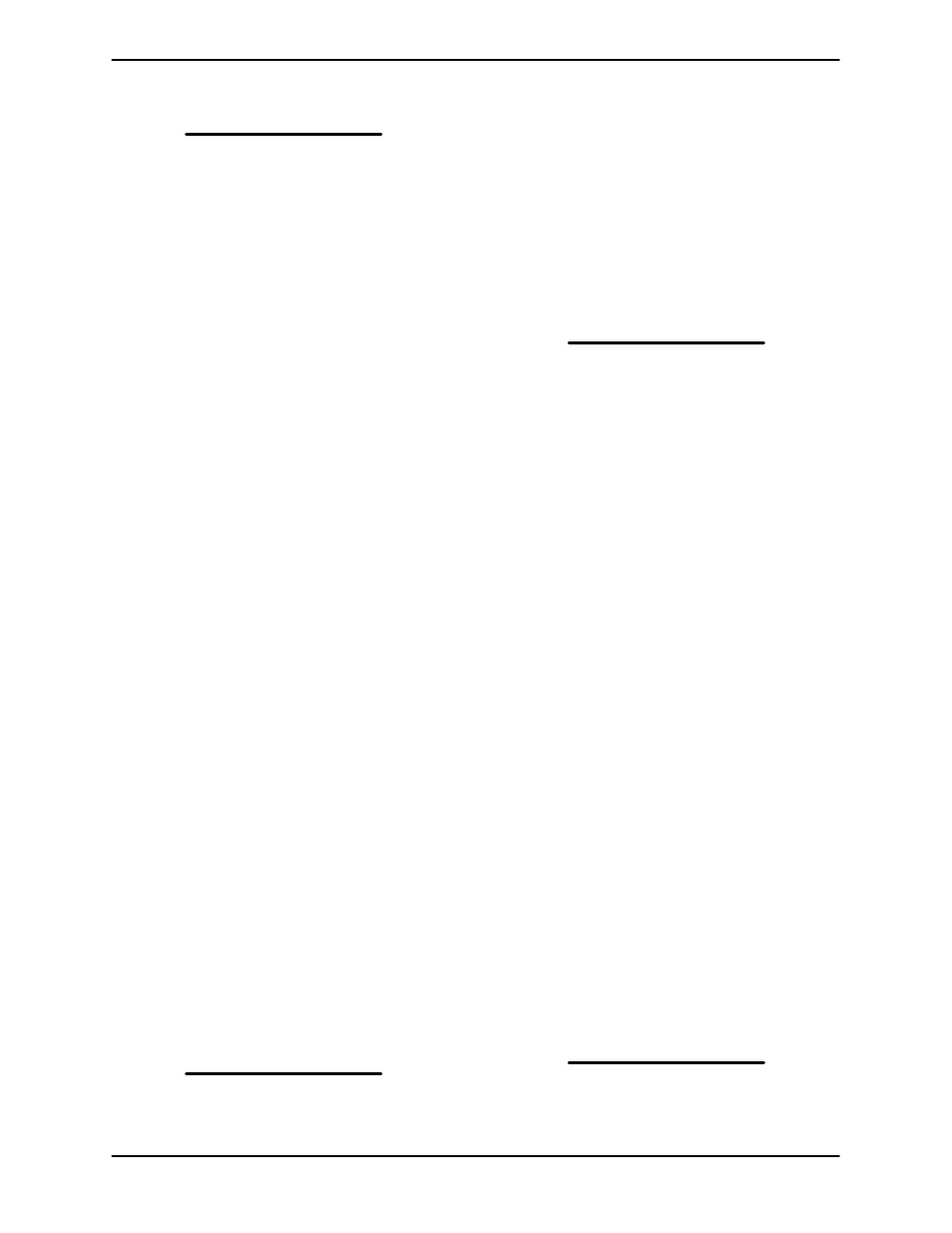
OM--00589--03
10 SERIES
MAINTENANCE & REPAIR
PAGE E -- 9
the O-ring, seal seat and seal face before installa-
tion.
Slide the seal plate over the shaft until fully seated
against the pedestal (25).
Be careful not to dam-
age the oil seal lip on the shaft threads.
Align the threaded seal lubricant hole with the ped-
estal opening and temporarily secure the seal p
late using two capscrews and nuts (3/8---16 UNC X
1 1/2 inch long, not supplied).
Slide the rotating subassembly (consisting of the
rotating element, retainer and bellows) onto the lu-
bricated shaft sleeve until the rotating element is
just flush with the chamfered end of the sleeve.
Slide the sleeve and rotating subassembly onto
the shaft until the seal elements contact. Continue
to push the sleeve through the seal until it bottoms
against the shaft shoulder.
Be careful not to dam-
age or roll the lips of the oil seal (31). Install the seal
spring and spring centering washer.
Lubricate the seal assembly as indicated in
LUBRICATION, after the impeller has been in-
stalled.
Impeller Installation And Adjustment
Inspect the impeller, and replace it if cracked or
badly worn. Install the same thickness of impeller
shims (62) as previously removed, and screw the
impeller onto the shaft until tight.
A clearance of .020 to .040 inch (0,51 to 1,02 mm)
between the impeller and the seal plate is neces-
sary for maximum pump efficiency. Measure this
clearance and add or remove impeller shims until
this clearance is reached.
NOTE
Be sure the seal plate is tight against the pedestal
while measuring this clearance.
Install the bottle oiler and piping (49, 50, 51, and
52).
Pump Casing Installation
Remove the hardware temporarily securing the
seal plate (35) to the pedestal (25). Install the same
thickness of pump casing gaskets (36) as pre-
viously removed, and secure the pump casing (1)
to the seal plate and pedestal with the nuts (34).
Do
not fully tighten the nuts at this time.
NOTE
The back cover assembly must be in place to adjust
the impeller face clearance.
A clearance of .008 to .015 inch (0,20 to 0,38 mm)
between the impeller and the wear plate (24) is also
recommended for maximum pump efficiency. Set
this clearance by adding or removing gaskets in
the pump casing gasket set (36) until the impeller
scrapes against the wear plate when the shaft is
turned. After the impeller scrapes, add approxi-
mately .008 inch (0,20 mm) of gaskets.
After the face clearance has been set, tighten the
nuts (34) securing the pump casing to the pedes-
tal.
Back Cover Installation
If the wear plate (38) was removed for replace-
ment, secure it to the cover plate (43) using the at-
taching hardware (39 and 40) at this time. The wear
plate must be concentric to prevent binding when
the back cover assembly (42) is installed.
Clean any scales or debris from the contacting sur-
faces on the pump casing that might prevent a
good seal with the back cover. Replace the back
cover gasket (41) and slide the back cover assem-
bly into the pump casing. Be sure the wear plate
does not scrape against the impeller.
NOTE
To ease future disassembly, apply a film of grease
or ‘Never-Seez’ on the back cover shoulder, or any
surface that contacts the pump casing. This action
will reduce rust and scale build-up.
Secure the back cover assembly by installing the
clamp bar (48) and tightening the clamp bar screw
(47).
Do not over-tighten the clamp bar screw; it