Gorman-Rupp Pumps 86A2-F3L 1257390 thru 1330588 User Manual
Page 32
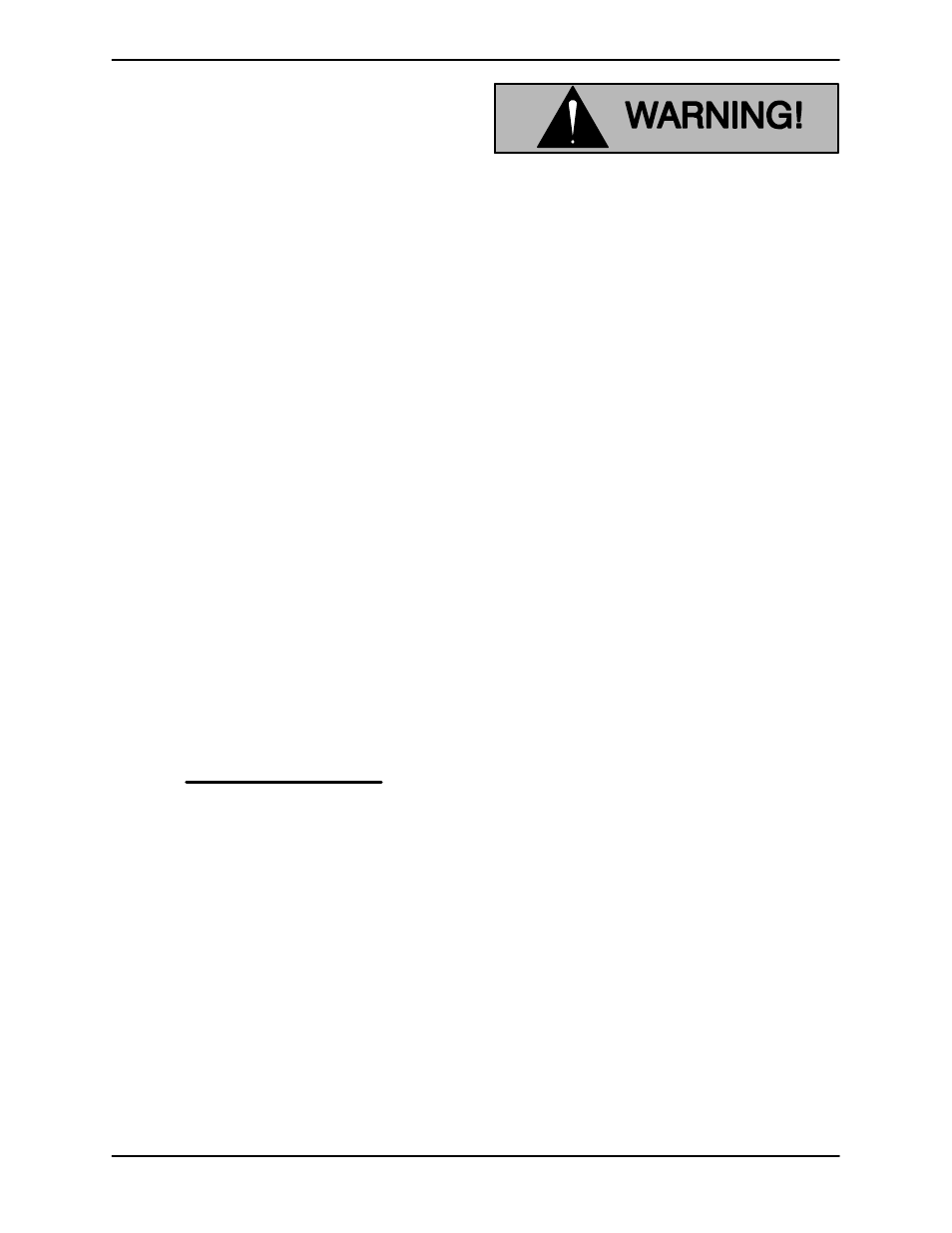
OM--00955
80 SERIES
MAINTENANCE & REPAIR
PAGE E -- 11
The end of the shaft must be
just flush with
the face of the bushing. This will allow the
two portions of the coupling to fully engage
when the intermediate is secured to the en-
gine bellhousing, without pre-loading the
bearings.
With the flexible portion of the coupling and the
bushing properly positioned on the shaft, tighten
the two setscrews in an alternating sequence until
the bushing and coupling are fully secured. Torque
the setscrews to 14.6 ft. lbs. (175 in. lbs. or 2,02 m.
kg.).
If the complete coupling assembly is being re-
placed, apply ‘Loctite Retaining Compound No.
242’ or equivalent compound to the threads of the
hardware (4 and 5), and secure the outer ring of the
coupling to the engine flywheel by torquing the
hardware to 45 ft. lbs. (540 in. lbs. or 6,2 m. kg.).
Using a suitable lifting device, position the interme-
diate (21, Figure 2) so the flexible portion of the
coupling seats inside the outer ring attached to the
engine flywheel.
NOTE
To ease installation,
lightly lubricate the rubber por-
tion of the coupling with a
non-petroleum based
lubricant such as vegetable oil or glycerin, or a sili-
con-based lubricant such as “WD40” or equivalent.
Do not use petroleum-based lubricants, or any oth-
er substance which may soften or otherwise dam-
age the rubber.
Install the intermediate guards (29, Figure 2), and
secure the intermediate to the engine bellhousing
with the previously removed hardware (6 and 7).
Seal Reassembly and Installation
(Figures 2 and 4)
Clean the seal cavity and shaft with a cloth soaked
in fresh cleaning solvent.
Most cleaning solvents are toxic and
flammable. Use them only in a well ven-
tilated area free from excessive heat,
sparks, and flame. Read and follow all
precautions printed on solvent contain-
ers.
The seal is not normally reused because wear pat-
terns on the finished faces cannot be realigned
during reassembly. This could result in premature
failure. If necessary to reuse an old seal in an emer-
gency,
carefully wash all metallic parts in fresh
cleaning solvent and allow to dry thoroughly.
Handle the seal parts with extreme care to prevent
damage. Be careful not to contaminate precision
finished faces; even fingerprints on the faces can
shorten seal life. If necessary, clean the faces with a
non-oil based solvent and a clean, lint-free tissue.
Wipe
lightly in a concentric pattern to avoid
scratching the faces.
Inspect the seal components for wear, scoring,
grooves, and other damage that might cause leak-
age. Clean and polish the seal spacer sleeve, or re-
place it if there are nicks or cuts on either end. If any
components are worn, replace the complete seal;
never mix old and new seal parts.
If a replacement seal is being used, remove it from
the container and inspect the precision finished
faces to ensure that they are free of any foreign
matter.
To ease installation of the seal, lubricate the pack-
ing rings and seal liner with water or a very
small
amount of oil, and apply a drop of light lubricating
oil on the finished faces. Assemble the seal as fol-
lows, (see Figure 4).