Gorman-Rupp Pumps PA12A60-B-6068H-ESP 1501367 and up User Manual
Page 50
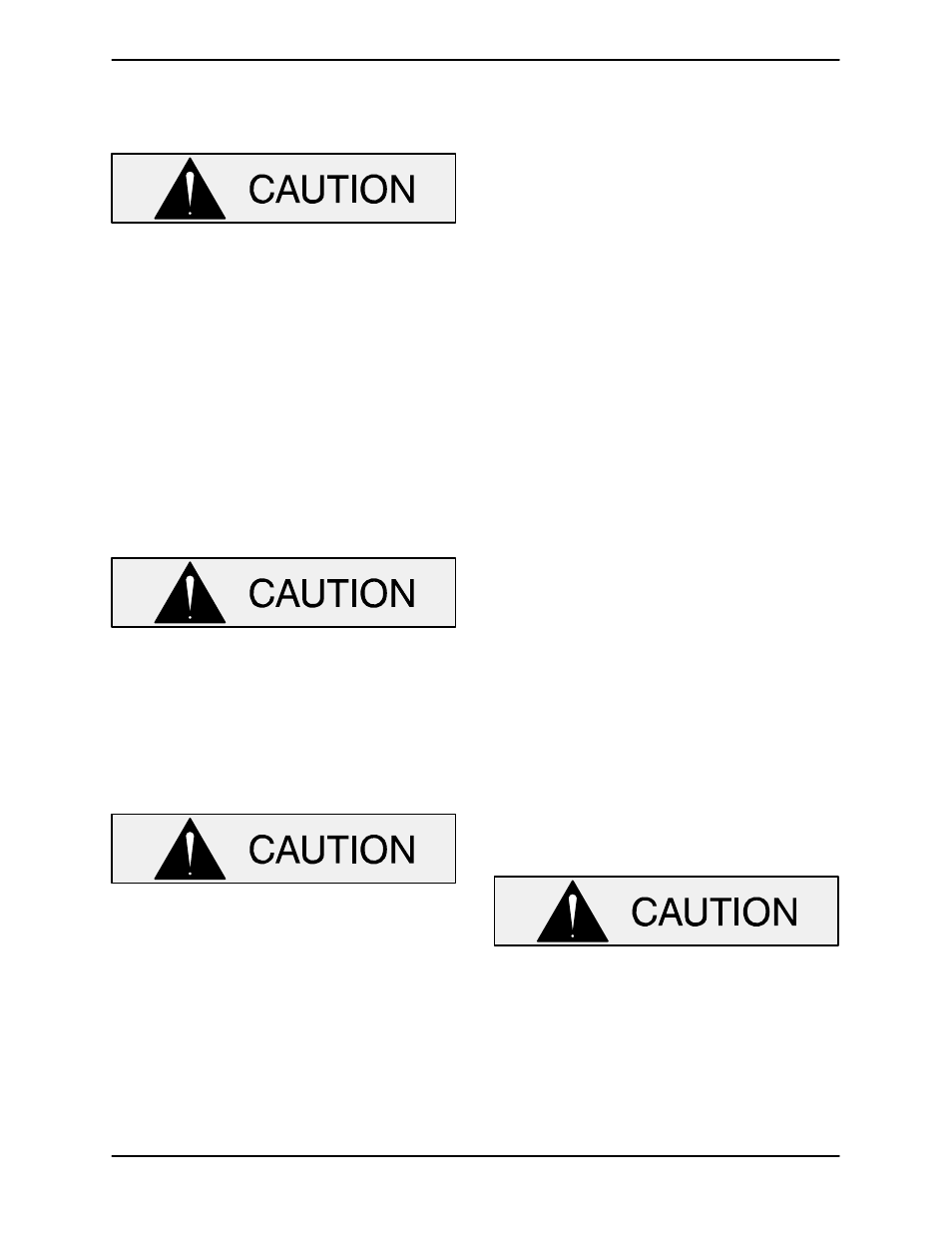
PA SERIES
OM-06261
MAINTENANCE & REPAIR
PAGE E - 30
Impeller Installation
(Figure 6)
Proper wear ring replacement requires
machining and dynamic balancing the im
peller assembly after the wear ring is
welded to the impeller. Failure to properly
install the wear ring and machine and bal
ance the impeller assembly can result in
premature shaft, seal or bearing failure, or
other damage to the pump.
Inspect the impeller, and replace it if cracked or
badly worn. If the impeller wear ring was removed,
chill the impeller by refrigeration and use an induc
tion heater or oven to heat the new wear ring. Slide
the wear ring onto the impeller until fully seated
against the shoulder and allow it to cool.
The wear ring must seat squarely on the
impeller; otherwise binding and/or exces
sive wear will occur. Use caution when han
dling hot parts to prevent burns.
Spot weld the wear ring to the impeller at three
places, equally spaced at the vanes. After welding,
machine the wear ring as shown in Figure 11.
The impeller assembly must be machined
and balanced as shown in Figure 11.
Otherwise, premature shaft, seal or bear
ing failure, or other damage to the pump
may occur.
After machining, dynamically balance the impeller
assembly per plane 1.05 oz./in. (11.7 g/cm).
Install the same thickness of impeller adjusting
shims (42) as previously removed. Install the shaft
key (33, Figure 7) and press the impeller assembly
onto the shaft until fully seated.
A clearance of approximately .025 to .040 inch
(0,63 to 1,04 mm) between the impeller and the
seal plate is recommended for maximum pump ef
ficiency. Measure this clearance, and add or re
move impeller adjusting shims as required.
After the impeller clearance has been set, align the
pin (9) in the impeller washer (8) with the hole in the
impeller and install the washer. Apply “Never‐
Seez” or equivalent compound on the threads of
the impeller capscrew (7). Immobilize the shaft and
secure the the impeller by torquing the capscrew
to 225 ft. lbs. (2700 in. lbs. or 31 m. kg.).
Pump Casing Installation
(Figure 6)
Install the casing gasket (6) over the pump casing
studs (4 and 5). Remove the hardware temporarily
securing the seal plate to the pedestal. Use a suit
able hoist and sling to position the volute over the
impeller and slide the studs through the seal plate
and pedestal mounting holes.
(Figure 7)
Install the bottle oiler bracket (12) over the volute
studs. Secure the bracket and volute casing with
the hardware (13, 14,and 15). Reconnect the hose
(48) to the connector (11) in the seal plate and se
cure it with the hose clamp (10).
Suction Head And Wear Ring Installation
(Figure 6)
If the wear ring (51) was removed, chill the wear
ring by refrigeration and heat the suction head.
Slide the wear ring into the suction head until fully
seated and allow it to cool.
The wear ring must seat squarely in the
suction head; otherwise binding and/or ex
cessive wear will occur. Use caution when
handling hot parts to prevent burns.
The wear ring is secured to the suction head with
the spiral pins (50). Drill three evenly spaced
3/16‐inch diameter x 3/4‐inch deep holes through
the wear ring and into the suction head. Tap the
spiral pins into the holes until fully seated.