Spencer Jet-Clean Separator User Manual
Page 2
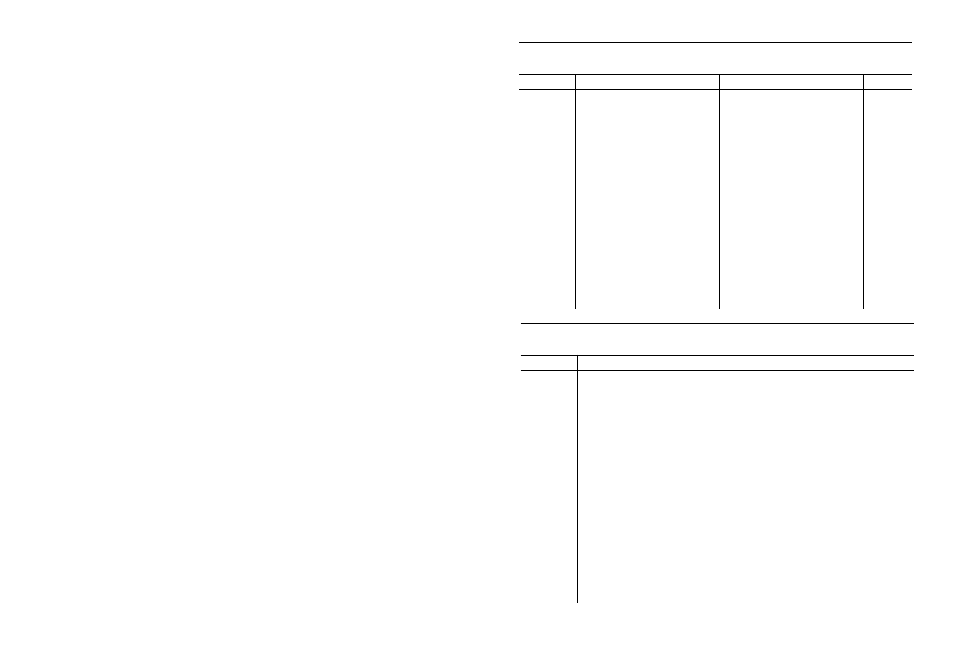
Contents
Pages
I
General Information
2
II
Separator Operation
2
III
Installation
3
IV
Operation and Maintenance
5
V
Trouble Shooting Guide — Separators
6
Warranty:
Spencer warrants that this product will be free from defects in
material and workmanship for a period of 18 months from date
of shipment or 12 months from date of start-up, whichever
comes first. Within the warranty period, we shall repair or
replace, F.O.B. our Factory or designated service center, such
products that are determined by us to be defective.
Caution: The Spencer Turbine Company is not responsible
for wear or corrosion caused by the material being handled
or failure due to corrosion or abrasion.
This warranty will not apply to any product which has been
subjected to misuse, negligence, or accident or misapplied
or improperly installed, or for failure due to corrosion or
abrasion. The warranty will not apply to any product which
has been disassembled, repaired or otherwise altered by
any persons not authorized by our Service Department.
The guarantee of the control manufacturer will govern the
extent of our guarantee on such equipment. Warranty work on
the controls must be authorized by Spencer and must be per-
formed in an authorized shop as designated by the control
manufacturer.
See Form 706 for complete Terms and Conditions.
I. General Information
The Jet-Clean™ Separator is supplied with an electronic
sequencer in various NEMA enclosures, (NEMA 12 is standard).
This unit utilizes “shop air” to clean the filter bags.
This design is reliable under severe climate conditions and
capable of continuous operation. The unit is easy to install.
Only one connection to high pressure air is necessary to ready
the unit for operation.
Removable Dirt Can Design
Available on all Jet-Clean Separators. Depending on the size of
the separator, dirt cans will be supplied in 3 cu. ft. or 7
1
/
2
cu. ft.
capacities. Each dirt can is provided with ball bearing casters
and two lifting handles to facilitate removal from the separator
and dumping. The dirt can is held in place by a can arrange-
ment and is removed by lifting the handle. When the can is
replaced and the handle lowered the can is locked in place.
Hopper Bottom Design
The Hopper Bottom design uses a 60° cone section that termi-
nates in a flange. Generally, more storage capacity can be
realized than in the removable dirt can design. For continuous
dumping of material, the hopper bottom style can be utilized
along with one of several types of automatic dumping devices.
Plastic Dirt Can Liner and Equalizing Line
Separators with removable dirt cans can be equipped with an
equalizing line which allows use of a plastic dirt can liner. This
option is recommended when hazardous or extremely dusty
materials are being handled. The equalizing line uses system
vacuum to hold the plastic bag (liner) in place in the dirt can
while the system is in operation. When the system is shut down
and the dirt can is removed from the separator, the collected
material can be easily and cleanly disposed of by tying off the
top of the plastic bag and removing it from the dirt can. A new
bag is then placed in the dirt can and the can replaced and its
equalizing line reconnected to prepare the system for contin-
ued operation.
Bag Cleaning Control
The Jet-Clean Separator has an ASME code welded air tank
with pressure gage and pressure-relief valve. The bag cleaning
control is time-based and is designed to cycle each of the air
operated diaphragm valves at a preprogrammed rate. This
program is determined by the field conditions including type of
material collected and customer requirements regarding the
system.
Material Level Indicator (Optional)
The material level indicator senses high material level and can
be wired to: shut down the system, empty the separator,
sound an alarm, activate a light or start a rotary valve.
II. Separator Operation
The Spencer Jet-Clean Separator is designed to separate air-
borne material from the air stream of cleaning or conveying
system and to collect it for use or disposal. Large particles of
material are separated from the air stream by the cyclonic
action induced by the separator casing design. Fine particles
which still remain in the reduced velocity air are collected on
the outside surface of the bags. Eventually, this material begins
to build up on the bags to form what is known as “bag cake.”
As bag cake continues to build up on the bags, the resistance
to air flow through the bags increases. this is indicated by an
increase in differential pressure across the bags and is mea-
sured by the manometer supplied with each separator.
For any given material, there is an optimum amount of bag cake
which should be allowed to form since it actually enhances the
filtering efficiency of the bags. Less than the optimum amount
will result in less than ideal (although in most cases adequate)
filtration. Too much cake will cut down on the air flow and may
actually adversely affect conveying velocity in the system. In
general, an average pressure drop of 4” H
2
O across the filter
bags will provide good results although exceptions to this will be
found. A certain amount of trial-and-error work with any new
system will usually be necessary to determine the best pressure
drop across the bags for that system.
To prevent too much cake from accumulating, the Spencer Jet-
Clean Separator’s control initiates a backwash of clean, high
pressure air through the bags.
Special nozzles direct the high pressure air into the bags so as
to induce additional backflow of the air from the clean air
plenum through the bags. The blast of high pressure air in
combination with induced backflow causes the filter bags to
puff out, thus loosening the collected cake. Reverse airflow
through the bags helps blow this loosened dust away from the
bags so it can drop to the bottom of the separator where it is
collected.
2
7
Filter Bag Part No.
Filter Bag Maintenance Record
Date
Filter Bag Material
Date Changed
Vacuum Accessories Record
(Hoses, Tools, Valves)
Part No.
Description