Xylem H-264 User Manual
Page 13
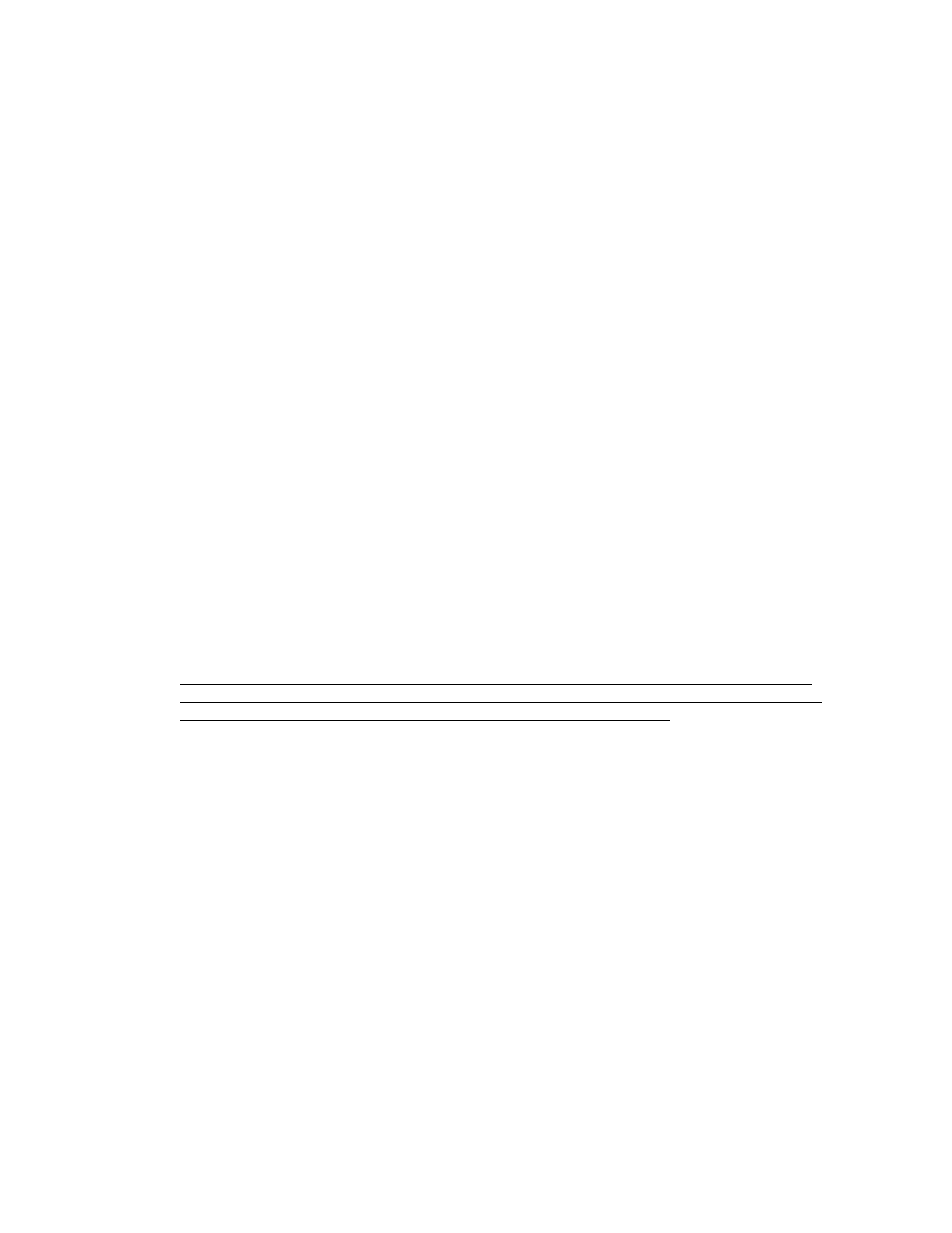
ASI v2 Operations (PRELIMINARY)
Toggle PTT LED at Short Software Delay rate (SWDelayS)
This diagnostic checks that the intrinsic RC DCO frequency of the MSP430 is within nominal
tolerance. The DCO clock is as the microprocessor’s main clock during serial input parsing and
conversion, used to time the 100 millisecond “serial input pause” and the 30 second delay in the
error handling routine prior to calling a software reset. None of these processes or timing
requires a particularly precise time base, so the DCO clock is used. During the diagnostic, the
processor toggles the PTT LED approximately every 20 milliseconds, for a frequency of 25 Hz
at the “PTT” test point (P23). At room temperature the tolerance is +/- 20%. During the test,
the transmitter “Switched Battery Power” is not turned on, and since the PTT transmitter
interface is an open collector, normally this test may be performed with a transmitter connected.
Toggle PTT LED at Long Software Delay rate (SWDelayL)
This diagnostic is a duplicate of the “Short Software Delay rate” routine except a longer software
delay timer is used, having a toggle rate of approximately 30 seconds. Again the tolerance is
+/- 20% at room temperature. This delay routine is used operationally only to generate the wait
time before calling a software reset in the error handler. During the test, the transmitter
“Switched Battery Power” is not turned on, and since the PTT transmitter interface is an open
collector, normally this test may be performed with a transmitter connected. (The next
diagnostic routine, the
“Load test control
”, also uses this software delay timer.)
Load test control: toggle SW+12 at 30 sec rate
This diagnostic is designed to be used in conjunction with an external load resistor (a 5.0 ohm,
at least 25 W, power resistor) to measure the voltage drop and calculate the internal resistance
of the transmitter “Switched Battery Power” power MOSFET during a high load. The processor
turns the “Switched Battery Power” on for approximately 30 seconds, then off for 30 seconds.
Using a battery (or high current power supply) set for approximately 12 V, measure the voltage
drop between the battery input (pin 2, P10) and the transmitter “Switched Battery Power” (pin 5,
P15) during the “Switch Battery Power” ON period. Also measure the battery input voltage
during the ON period. Using the measured value of the load resistor, calculate the load current
(nominally 2.4 A). Then using the measured voltage drop, calculate the MOSFET resistance
during load (Rdson). It should be less than 0.035 ohms. After confirming the MOSFET
resistance is within specification, carefully touch Q2 and confirm it is not warm to the touch.
CAUTION – the 5 ohm resistor load is approximately 30 W, so depending on the type power
resistor used, it could become very hot, even with the 50% duty cycle. DO NOT LEAVE THIS
TEST ON UNATTENDED or ON FOR MORE THAN A FEW MINUTES.
DIP Switch Test, send DIP switch out RS232 @ 1200 baud
This diagnostic is used to check that all the DIP switch positions are functional, both in the
“open” and “closed” positions. (Obviously, in order to run this test, the DIP switch must be at
least partially functional.) It also checks the processor UART0 transmission section, the baud
rate generator and the RS232 driver IC. During this diagnostic the processor powers on the
DIP switch inputs, reads the 8 bit values, forms a 4 digit ASCII hex value (with the first 2 digits
always “00”). This value is output asynchronously using the processor UART0 at 1200 baud (8
bits, no parity, 1 stop bit), followed by a CR and LF, using the RS232 auxiliary output (pin 2, J1,
“AuxRS232”). The processor then waits ½ a second and repeats the process. To confirm all
DIP switch functions, start this diagnostic, attach a PC serial port “ground” and “receive data” to
the “AuxRS232” connector pin 4 and pin 2, respectively, start a terminal emulation program
using 1200 baud and monitor the received hex value. Start changing the DIP switches: begin
with all “open” the output should be “0000”; set switch 1 to “closed”, the output should be
“0001”; set switch 2 to “closed”, the output should be “0003”; continue sequentially setting
increasing dip switches to the “closed” position and monitoring the output progression: “0007”,
“000F”, “001F”, …”00FF”.
BatVoltage Avg out RS232 @ 1200baud & PTT on < VBatCutoff
This diagnostic is identical to the “
Turn on PTT LED when BatVoltage Avg < VBat Cutoff”
diagnostic except that the processor also outputs the measured battery voltage average, in
counts, at 1200 baud (8 bits, no parity, 1 stop bit) on the auxiliary RS232 ASI output (pin2, J1,
“AuxRS232”), every time a new average is calculated. The output is a 5 digit decimal number
representing the ADC count (0-4095). The conversion to battery voltage is N * 0.0044895 = V,