Xylem H-264 User Manual
Page 12
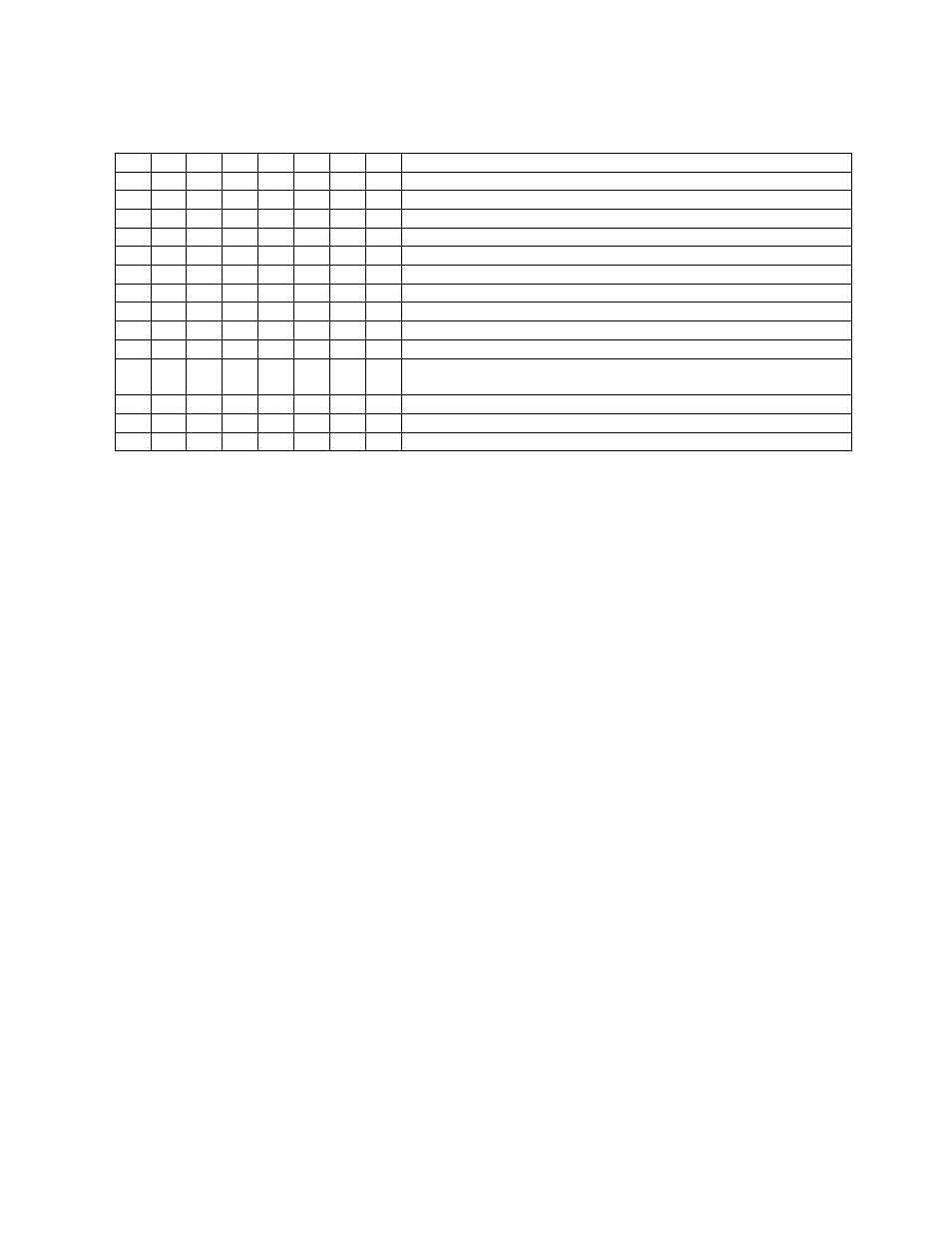
ASI v2 Operations (PRELIMINARY)
The diagnostic test routines are explained in detailed below.
S1 S2 S3 S4 S5 S6 S7 S8
1
1
1
1
0
0
0
0
Field Test Tool
1
1
1
1
1
0
0
0
Generate 1000 Hz on Tone Out (SW+12 on, PTT off)
1
1
1
1
0
1
0
0
Generate 1920 Hz on Tone Out (SW+12 on, PTT off)
1
1
1
1
1
1
0
0
Generate 2140 Hz on Tone Out (SW+12 on, PTT off)
1
1
1
1
0
0
1
0
Generate 4062.5 Hz on Tone Out (SW+12 on, PTT off)
1
1
1
1
1
0
1
0
Turn on PTT LED when BatVoltage Avg < VBatCutoff
1
1
1
1
0
1
1
0
Toggle PTT LED at Short SW Delay (about 20 msec) rate
1
1
1
1
1
1
1
0
Toggle PTT LED at Long SW Delay (about 30 sec) rate
1
1
1
1
0
0
0
1
Load test control: toggle SW+12 at 30 sec rate
1
1
1
1
1
0
0
1
DIP Switch Test, send DIP switch out RS232 @ 1200 baud
1
1
1
1
0
1
0
1
BatVoltage Avg out RS232 @ 1200baud & PTT on <
VBatCutoff
1
1
1
1
0
1
1
1
Put High Speed Xtal MCLK on P16 & Xtal2 on ACLK
1
1
1
1
1
1
1
1
Put DCO MCLK on P16
1
1
1
1
x
x
x
x
Any other: put DCO MCLK on P16
Field Test Tool
In this mode, the ASI can be used to assist in field transmission path analysis. The ASI requires
no input. It transmits an ALERT binary message about every 20 seconds, (20.00 seconds from
the end of one transmission to the start of the next transmission). The ASI uses an ID of 5000
and the transmitted data value increments on every transmission, initially starting at value 0 on
RESET.
Production Test Routines
Generate Tone Out (4 separate diagnostic routines)
This diagnostic checks the FSK generation code, high frequency oscillator and the 3
rd
order
lowpass filter transfer response. The processor powers on the filter, enables the tone output
and generates a continuous frequency. To accurately measure the frequency use the square
wave output test point “DTone” test point (P14); all frequency measurements should be within
+/- 0.5 Hz, when measured at room temperature. To measure the filter transfer response,
examine the signal at the analog filter output “ToneOut” test point (P14). With the 1920 & 2140
Hz the analog signal should approximate a sine wave at 200mV RMS centered at ½ the supply
voltage (3.3V/2 or approximately 1.65 V); at 4062.5 Hz the signal should be less than 80 mV
RMS. At 1000 Hz, the signal shape will not be a sine wave and but more like a contorted
square wave, yet still should measure approximately 200mV RMS. The tolerance on these
RMS levels is +/- 10%. During these tests the transmitter “Switched Battery Power” is turned on
(required to power the filter circuit) which unintentionally powers any transmitter connected, but
the transmitter “PTT” is not asserted during the test.
Turn on PTT LED when BatVoltage Avg < VBat Cutoff
This diagnostic checks the battery voltage monitor resistive divider network, the 12 bit Analog to
Digital Converter (ADC) and the ADC reference circuit. The battery monitor circuit is enabled
and the ADC continuously measures and calculates an 8 sample average of the input battery
voltage. If the average drops below the minimum transmitter battery voltage threshold (set for
9.00 volts), the PTT LED is turned on. As designed, with a 0.5%, 50 ppm/degC reference and
0.1% resistors in the battery voltage monitor network, the worst case error (over the full
operating temperature range, excluding ADC non-linearity) is +/- 0.85%. The PTT LED
illumination range is therefore 8.92 V to 9.08 V. During the test, the transmitter “Switched
Battery Power” is not turned on, and since the PTT transmitter interface is an open collector,
normally this test may be performed with a transmitter connected.