Xylem ADAQCPC Modbus Aquavar CPC User Manual
Page 6
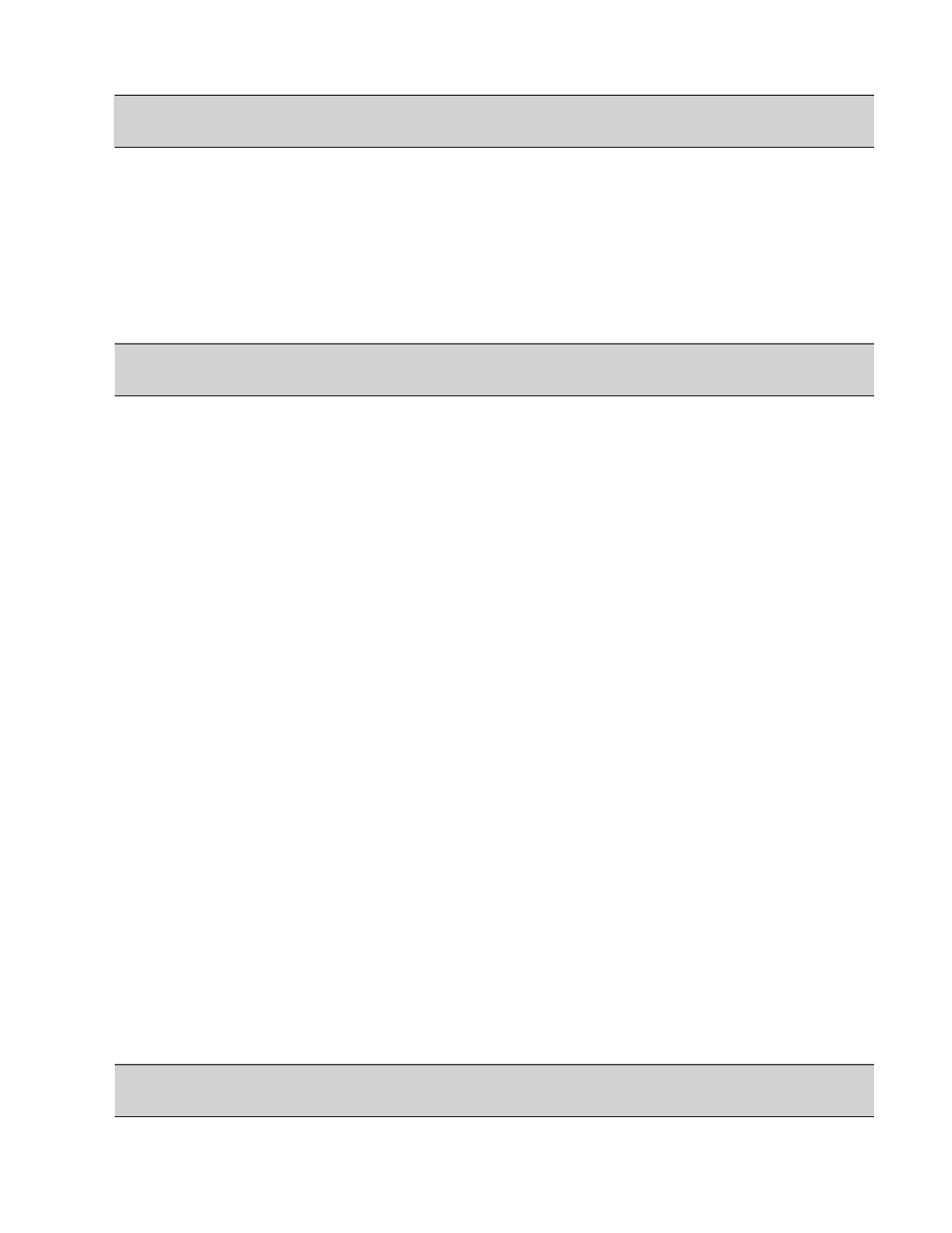
6
Note: With Modbus, any parameter can be accessed using the format: “4” followed by the parameter
number. See the following example:
Changing Ramps 1 and 2 via Modbus from 5 to 10 seconds on a drive over 15 HP.
1. Set parameter 1102 (Applic Macro) to: [1] Single Pump, [4] Constant Slv, or [5] Speed Cntrl.
2. Configure and Setup Modbus Serial Communications
3. Ramp 1 is parameter 1301 and Ramp 2 is parameter 1302.
4. Write ‘100’ to Holding Register 41301. Assuming no errors occur during this transaction, 1301 (Ramp 1)
should now be set to 10.0 seconds.
Note: There is an implied decimal point that is not written between the first (from the right) and second
digit. Thus 100 = 10.0
5. Write ‘100’ to Holding Register 41302. 1302 (Ramp 2) should now be set to 10.0 seconds.
START / STOP CONTROL
Start
1. Set parameter 1102 (Applic Macro) to: [1] Single Pump, [4] Constant Slv, or [5] Speed Cntrl.
2. Configure and Setup Modbus Serial Communications
3. Set parameter 1201 to [1] Fieldbus
4. To Start, write ‘1’ to Register 00002. Register 00001 (Stop) must be set ‘0’. The rotation arrow on the display
should now be spinning and the drive will start if the actual pressure is below the setpoint.
5. Write ‘0’ to Register 00002. The drive will continue to run as long as
Register 00001 is ‘0’.
Stop
1. To Stop, write ‘1’ to Register 00001. Register 00002, should be set to ‘0’. The rotation arrow on the display
should stop rotating.
REMOTE SETTING OF SET POINT 1
1. Set parameter 1102 (Applic Macro) to: [1] Single Pump, [4] Constant Slv, or [5] Speed Cntrl.
2. Configure and Setup Modbus Serial Communications.
3. Set parameter 1601 to [0] Setp1.
4. Set parameter 1602 to [2] Fieldbus.
5. Write a value between ‘10000’ and ‘0’ (100.00% to 0% of Transducer Max) to Holding Register 40003.
Note: There is an implied decimal point that is not written between the second (from the right) and third
digit. Thus, 10000 = 100.00%.
SETTING DRIVE PARAMETERS