Xylem IM194 R02 GRINDER PUMPS 1 AND 3 11?4 DISCHARGE User Manual
Page 6
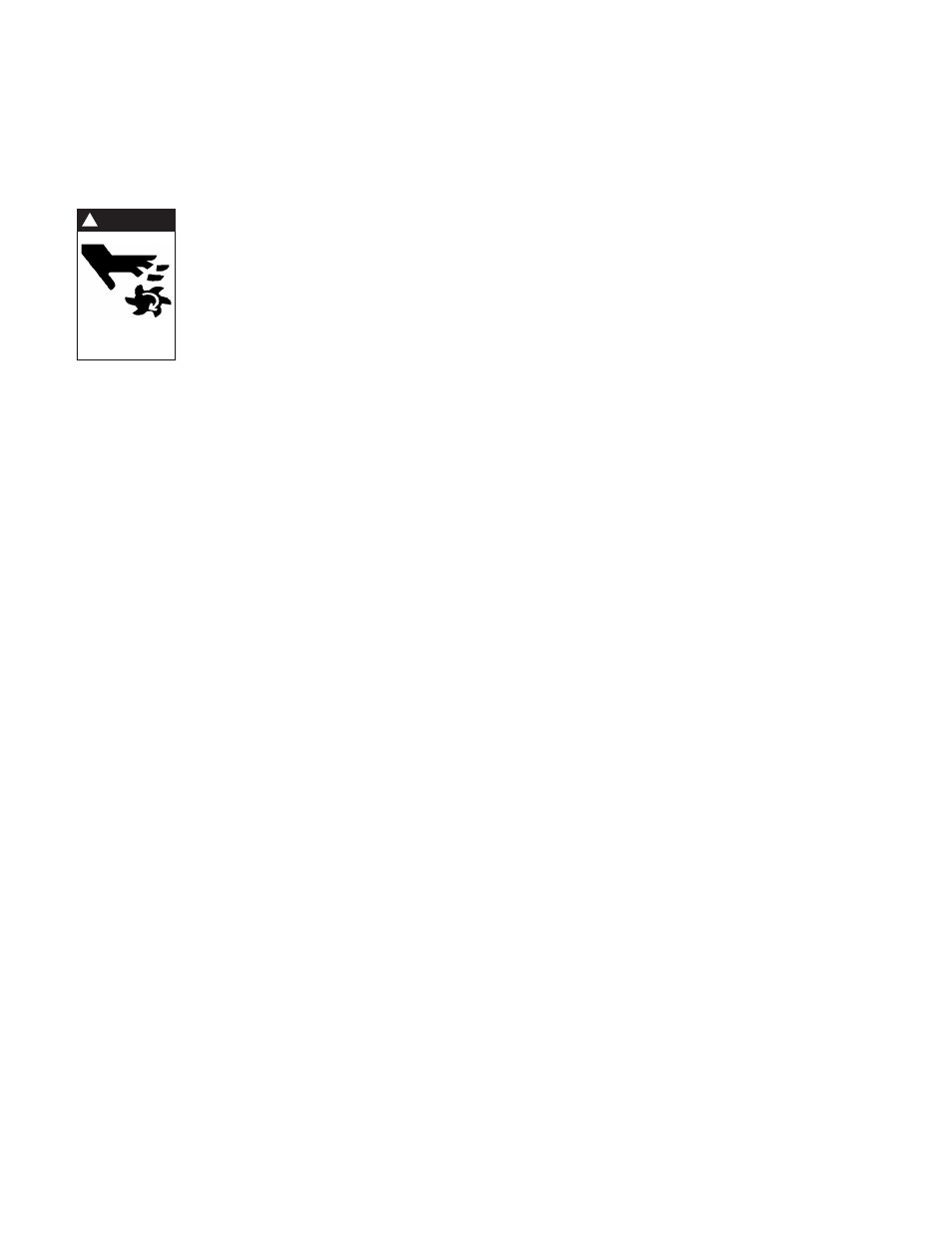
6
INSTALLATION
Connect the pump(s) to the guide rail pump adapters or to the
discharge piping. Guide rail bases should be anchored to the
wetwell floor.
Complete all wiring per the control panel wiring diagrams
and NEC, Canadian, state, provincial and/or local codes.
This a good time to check for proper rotation of the
motors/impellers.
DO NOT PLACE HANDS IN PUMP
SUCTION WHILE CHECKING
MOTOR ROTATION. TO DO SO WILL
CAUSE SEVERE PERSONAL INJURY.
Always verify correct rotation. Correct
rotation is indicated on the pump casing.
Three phase motors are reversible. It is
allowable to bump or jog the motor for a
few seconds to check impeller rotation. It
is easier to check rotation before installing
the pump. Switch any two power leads to
reverse rotation.
Lower the pump(s) into the wetwell.
Check to insure that the floats will operate freely and not
contact the piping.
OPERATION
Once the piping connections are made and checked you can
run the pumps.
Control Panel Operation – Fill the wetwell with clear water.
Use the pump H-O-A (Hand-Off-Automatic) switches
in Hand to test the pumps. If they operate well in Hand
proceed to test Automatic operation. If the pumps run but
fail to pump, they are probably air locked, drill the relief holes
per the instructions in the Piping Section.
Place Control Panel switch(es) in Automatic position and
thoroughly test the operation of the ON, OFF, and
Alarm floats by filling the wetwell with clear water.
Important: Failure to provide a Neutral from the power
supply to a 1Ø, 230 volt Control Panel will not allow the
panel control circuit to operate. The Neutral is necessary
to complete the 115 volt control circuit.
Check voltage and amperage and record the data on the front
of this manual for future reference. Compare the amperage
readings to the pump nameplate maximum amperage. If
higher than nameplate amperage investigate cause. Operating
the pump off the curve, i.e. with too little head or with high
or low voltage will increase amperage. The motor will operate
properly with voltage not more than 10% above or below
pump nameplate ratings. Performance within this range will
not necessarily be the same as the published performance at
the exact rated nameplate frequency and voltage. Correct the
problem before proceeding. Three phase unbalance is also a
possible cause. See Three Phase Power Unbalance and follow
the instructions.
Reset the Alarm circuit, place pump switch(es) in the Au-
tomatic position and Control Switch in ON position. The
system is now ready for automatic operation.
Explain the operation of the pumps, controls and alarms to
the end user. Leave the paperwork with the owner or at the
control panel if in a dry, secure location.
OPERATION
INSTALLATION
DANGER
Hazardous Machinery
!
1st, 2nd and 3rd Characters – Discharge Size and Type
1GD = 1¼" discharge, grinder, dual seal
4th Character – Mechanical Seals
5 = silicon carbide/silicon carbide/BUNA – lower seal and
carbon/ceramic/BUNA – upper seal (standard)
3 = silicon carbide/tungsten carbide/BUNA – lower seal
and carbon/ceramic/BUNA – upper seal (optional)
5th Character – Cycle/RPM
1 = 60 Hz/3500 RPM
5 = 50 Hz/2900 RPM
6th Character – Horsepower
G = 2 HP
7th Character – Phase/Voltage
1 = single phase, 230 V
2 = three phase, 200 V
3 = three phase, 230 V
4 = three phase, 460 V
5 = three phase, 575 V
6 = three phase, 380 V
8 = single phase, 208 V
NOMENCLATURE DESCRIPTION
8th Character – Impeller Diameter
A = 5
5
⁄
8
", Standard
C = 4¾"
B = 5¼"
D = 4¼"
9th Character – Cord Length (Power and Sensor)
A = 20' (standard)
G = 75'
D = 30'
J = 100'
F = 50'
10th Character – Options
S = Seal fail, moisture sensing circuit
1
E = Epoxy paint
Last Character – Option
H = Pilot duty thermal sensors
1
1
These options add a 2-wire or 4-wire sensor cord to the pump and
require optional control panel circuits to operate. See panel options
on control panel bulletin BCP5.