Xylem IM194 R02 GRINDER PUMPS 1 AND 3 11?4 DISCHARGE User Manual
Page 4
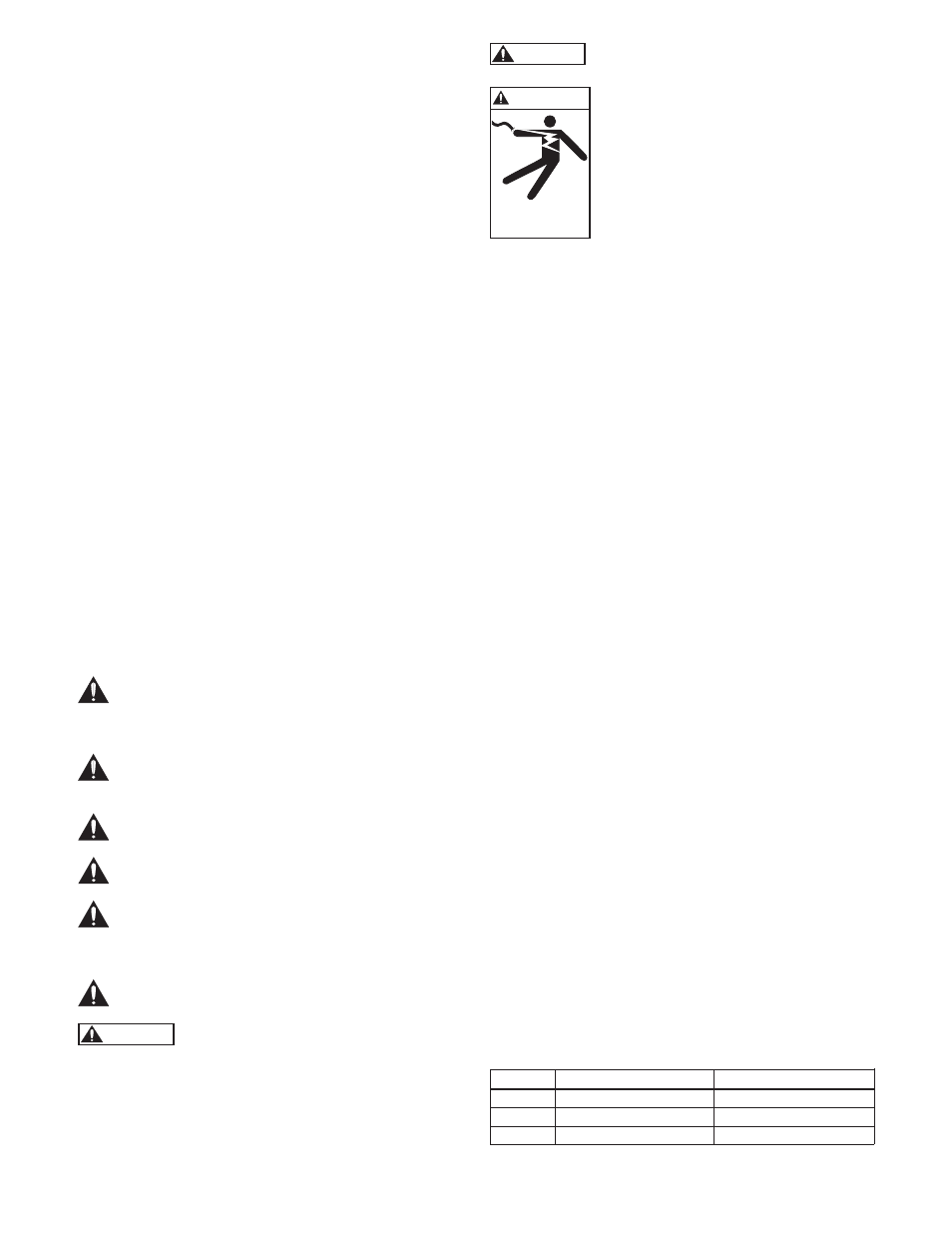
4
NOTICE: FOLLOW THE INSTRUCTIONS THAT ARE
PROVIDED WITH THE GUIDE RAIL
ASSEMBLY.
PIPING
Discharge piping should be no smaller than the pump dis-
charge diameter and kept as short as possible, avoiding unnec-
essary fittings to minimize friction losses.
Install a check valve to prevent fluid backflow. Backflow
can allow the pump to “turbine” backwards and may cause
premature seal and/or bearing wear. If the pump is turning
backwards when it is called on to start the increased torque
may cause damage to the pump motor and/or motor shaft and
some single-phase pumps may actually run backwards.
Install an adequately sized gate valve after the check valve for
pump, plumbing and check valve maintenance.
Important – Before pump installation. Drill a
3
⁄
16
" (4.8mm)
relief hole in the discharge pipe. It should be located within
the wetwell, 2" (51mm) above the pump discharge but below
the check valve. The relief hole allows any air to escape from
the casing. Allowing liquid into the casing will insure that the
pump can start when the liquid level rises. Unless a relief hole
is provided, a bottom intake pump could “air lock” and will
not pump water even though the impeller turns.
All piping must be adequately supported, so as not to impart
any piping strain or loads on the pump.
The pit access cover must be of sufficient size to allow for
inspection, maintenance and crane or hoist service.
WIRING AND GROUNDING
Important notice: Read Safety Instructions before proceeding
with any wiring.
Use only stranded copper wire to pump/motor and
ground. The ground wire must be at least as large as the
power supply wires. Wires should be color coded for
ease of maintenance and troubleshooting.
Install wire and ground according to the National Elec-
trical Code (NEC), or the Canadian Electrical Code, as
well as all local, state and provincial codes.
Install an all leg disconnect switch where required by
code.
Disconnect and lockout electrical power before per-
forming any service or installation.
The electrical supply voltage and phase must match all
equipment requirements. Incorrect voltage or phase can
cause fire, motor and control damage, and voids the
warranty.
All splices must be waterproof. If using splice kits follow
manufacturer’s instructions.
Select the correct type and NEMA grade
junction box for the application and location.
The junction box must insure dry, safe wiring
connections.
Seal all controls from gases present which
may damage electrical components.
FAILURE TO PERMANENTLY
GROUND THE PUMP, MOTOR AND
CONTROLS BEFORE CONNECTING
TO POWER CAN CAUSE SHOCK,
BURNS OR DEATH.
ON NON-PLUG UNITS, DO NOT RE-
MOVE CORD AND STRAIN RELIEF. DO
NOT CONNECT CONDUIT TO PUMP.
SELECTING AND WIRING
PUMP CONTROL PANELS
Control panel wiring diagrams are shipped with the
control panels. Please use the control panel drawings in
conjunction with this instruction manual to complete the
wiring.
Important – Read Before Proceeding
Single-Phase Motor Design Change Information –
Only for New Pump Installed on Older Panel.
Overload and Capacitors: Single-phase pumps built after
Dec.1, 2005 (M05 date code) now feature a built-in, on
winding overload. If replacing a pre-Dec 2005 pump (date
code L05 or earlier) you have to change the capacitors in the
old style control panel.
Pilot Duty Thermal Sensor/Overload Wire: Pre-Dec 2005
single-phase pumps had a pilot-duty thermal sensor wire
connected between the pump and an overload heater block in
the control panel, you will have to install a jumper wire across
the two high temperature/overload terminals when installing
a new pump on an old panel or the new pump may not oper-
ate.
Standard single-phase pumps no longer have a Pilot Duty
Thermal Sensor Wire but it is available as an option. Another
option is a Seal Fail Sensor & Wire. Please use the Nomencla-
ture data found in this manual and the pump Order Number
to determine which optional features are on the pump being
installed.
CONTROL PANEL REQUIREMENTS
Single Phase Control Panels – Eff. Dec. 2005, M05 date code,
Series 1GD and 12GDS single phase grinder pumps require a
control panel containing as a minimum:
• Magnetic contactor
• Start capacitor
• Run capacitor
• Start relay
• Terminal wiring strip for all external connections.
See Recommended Panel Chart in Engineering Data Section
Capacitor and Starting Relay Information
Description Order a CP1GDB for New Pump
Part Order No. – Old Pump
Start Cap
216-259 Mfd @ 330 vac
RB-61 (594 Mfd @ 125 vac)
Run Cap
50 Mfd @ 370 vac
RB-62 (30 Mfd @ 370 vac)
Start Relay
9K458 (RVA2ALKL)
9K458 or RB-60 (155031 102)
PIPING
WIRING AND GROUNDING
WARNING
WARNING
WARNING
Hazardous voltage
can shock, burn or
cause death.
SELECTING AND WIRING
PUMP CONTROL PANELS