Rainbow Electronics MAX17083 User Manual
Page 12
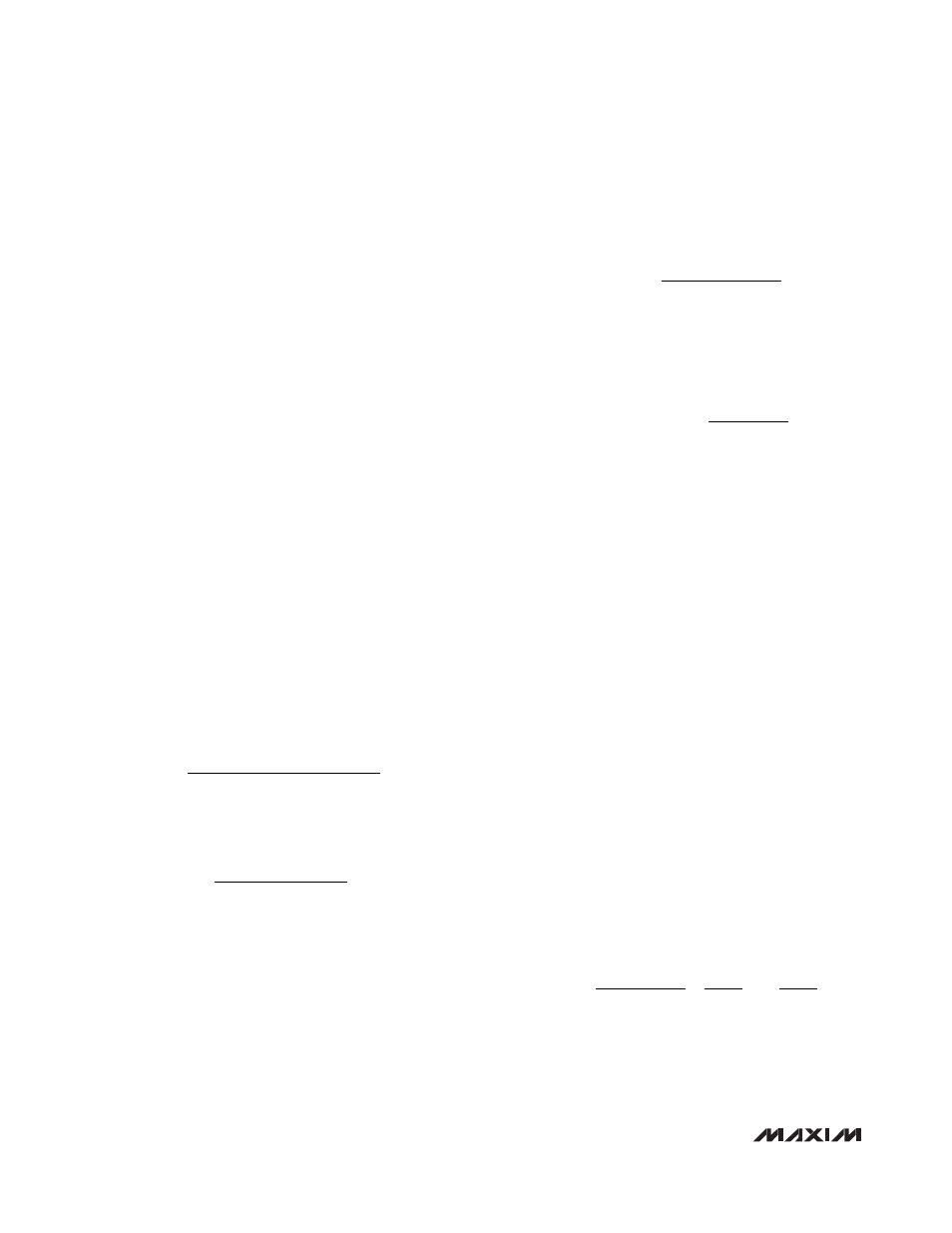
(I
LOAD
) determines the thermal stresses and thus dri-
ves the selection of input capacitors, MOSFETs, and
other critical heat-contributing components.
•
Switching Frequency. This choice determines the
basic trade-off between size and efficiency. The
optimal frequency is largely a function of maximum
input voltage due to MOSFET switching losses that
are proportional to frequency and the square of V
IN
.
The optimum frequency is also a moving target, due
to rapid improvements in MOSFET technology that
are making higher frequencies more practical.
•
Inductor Operating Point. This choice provides
trade-offs between size and efficiency, and
between transient response and output ripple. Low
inductor values provide better transient response
and smaller physical size, but also result in lower
efficiency and higher output ripple due to increased
ripple currents. The minimum practical inductor
value is one that causes the circuit to operate at the
edge of critical conduction (where the inductor cur-
rent just touches zero with every cycle at maximum
load). Inductor values lower than this grant no fur-
ther size-reduction benefit. The optimum operating
point is usually found between 20% and 50% of rip-
ple current. When pulse skipping (at light loads),
the inductor value also determines the load-current
value at which PFM/PWM switchover occurs.
Step-Down Inductor Selection
The switching frequency and inductor operating point
determine the inductor value as follows:
Assuming 5A maximum load current, and an LIR of 0.3
yields:
Find a low-loss inductor having the lowest possible DC
resistance that fits in the allotted dimensions. Most
inductor manufacturers provide inductors in standard
values, such as 1.0µH, 1.5µH, 2.2µH, 3.3µH, etc. Also
look for nonstandard values, which can provide a better
compromise in LIR across the input voltage range. If
using a swinging inductor (where the no-load induc-
tance decreases linearly with increasing current), evalu-
ate the LIR with properly scaled inductance values. For
the selected inductance value, the actual peak-to-peak
inductor ripple current (
ΔI
INDUCTOR
) is defined by:
Ferrite cores are often the best choice, although soft sat-
urating molded core inductors are inexpensive and can
work well at 500kHz. The core must be large enough not
to saturate at the peak inductor current (I
PEAK
):
SMPS Output-Capacitor Selection
The output filter capacitor selection requires careful
evaluation of several different design requirements—
stability, transient response, and output ripple volt-
age—that place limits on the output capacitance and
ESR. Based on these requirements, the typical applica-
tion requires a low-ESR polymer capacitor (lower cost
but higher output-ripple voltage) or bulk ceramic
capacitors (higher cost but low output-ripple voltage).
SMPS Loop Compensation
Voltage positioning dynamically lowers the output volt-
age in response to the load current, reducing the loop
gain. This reduces the output capacitance requirement
(stability and transient) and output power dissipation
requirements as well. The load-line is generated by
sensing the inductor current through the high-side
MOSFET on-resistance, and is internally preset to
-5mV/A (typ). The load-line ensures that the output volt-
age remains within the regulation window over the full-
load conditions.
The load line of the internal SMPS regulators also pro-
vides the AC ripple voltage required for stability. To
maintain stability, the output capacitive ripple must be
kept smaller than the internal AC ripple voltage, and
crossover must occur before the Nyquist pole occurs
(1 + duty)/(2f
SW
). Based on these loop requirements, a
minimum output capacitance can be determined from
the following:
where R
DROOP
is 5mV/A as defined in the
Electrical
Characteristics
table and f
SW
is the switching frequen-
cy selected by the FREQ setting (see Table 1).
C
f
R
V
V
V
V
OUT
SW DROOP
REF
OUT
OUT
>
⎛
⎝⎜
⎞
⎠⎟
⎛
⎝⎜
⎞
⎠⎟
+
1
2
1
IIN
⎛
⎝⎜
⎞
⎠⎟
I
I
I
PEAK
LOAD MAX
INDUCTOR
=
+ ⎛
⎝⎜
⎞
⎠⎟
(
)
Δ
2
ΔI
V
V
V
V f
L
INDUCTOR
OUT
IN
OUT
IN OSC
=
(
)
-
L
V
V
V
V
f
OUT
IN
OUT
IN
OSC
=
Ч
(
)
Ч
Ч
-
1 5
.
L
V
V
V
V
f
I
LIR
OUT
IN
OUT
IN
OSC
LOAD MAX
=
Ч
(
)
Ч
Ч
Ч
-
(
)
MAX17083
Low-Voltage, Internal Switch,
Step-Down Regulator
12
______________________________________________________________________________________