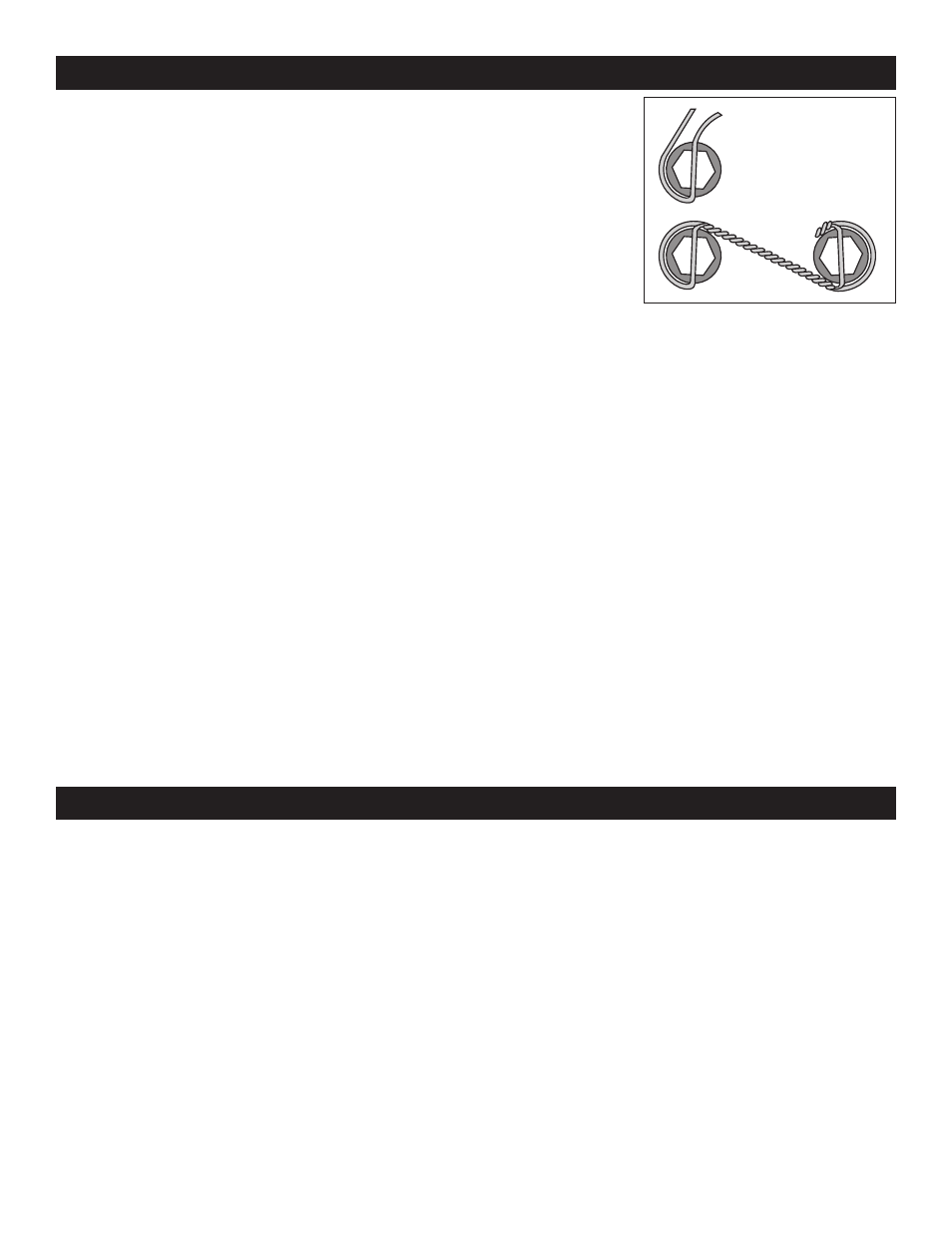
•Install the hub assembly (customer supplied) onto the rotor adapter (2) by sliding bolts (7 for
six pin hub) or (8 for wide 5 hub) from the larger I.D. side of the rotor (3) thru holes in rotor
adapter and thread into hub. For wide 5 hubs, install spacer (9) between rotor adapter and
hub before threading bolt into wide 5 hub. Slide hub/rotor assembly onto spindle and secure
with customer supplied spindle nut.
•The caliper (10) should be installed first with clean, dry threads on the mounting bolts. Install
the caliper on the inboard side of the bracket (1 or 1a) by sliding bolt (11) thru washer (12)
thru caliper mounting tabs and into the caliper mounting bracket. Initially place one shim
each (13 and 14) between the caliper and caliper bracket. The caliper bleed screws should
be horizontal to the bracket for top fitting applications, or pointing up for the front mount
configuration. Snug the bolts (11) and check that the rotor (3) is centered in the caliper. Add
or subtract .035" shims (13) and/or .016” shims (14) as necessary between the caliper
mounting bracket and the caliper to center the caliper on the rotor.
•Remove the pad pin retainer (15) from the caliper (10). Slide the brake pads (16) into place.
They should install easily without interference. Reinstall the pad pin retainer.
•Once all clearances have been checked, secure the caliper (10) to the caliper mounting bracket (1 or 1a) with bolt (11) using red
Loctite
®
271 on the bolt threads. Torque bolt to 40 ft-lb.
•NOTE: Rubber brake hoses generally cannot be adapted to Wilwood calipers. The caliper inlet fitting is a 1/8-27 NPT. The preferred
method is to use steel adapter fittings at the caliper, either straight, 45 or 90 degree and enough steel braided line to allow for full
suspension travel and turning radius, lock to lock. Carefully route lines to prevent contact with moving suspension, brake or wheel
components. It is the installer's responsibility to properly route and ensure adequate clearance and retention for brake hose
components.
•It is also the installer's responsibility to ensure that all fittings and hoses are the correct size and length, to ensure proper sealing and
that they will not be subject to crimping, strain and abrasion from vibration or interference with suspension components, brake rotor, or
wheel.
•In absence of specific instructions for brake line routing, the installer must use his best professional judgment on correct routing and
retention of lines to ensure safe operation. Test vehicle brake system per the 'minimum test' procedure stated within this document
before driving. After road testing, inspect for leaks and interference. Initially after install and testing, perform frequent checks of the
vehicle brake system and lines before driving, to confirm that there is no undue wear or interference not apparent from the initial test.
Afterwards, perform periodic inspections for function, leaks and wear in a interval relative to the usage of vehicle.
•Bleed the brake system. Reference the general information and recommendations below for proper bleeding instructions.
Page 4
BEGIN BY SLIDING THE 0.032"
DIAMETER WIRE THROUGH TWO OF
THE HOLES (LEFT) THAT ARE 180°
APART. TWIST THE WIRE AS
SHOWN (BELOW) USING SAFETY
WIRE PLIERS. NOW SLIDE ONE
WIRE THROUGH TWO OF THE
HOLES (180° APART) AND WRAP THE
OTHER WIRE AROUND THE BOLT.
TWIST THE WIRES TOGETHER TO
FORM A PIGTAIL. SEE DS-386 FOR
COMPLETE DETAILS.
Figure 2. Safety Wire Diagram
Additional Information and Recommendations
•For optimum performance, fill and bleed the new system with Wilwood Hi-Temp° 570 grade fluid or EXP 600 Plus. For severe braking
or sustained high heat operation, use Wilwood EXP 600 Plus Racing Brake Fluid. Used fluid must be completely flushed from the
system to prevent contamination. NOTE: Silicone DOT 5 brake fluid is NOT recommended for racing or performance driving.
•To properly bleed the brake system, begin with the caliper farthest from the master cylinder. Bleed the outboard bleed screw first, then
the inboard. Repeat the procedure until all calipers in the system are bled, ending with the caliper closest to the master cylinder. If the
caliper is fitted with bleed screws on four corners, make sure the bottom bleed screws are tight. Only bleed from the top bleed screws.
NOTE: When using a new master cylinder, it is important to bench bleed the master cylinder first.
•Test the brake pedal. It should be firm, not spongy, and stop at least 1 inch from the floor under heavy load.
If the brake pedal is spongy, bleed the system again.
If the brake pedal is initially firm, but then sinks to the floor, check the system for leaks. Correct the leaks (if applicable) and then
bleed the system again.
If the brake pedal goes to the floor and continued bleeding of the system does not correct the problem, either air may be trapped
in the system, or a master cylinder with increased capacity (larger bore diameter) may be required. Wilwood offers various
lightweight master cylinders with large fluid displacement capacities (custom fabricated mounting may be required).
Assembly Instructions (Continued)