General information – Wilwood Stealth Motorcycle Front Brake Kit User Manual
Page 3
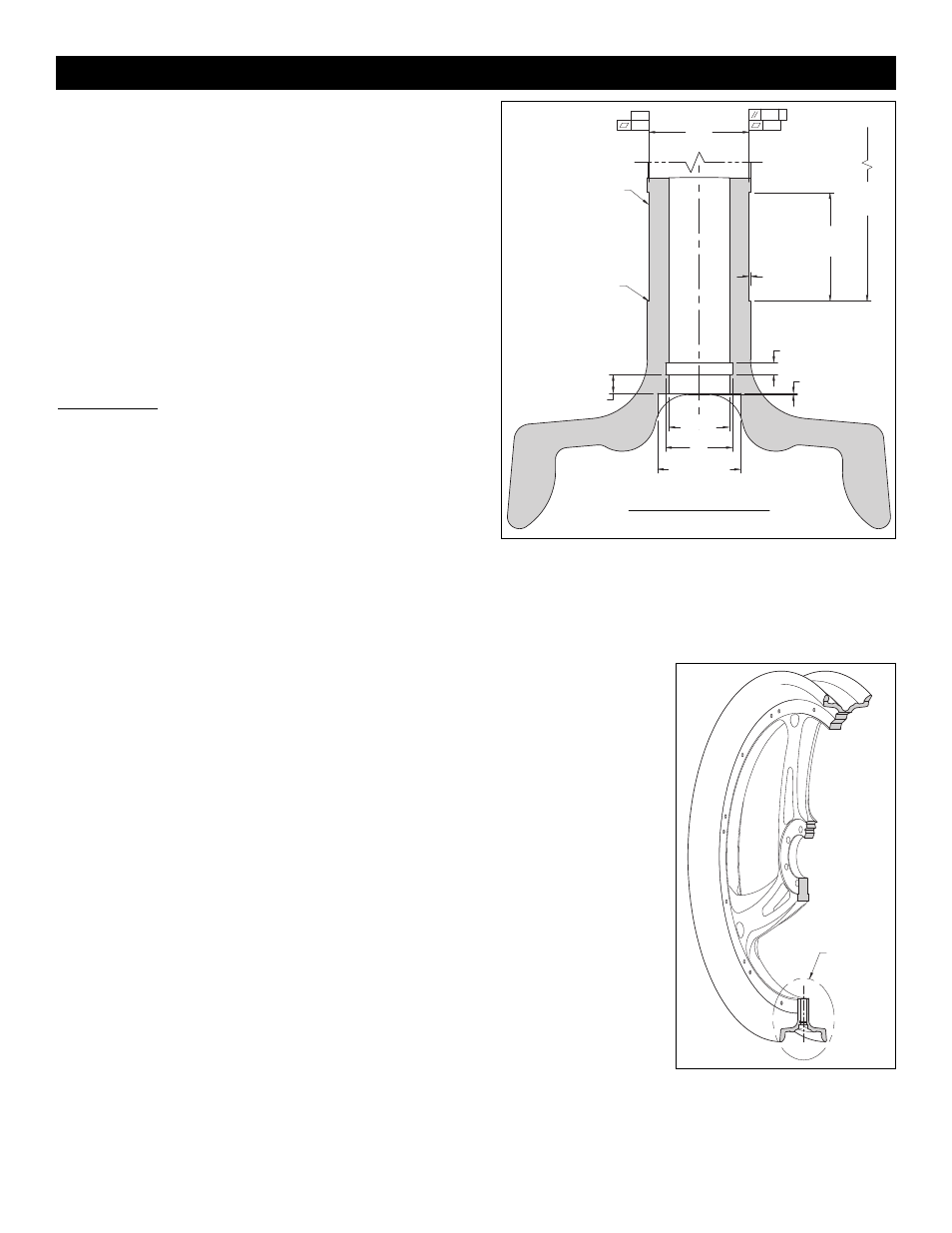
Installation of this kit should ONLY be performed by a trained
mechanic/machinist experienced in the installation and proper operation of
motorcycle disc brake systems. Read these instructions carefully before
beginning work to be sure that the procedures are thoroughly understood.
Before machinging and assembly of the Wilwood Stealth front caliper disc
brake kit, double check the following items to ensure a trouble-free
installation.
•Make sure this is the correct kit to match the exact year and model Harley-
Davidson® for which installation is intended.
•Inspect the package contents against the parts list to ensure that all
components and hardware are included.
•This kit contains rotor segments that need to be applied to a customer
supplied machined wheel. This machining needs to be performed by a
qualified machine shop.
INSTRUCTIONS:
•The dimensions as outlined in figure 1 are for the installation of Wilwood
rotor segments (2). These segments are specifically designed for use with
a 21.00” by 2.15” machined wheel. After you have machined your wheel
per figure 2, being careful not to allow machining in the rotor area other
than for the 10-24 threaded holes. Also, remembering to drill for your
valve stem. Figure 2 valve stem detail is for reference only. Actual
dimensions may vary depending on your valve stem requirements.
Wilwood does not supply a valve stem. Valve stem must be oriented on
the wheel centerline as shown. Maximum through hole allowable is .453”.
•A typical fully machined wheel is shown for reference in figure 3.
•Proceed to prepare the wheel for the installation of the rotor segments.
First drill 18 10-24 threaded through holes on both sides of the wheel per
the dimensional characteristics of figure 1.
•Check rotor mounting surfaces for distortion after drilling valve stem hole. No distortion of rotor mounting
surfaces is allowable.
•Install the rotor segments (2) to the machined wheel using bolts (3). Before installation, apply red Loctite
®
271 to the bolt threads and torque bolts to 40-50 in-lbs. being sure bolt heads are completely flush or
below rotor segment surface.
•The caliper (1) mounts to the front leg support as shown in figure 4. The caliper mounting installation
holes are tapped for 5/16-18 bolt threads. Customer supplies their own caliper mounting bolts. These
bolts are then torqued to applicable specifications depending upon the grade bolt utilized. The use of blue
Loctite
®
is solely at the discretion of the installer.
•NOTE: The Stealth caliper inlet fitting is a 3/8-24 thread. A banjo bolt fitting is used at the caliper with
sealing (crush) washers. Banjo bolt thread engagement should not shorter than .375" or too long to cause
it to bottom out at the end of the threads (see figure 4). Use enough steel braided line to allow for full
suspension travel and turning radius, lock to lock. Carefully route lines to prevent contact with moving
suspension, brake or wheel components. It is the installer's responsibility to properly route and ensure
adequate clearance and retention for brake hose components..
•Specified brake hose kits may not work with all Years, Makes and Models of vehicle that this brake kit is
applicable to, due to possible OEM manufacturing changes during a production vehicle's life. It is the
installer's responsibility to ensure that all fittings and hoses are the correct size and length, to ensure
proper sealing and that they will not be subject to crimping, strain and abrasion from vibration or
interference with suspension components, brake rotor or wheel.
•In absence of specific instructions for brake line routing, the installer must use his best professional
judgment on correct routing and retention of lines to ensure safe operation. Test vehicle brake system per
the 'minimum test' procedure stated within this document before driving. After road testing, inspect for
leaks and interference. Initially after install and testing, perform frequent checks of the vehicle brake
system and lines before driving, to confirm that there is no undue wear or interference not apparent from
the initial test. Afterwards, perform periodic inspections for function, leaks and wear in an interval relative
to the usage of vehicle.
General Information
Page 3
.750
_A_
A
.002
CL
.002
18.791
BOTH
SIDES
.813
BOTH
SIDES
MINIMUM
SKIM CUT
BOTH SIDES
.453 MAX.
THRU
.625 CBORE
TO DEPTH
SHOWN
VALVE STEM ORIENTATION DETAIL
.090
.140
.01
.503
SHOWN FOR REFERENCE ONLY - ACTUAL DIMENSIONS MAY
VARY DEPENDING ON YOUR VALVE STEM REQUIREMENTS
.030 RADIUS MAX
2 PLACES
BOTH SIDES
DO NOT ALLOW MACHINING
IN ROTOR AREA AND CHECK
FOR DISTORTION AFTER
DRILLING VALVE STEM HOLE
.002
Figure 2. Wheel Machining / Valve Stem Detail
“VALVE STEM
ORIENTATION”
SEE FIGURE 2
Figure 3. Fully Machined Wheel