Schneider Electric MS40-717X User Manual
Application, Features
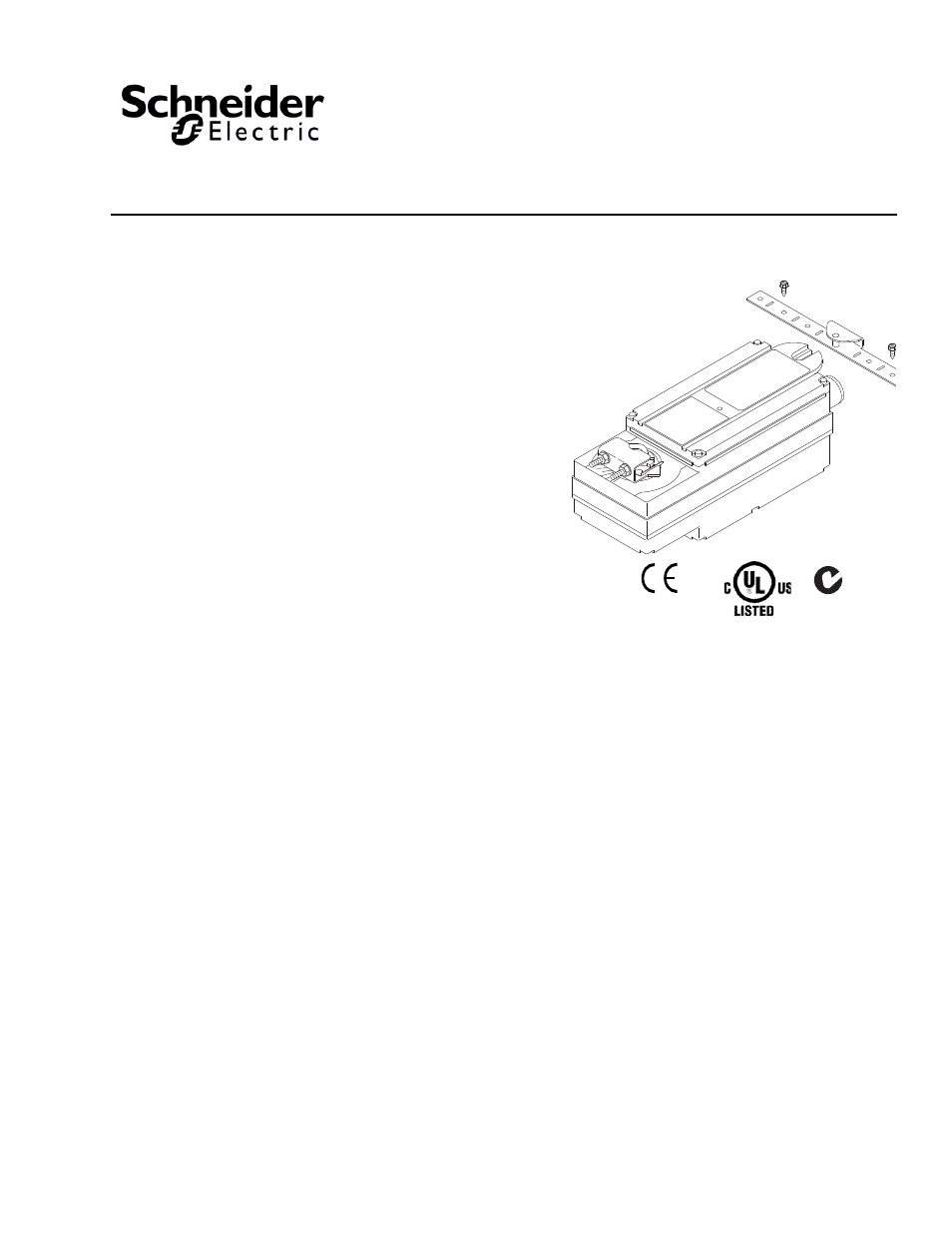
Printed in U.S.A.
1/10
© Copyright 2010 Schneider Electric All Rights Reserved.
F-26748-6
Application
DuraDrive
Direct Coupled Actuators are designed to be
used in both damper and valve control applications.
The following general instructions are for damper
applications, refer to the Applicable Literature table for
valve literature.
The MS40-717X series actuators are over the shaft
spring return actuators compatible with 2 to 10 Vdc or
4 to 20 mAdc
1
control signals.
Features
•
150 lb-in (17 N-m) rated torque
•
NEMA Type 4 housing (IEC IP56)
•
Custom automatic current sensing motor control
provides extended reliability and repeatable timing
•
Direct coupled to the damper shaft with dual
industrial hardened universal mounting clamps
•
Integral wiring for proportional control by 2 to 10 Vdc
or 4 to 20 mAdc
1
•
Clockwise or counterclockwise spring return is
determined by actuator mounting position
•
Accurate 92° travel digitally controlled
•
Integral position indication scale
•
Rugged die-cast housing
•
Oil immersed gear train provides continuous
lubrication
•
Integral transformer for high voltage systems
•
Rated for operating temperature up to 140 °F
•
Five year warranty
•
MS40-717x series actuators can be double-
mounted (gang mounting) to accommodate high
torque application requirements (2 to 4 actuators).
•
Position feedback signal
1.
With the addition of a 500 Ohm resistor - not in-
cluded
MS40-717X Series
DuraDrive™
Series Spring Return
Proportional Actuators
General Instructions
Document Outline
- Application
- DuraDrive Direct Coupled Actuators are designed to be used in both damper and valve control applications. The following general instructions are for damper applications, refer to the Applicable Literature table for valve literature.
- The MS40-717X series actuators are over the shaft spring return actuators compatible with 2 to 10 Vdc or 4 to 20 mAdc control signals.
- Features
- . 150 lb-in (17 N-m) rated torque
- . NEMA Type 4 housing (IEC IP56)
- . Custom automatic current sensing motor control provides extended reliability and repeatable timing
- . Direct coupled to the damper shaft with dual industrial hardened universal mounting clamps
- . Integral wiring for proportional control by 2 to 10 Vdc or 4 to 20 mAdc1
- . Clockwise or counterclockwise spring return is determined by actuator mounting position
- . Accurate 92° travel digitally controlled
- . Integral position indication scale
- . Rugged die-cast housing
- . Oil immersed gear train provides continuous lubrication
- . Integral transformer for high voltage systems
- . Rated for operating temperature up to 140 °F
- . Five year warranty
- . MS40-717x series actuators can be double- mounted (gang mounting) to accommodate high torque application requirements (2 to 4 actuators).
- . Position feedback signal
- Applicable Literature
- SPECIFICATIONS
- Class 1 Power
- Class 2 Power & Control
- Ground,
- Position Feedback Voltage
- Stroke
- Action
- Anti-Rotation Bracket
- Universal Mounting Clamps,
- Minimum Damper Shaft Length
- Position Indicator
- Nominal Damper Area
- Direction of Rotation
- Shipping & Storage,
- Operating,
- Humidity:
- Location:
- Agency Listings
- Table-1 Model Chart.
- TYPICAL APPLICATIONS (wiring diagrams)
- Figure-1 Typical MS40-7170 2 to 10 Vdc Wiring Diagram.
- Figure-2 Typical MS40-7170 4 to 20 mA Wiring Diagram.
- Figure-3 Typical MS40-7171 2 to 10 Vdc Wiring Diagram.
- Figure-4 Typical MS40-7171 4 to 20 mA Wiring Diagram.
- Figure-5 Typical MS40-7173 2 to 10 Vdc Wiring Diagram.
- Figure-6 Typical MS40-7173 4 to 20 mA Wiring Diagram.
- Figure-7 Two Actuators on the Same Damper Shaft.
- Figure-8 Typical 4 to 20 mAdc Control Wiring For Two Actuators On The Same Damper Shaft.
- INSTALLATION
- Precautions
- Mounting
- Damper Actuator Sizing
- Damper Shaft Sizing
- Mounting the Actuator for Clockwise or Counterclockwise Dampers
- Long Damper Shafts
- 1. Move the damper to its normal position. Verify the controller action is set to match the damper application (normally closed or normally open). See TYPICAL APPLICATIONS (wiring diagrams).
- 2. Slide the actuator over the shaft and into its desired final mounting position.
- 3. Hand tighten the nuts on both of the actuator’s universal mounting clamps.
- 4. Align the actuator at 90° (perpendicular) to the damper shaft. See Figure-12.
- 5. Slide the anti-rotation bracket pin into the mounting slot on the actuator and drill mounting holes. See Figure-12. For narrow spaces the AM-752 anti-rotation bracket is recommended (order separately).
- 6. Attach one side of the anti-rotation bracket to the mounting surface with one of the screws provided. Leave the screw loose so that the bracket can be rotated. See Figure-10 for clockwise or Figure-11 for counterclockwise spring return.
- 7. Pivot the anti-rotation bracket away from the actuator. See Figure-10 or Figure-11.
- 8. Loosen the universal mounting clamps, making sure not to move the damper shaft. Rotate the actuator approximately 5° in the direction which would open the damper. See Figure-10 or Figure-11.
- 9. Tighten all of the universal mounting clamp nuts with a 1/2" socket wrench. Apply 4 to 6 ft -lbs (5 to 8 N-m) of torque.
- 10. Manually rotate the actuator toward the full-closed position to apply pressure to the damper seals. See Figure-10 or Figure-11.
- 11. Pivot the anti-rotation bracket into place and secure the other side of the bracket onto the mounting surface using the other screw provided with the actuator. See Figure-10 or Figure-11.
- 12. Verify that the damper is in its full-closed position and actuator at 90° (perpendicular) to the damper shaft. See Figure-10 or Figure-11.
- 1. Move the damper to its normal position. Verify the controller action is set to match the damper application (normally closed or normally open). See TYPICAL APPLICATIONS (wiring diagrams).
- Figure-10 Long Damper Shaft Mounting with Clockwise Spring Return for Normally Closed Damper.
- Figure-11 Long Damper Shaft Mounting with Counterclockwise Spring Return for Normally Closed Damper.
- Figure-12 Mounting Anti-rotation Bracket to Actuator.
- Long Damper Shafts
- Short Damper Shafts
- 1. Loosen the V-clamp nuts on the AM-676 universal shaft extension.
- 2. Fit the universal shaft extension fully onto the damper shaft. Tighten the universal shaft extension V-clamp nuts with a 10 mm open-end wrench. Apply 4 to 6 ft. lbs (5 to 8 N-m) of torque.
- 3. Move the damper to its normal position. Verify the controller action is set to match the damper application. See TYPICAL APPLICATIONS (wiring diagrams).
- 4. Remove the mounting clamps from the actuator and replace them with the AM-753 universal mounting clamps.
- 5. Loosen the nuts on both of the AM-753 universal mounting clamps on the damper actuator.
- 6. Assemble the damper actuator onto the universal shaft extension, allowing the extension to slide through the actuator’s unive...
- 7. Slide the anti-rotation bracket pin into the mounting slot on the actuator. See Figure-12. For narrow spaces, the AM-752 anti-rotation bracket is recommended (order separately).
- 8. Position the actuator and bracket in the desired final mounting position on the mounting surface and drill mounting holes. See Figure-13.
- 9. Attach one side of the anti-rotation bracket to the mounting surface with one of the screws provided. Leave the screw loose so that the bracket can be rotated. See Figure-10 for clockwise or Figure-11 for counterclockwise spring return.
- 10. Pivot the anti-rotation bracket away from the actuator. See Figure-10 or Figure-11.
- 11. Loosen the universal mounting clamps, making sure not to move the damper shaft. Rotate the actuator approximately 5° in the direction which would open the damper. See Figure-10 or Figure-11.
- 12. Tighten all of the universal mounting clamp nuts with a 1/2" socket wrench. Apply 4 to 6 ft-lbs (5 to 8 N-m) of torque.
- 13. Manually rotate the actuator toward the full-closed position to apply pressure to the damper seals. See Figure-10 or Figure-11.
- 14. Pivot the anti-rotation bracket into place and secure the other side of the bracket onto the mounting surface using the other screw provided with the actuator. See Figure-10 or Figure-11.
- 15. Verify that the damper is in its full-closed position and actuator at 90° (perpendicular) to the damper shaft. See Figure-10 or Figure-11.
- Figure-13 Installation of Universal Shaft Extension.
- Wiring Requirements
- 1. Loosen the V-clamp nuts on the AM-676 universal shaft extension.
- CHECKOUT
- 1. Apply power to the actuator and control system.
- 2. Set the controller to cause the actuator to drive open (set override controller output to maximum).
- 3. Check to see that the actuator travels to the full-open position.
- 4. Set the controller to cause the actuator to drive closed (set override controller output to minimum).
- 5. Check to see that the actuator travels to the fully closed position.
- THEORY OF OPERATION
- MAINTENANCE
- FIELD REPAIR
- 1. Apply power to the actuator and control system.
- DIMENSIONAL DATA