Troubleshooting guide, Instructions included – Whirlpool WHES20 User Manual
Page 29
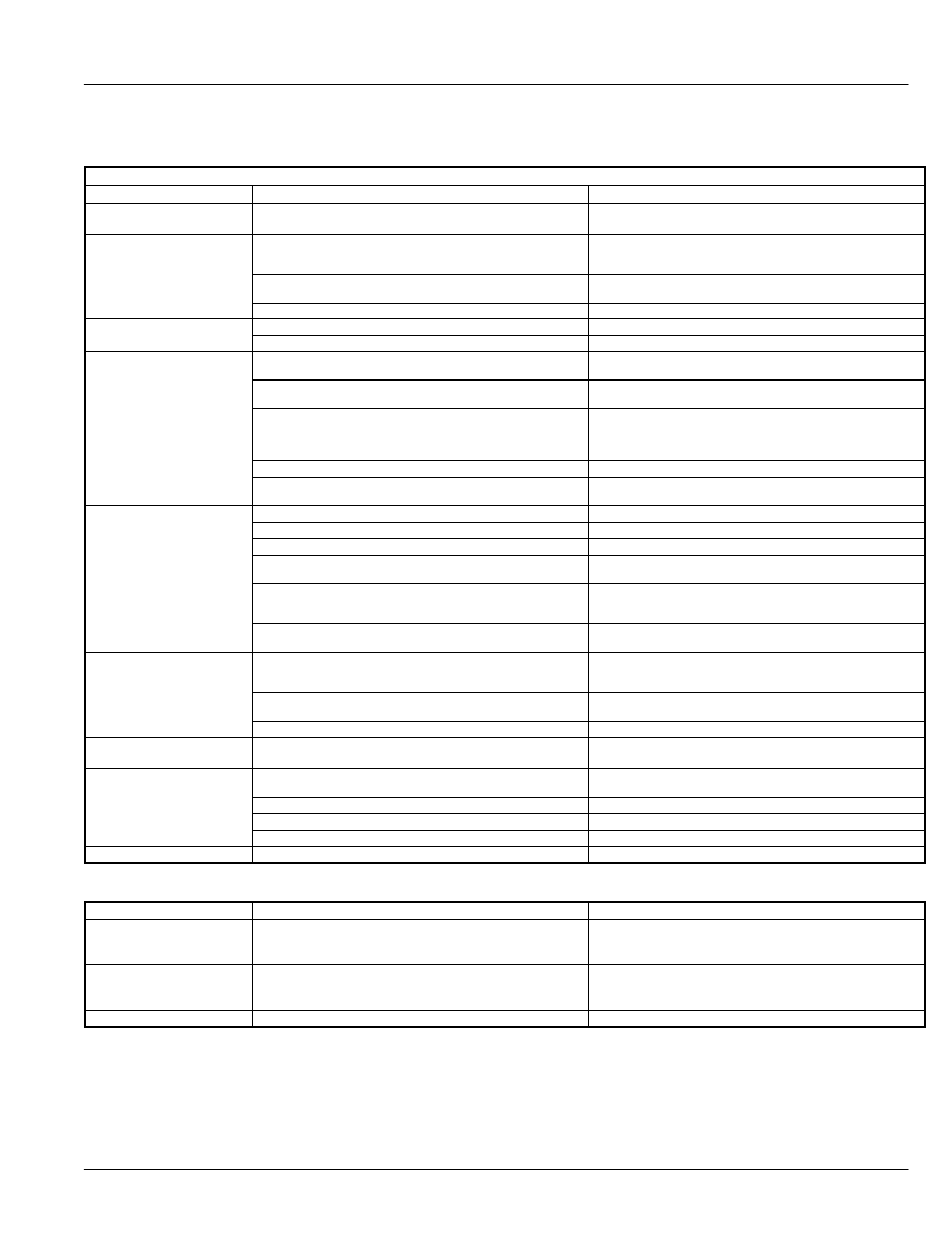
29
Troubleshooting Guide
Need help troubleshooting? Call 1--866--986--3223, Monday -- Friday, 8 am to 9 pm, EST.
Tools Needed For Most Repairs: 5/16 Hex Driver, Phillips Screwdriver, Needle---nose Pliers
PROBLEM
CAUSE
SOLUTION
No Soft Water
1. No salt in the storage tank.
a. Refill with salt.
b. Use Recharge feature.
No Soft Water Timer
Display Blank
1. Transformer unplugged at wall outlet, or power cable
disconnected from back of electronic board, transformer
defective.
a. Check for loss of power and correct. Reset electronic controls
and use the Recharge feature.
2. Fuse blown, circuit breaker popped, or circuit switched off.
(See page 24 “Power Outage Memory”).
a. Replace fuse, reset circuit breaker, or switch circuit on use the
Recharge feature.
3. Electronic control board defective.
a. Replace Electronic Control Board (PWA). *
No Soft Water Salt Level
1. Salt in storage tank bridged.
a. Refer to “Breaking a Salt Bridge” section to break.
No Soft Water Salt Level
Not Dropping
2. Manual bypass valve(s) in bypass position.
a. Move stem in single valve bypass to service.
No Soft Water, Salt
Storage Tank Full Of
1. Dirty, plugged or damaged nozzle & venturi.
a. Take apart, clean and inspect nozzle and venturi, see
“Cleaning the Nozzle and Venturi” section.
Storage Tank Full Of
Water
2. Valve drain hose plugged.
a. Hose must not have any kinks, sharp bends or any water flow
blockage, see “Valve Drain Requirements” section.
3. Low or high system water pressure (low pressure may disrupt
brine draw during recharge, high pressures may cause inner
valve parts failure).
a. If pressure is low, increase well pump output to a minimum 20
psi. Add a pressure reducing valve in the supply pipe to the
softener, if daytime pressure is over 100 psi. Contact a licensed
plumber.
4. Brine valve float dirty or defective.
a. Clean or replace Brine Valve Float assembly. *
5. Leak between valve and resin tank assembly.
a. Replace o---rings between resin tank and valve. See water
softener components.
Water Hard Sometimes
1. Time setting wrong.
a. Check and change time setting.
Water Hard Sometimes
2. Incorrect water hardness setting.
a. Refer to “Set Water Hardness Number” section to set correctly.
3. Incorrect model code programmed.
a. Refer to “Program The Water Softener” section to set correctly.
4. Hot water being used when softener is regenerating.
a. Avoid using hot water while the softener is regenerating as the
water heater will fill with hard water.
5. Possible increase in water hardness.
a. Test the raw water for hardness and iron and program the
water softener accordingly, see “Set Water Hardness Number”
section to set.
6. Leaking faucet or toilet valve. Excessive water usage.
a. A small leak will waste hundreds of gallons of water in a few
days. Fix all leaks and always fully close faucets.
Iron In Water
1. Clear water iron in water supply.
a. Test the raw water for hardness and iron and program the
water softener accordingly see “Set Water Hardness Number”
section to set.
2. Iron in soft water.
a. Clean resin bed with Resin Bed Cleaner. Follow instructions on
package.
3. Bacterial or organic bound iron.
a. Cannot be treated by water softener.
Motor Stalled Or Clicking
1. Motor defective or inner valve defect causing high torque on
motor.
a. Replace rotor/seal kit.*
b. Replace motor & switch. See water softener components.
Error Code E1, E3, or E4
appears
1. Wiring Harness or Connection to Position Switch.
a. Replace wiring harness or connection to position switch. See
water softener components.
appears
2. Switch.
a. Replace switch. See water softener components.
3. Valve Defect Causing High Torque.
a. Replace rotor/seal kit.*
4. Motor Inoperative.
a. Replace motor. *
Error Code E5 appears
1. Electronic Control.
a. Replace Electronic Control Board (PWA). *
Assistance from customer service may be needed with the following problems and solutions.
PROBLEM
CAUSE
SOLUTION
Water Running To The
Drain (While Unit Is In The
Soft Water Cycle)
1. Inner valve defect causing leak.
a. Replace seals and rotor.
Resin In Household
Plumbing, Resin Tank
Leaking
1. Crack in distributor or riser tube.
a. Replace distributor or riser tube.
Salt Storage Tank Leaking
1. Crack in brine tank.
a. Replace salt storage tank.
* Instructions included.
Procedure for removing error code from faceplate:
1. Unplug transformer from outlet.
2. Correct defect.
3. Plug in transformer.
4. Wait for 6 minutes. The error code will return if the defect was not corrected.