Maintenance, Draining and cleaning, Keeping air vent clean – Weil-McLain PER 550-141-396/0801 User Manual
Page 10: Checking relief valve, Checking expansion tank, Operating temperature and pressure
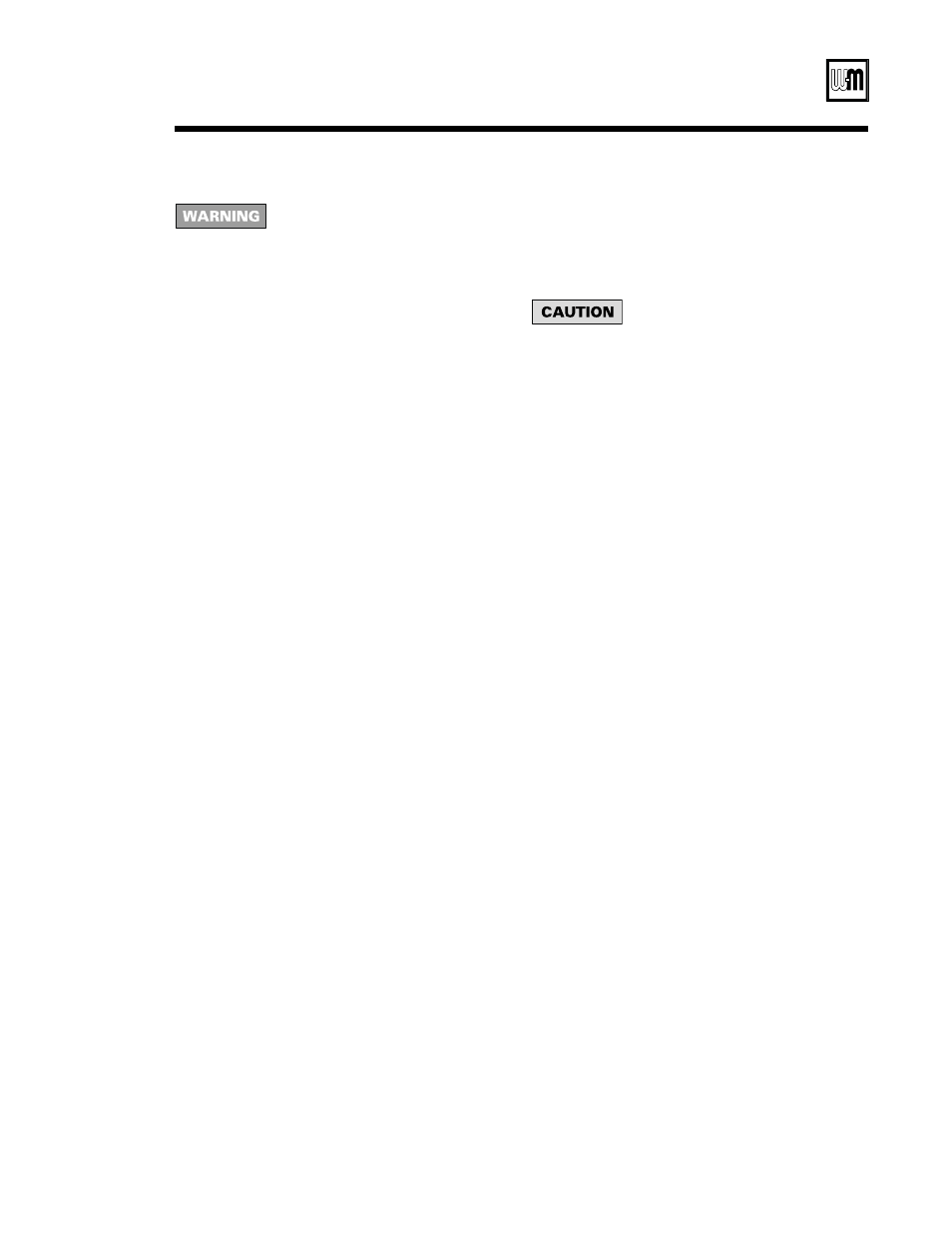
Part number 550-141-396/0801
10
PER Series 3 Electric-Hydronic Boilers Installation Instructions
Maintenance
Draining and cleaning
Do not drain the boiler during periods of shutdown
unless the heating system is exposed to freezing
temperatures. At the end of each heating season, open
the boiler drain cock just long enough to remove any
impurities or sediment that may have settled to the
bottom of the boiler.
Keeping air vent clean
Loosen the cap on the Float-Type Automatic Air Vent
two turns while the system is being filled with water.
Should dirt or scale lodge on the valve seat causing it to
leak, remove the vent cap and push the valve core in by
hand to permit water to flush the valve seat clean; release
the valve core quickly and replace the vent cap. For
normal operation and venting, unscrew the vent cap at
least two turns.
Checking relief valve
Check the relief valve once a year by manually opening
the valve and allowing a small quantity of water to flow.
Make sure that the valve reseats and does not leak.
Replace any defective valve.
Checking expansion tank
Undersized expansion tanks cause
system water to be lost from relief
valve and makeup water added
through fill valve. Eventual section
failure can result.
If the relief valve opens frequently, check the expansion
tank. If the system has a pressurized tank with a rubber
diaphragm separating the air cushion from the water
(an Ex-Trol or equivalent tank), use a tire pressure gauge
to check the air-charging valve on the end of the tank.
If water flows, the diaphragm is ruptured or leaking.
The tank must be replaced. If no water flows but the air
charge has been lost, recharge the tank to 12 pounds
per square inch. Periodic air loss from the expansion
tank probably means a leaky charging valve.
If the expansion tank is of the standard closed variety,
(without a rubber diaphragm) the tank must be partly
drained to re-establish an air cushion.
Operating temperature and
pressure
The maximum recommended low and high limit
control settings are 200
°
F and 220
°
F, respectively. The
relief valve opens at 30 pounds per square inch. The
actual operating pressure will range from 12 pounds
per square inch when the system is cold to as much as
15 pounds per square inch at maximum operating
temperature.
This boiler contains fiberglass materials. Use care when handling these materials per instructions
on page 11 of this manual. Failure to comply could result in severe personal injury.