Hydronic heating – Raypak HI DELTA 122-322 User Manual
Page 13
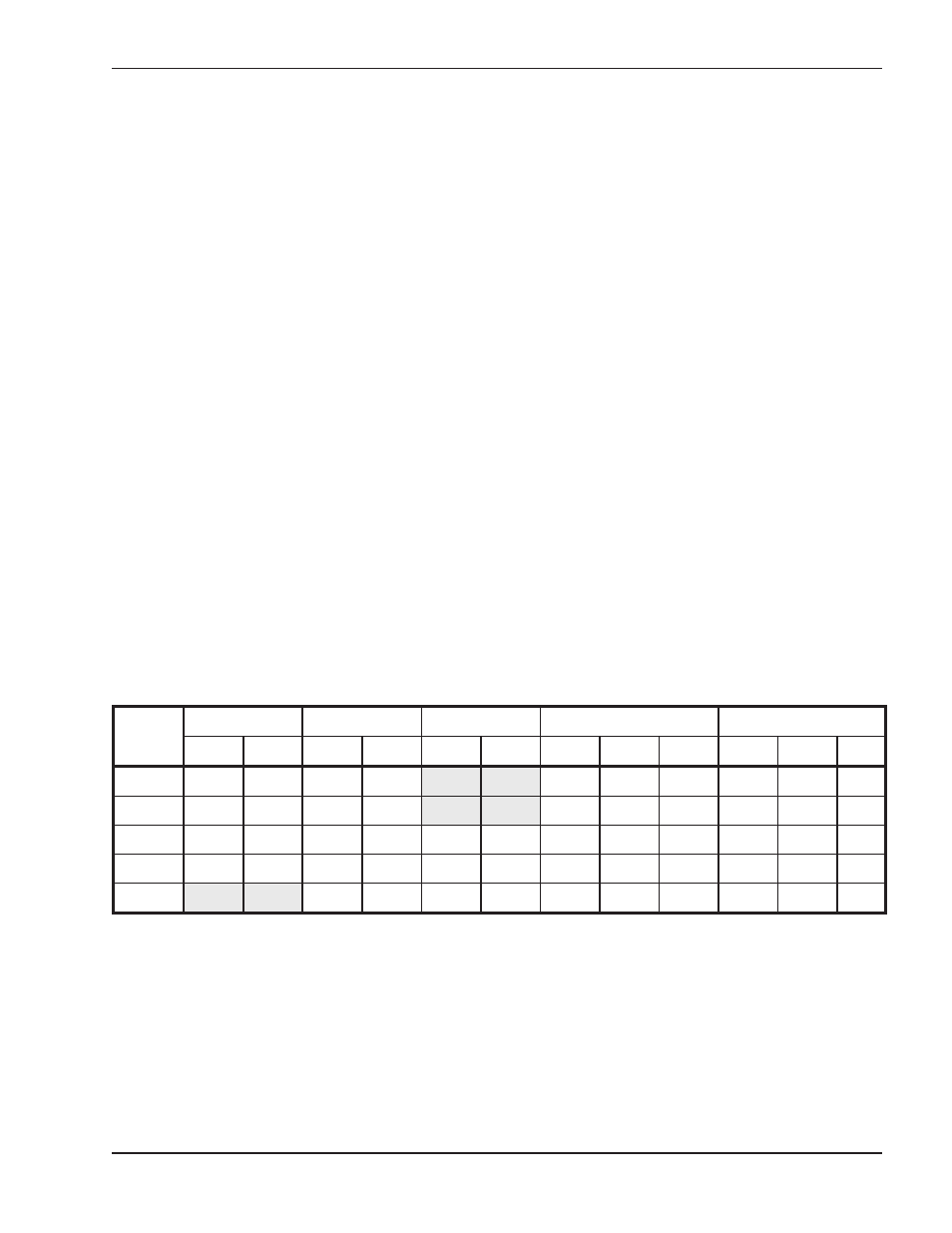
13
Low Temperature System
Heater requires minimum inlet temperature of 105°F.
Consult the following sections for piping details.
Temperature & Pressure Gauge
The temperature and pressure gauge is factory-
mounted in the in/out header.
Hydronic Heating
Pump Selection
In order to ensure proper performance of your boiler
system, you must install a properly sized pump.
Raypak recommends using a 20°F Delta T as design
Delta T. (Delta T is the temperature difference between
the inlet and outlet water when the heater is firing at
full rate). If a Delta T larger than 20°F is necessary,
see Table F for minimum flow rate requirements.
Pressure Drop in Feet of Head
Feedwater Regulator
Raypak recommends that a feedwater regulator be
installed and set at 12 PSIG minimum pressure at the
highest point of system. Install a check valve or back
flow device upstream of the regulator, with a manual
shut off valve as required by local codes.
Model
No.
10°F ΔT
20°F ΔT
30°F ΔT
Min. Flow
Max. Flow
gpm
ΔP (ft)
gpm
ΔP (ft)
gpm
ΔP (ft)
gpm
ΔP (ft)
ΔT
gpm
ΔP (ft)
ΔT
122
20
2.5
10
<1.0
10*
<1.0
20
30
5.3
7
162
27
4.5
13
1.10
10
<1.0
27
30
5.4
9
202
34
7.2
17
1.85
11
<1.0
10
<1.0
34
30
5.5
11
242
40
10.0
20
2.65
14
1.3
10
<1.0
40
44
11.8
9
322
27
4.70
18
2.2
14
1.4
40
44
12.2
12
Table F: Heater Rates of Flow and Pressure Drops
* Flow switch (when used) will not activate at less than 12 gpm.
NOTE: Basis for minimum flow - 10 gpm or 40° Delta T
maximum flow - 44 gpm, except for 1.25” header.
Hydrostatic Test
Unlike many other types of heaters, Raypak heaters
do not require hydrostatic testing prior to being placed
in operation. The heat exchanger has already been
factory-tested and is rated for 160 PSI maximum oper-
ating pressure. However, Raypak does recommend
hydrostatically testing the piping connections to the
heater and the rest of the system prior to operation.
This is particularly true for hydronic systems using
expensive glycol-based antifreeze. Raypak recom-
mends conducting the hydrostatic test before
connecting gas piping or electrical supply.
Leaks must be repaired at once to prevent damage to
the heater. NEVER use petroleum-based stop-leak
compounds.
1. Connect fill water supply. Fill heater with water (be
sure bleed valve is open). When water flows from
bleed valve, shut off water. Close bleed valve.
Carefully fill the rest of the system, being sure to
eliminate any entrapped air by using high point
vents. Close feed valve. Test at standard operating
pressure for at least 24 hours.
2. Make sure constant gauge pressure has been
maintained throughout test.
3. Check for leaks. Repair if found.