Servis-Rhino 2412 User Manual
Operator’s manual, Loader
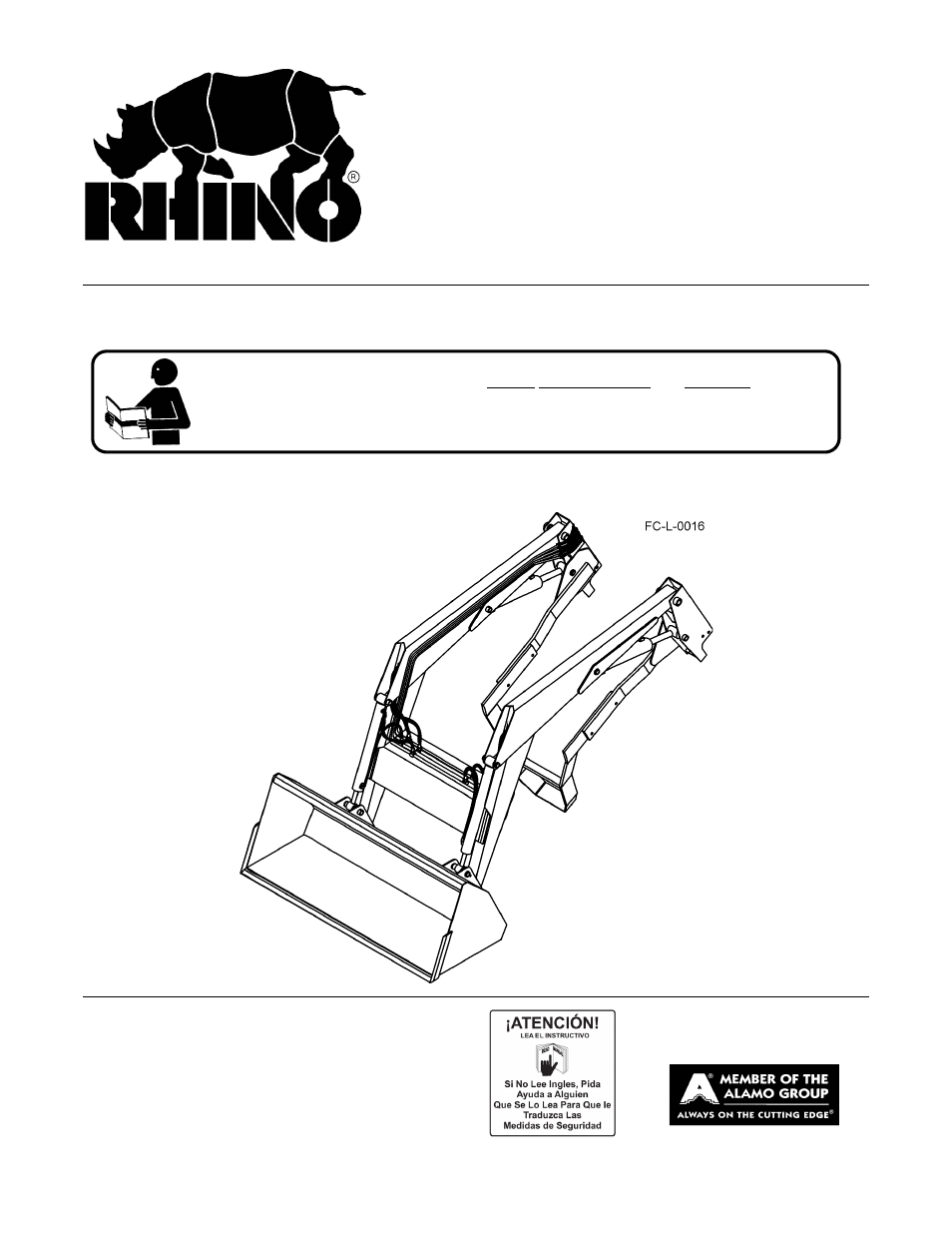
© 2011 Alamo Group Inc.
$0.00
2412
Published 01/11
Part No.
F-3660C
OPERATOR’S MANUAL
RHINO
®
1020 S. Sangamon Ave.
Gibson City, IL 60936
800-446-5158
Email: [email protected]
LOADER
This Operator's Manual is an integral part of the safe operation of this machine and must
be maintained with the unit at all times. READ, UNDERSTAND, and FOLLOW the Safety
and Operation Instructions contained in this manual before operating the equipment. C01-
Cover
Table of contents
Document Outline
- 2412
- OPERATOR’S MANUAL
- To the Owner/Operator/Dealer
- TABLE OF CONTENTS
- General Safety Instructions and Practices
- Equipment Operation Safety Instructions and Practices
- Maintenance and Service Safety Instructions and Practices
- Concluding Safety Instructions and Practices
- Decal Location
- 1. 49696 1 LOGO Rhino, Left
- 2. 51448 1 LOGO Rhino, Right
- 3. 50286 2 MODEL 2412
- 4. 52740 2 WARNING Oil Leaks
- 5. 52203 1 WARNING Lock Valve in Transport
- 6. 52204 1 INSTRUCT Loader Positions
- 7. D469 1 WARNING Loader Safety
- 8. D468 2 DANGER Crushing, Electrocution, Falling Hazard
- 9. D471 1 WARNING Handling Bales
- 10. D470 1 DANGER Use ROPS, Seatbelt, Rear Ballast
- 11. 03200347 * REFLCTR SMV Sign
- 12. 00776031 1 _________ Canister, Operator’s Manual
- Decal Description
- Decal Location
- Federal Laws and Regulations
- Assembly Instructions
- Proper Ballasting and Wheel Spacing
- Assembly
- Dismounting Loader and Mounting Loader to Tractor
- Dismounting Loader
- 1. Locate tractor and loader on firm level ground.
- 2. Level the bucket and lower it to the ground. Engage the tractor brakes and shut off the tractor engine. Move the lift control lever back and forth several times to relieve pressure in the lift cylinders
- 3. Loosen the 3/4 x 3-1/2 cap screws which clamp the hinges closed around the midmounting tubes. Remove cap screws, washers and lock nuts. Place washer onto cap screw, hold hinge open as wide as possible, then insert cap screw through the hole provid...
- 4. Remove the rubber strap which secures the hoses to the loader front support bracket. Remove any tie straps which attach hoses to tractor or brackets.
- 5. Start the tractor engine and release tractor brakes. Lower loader boom slightly as necessary to distribute the weight of the loader equally between the front mounting bracket and midmounting brackets. This can also be accomplished by using the boo...
- 6. Move lift and bucket control levers back and forth several times to relieve pressure on the lift and bucket cylinders. Disconnect quick couplers between the loader and tractor. Hang hoses over the side frame for storage. If tractor is equipped wit...
- Preparing Stored Loader for Mounting
- 1. Slowly back the tractor up to the loader until hoses will reach from loader to tractor remote couplers. Engage the tractor brakes and shut off the tractor engine.
- 2. Making sure quick couplers are clean, connect quick couplers between the tractor and loader. Match color coded bands when connecting couplers.
- 3. Start the tractor engine and release tractor brakes. Operate the lift control valve to extend the lift cylinders as far as possible.
- 4. Once the lift cylinders are fully extended, shut off the tractor engine and engage the tractor brakes. Move the loader control levers back and forth to relieve pressure in the cylinders, then disconnect the quick couplers.
- 5. Start the tractor engine, release the tractor brakes, slowly drive the tractor up to loader
- 1. Slowly drive the tractor up to the loader until hoses will reach from 1-lever auxiliary valve to tractor. Engage tractor brakes and shut off tractor engine.
- 2. Reinstall valve support assembly into the valve support guide tube. Connect quick couplers by matching color coded bands.
- 3. Start the tractor engine and release tractor brakes. Operate the lift control to extend the lift cylinders as far as possible.
- Mounting Procedure
- 1. Slowly drive the tractor up to loader until hoses will reach from the loader to the tractor. Engage the tractor brakes and shut off tractor engine.
- 2. Connect quick couplers between tractor and loader, matching color coded bands.
- 3. Start tractor engine and release tractor brakes. Slowly drive the tractor ahead while activating lift control lever to retract lift cylinders. Position tractor so hinges hook midmounting bracket tubes as loader side frame uprights rotate.
- 4. Put the tractor in neutral. Retract the lift cylinders bringing the side frame channels up so front support bracket tube contacts front mounting bracket channel. Move the tractor ahead so front support bracket tube engages in front mounting bracke...
- 5. Remove 3/4 x 3-1/2 cap screw with washer which blocked hinge open and remove elastic lock nut from extra threads on hinge carrier bolt. Clamp hinge of upright around the midmounting tube. Insert 3/4 x 3-1/2 cap screw down through upright and hinge...
- 6. Hook the rubber strap from hoses to loader support bracket. Reinstall reusable tie straps.
- OPERATION SECTION
- Dismounting Loader
- RHINO 2412 LOADER
- OPERATION INSTRUCTIONS
- 1. Standard Equipment and Specifications
- 2. Operator Requirements
- 3. Tractor Requirements
- 4. Getting On and Off the Tractor
- 8. Operating the Tractor and Loader
- 9. Operating the Loader
- FILLING THE BUCKET
- LIFTING THE LOAD
- CARRYING THE LOAD
- DUMPING THE BUCKET
- OPERATING WITH FLOAT CONTROL
- LOADING FROM A BANK
- PEELING AND SCRAPING
- LOADING LOW TRUCKS OR SPREADERS FROM A PILE
- BACKFILLING
- 9.1 Operating Bale Spear
- 9.2 Shutting Down the Implement
- 9. Operating the Loader
- 10. Loader Storage
- 11. Transporting the Tractor and Implement
- 11.1 Transporting on Public Roadways
- 11.2 Hauling the Tractor and Implement
- 12. Troubleshooting Guide
- Loader slow or will not lift Hydraulic oil too heavy. Change to proper oil.
- and/or dump
- Oil filter plugged. Clean or replace filter.
- Hydraulic pump worn. Repair or replace pump.
- Oil line restricted or leaking. Check all hoses and tubes for leaks,
- damage or restrictions. Replace
- damaged or restricted hoses or tube
- oil lines.
- Control valve does not shift Inspect, clean, repair or replace
- properly. valve.
- Air in hydraulic system. Cycle lift cylinders and bucket
- cylinders several times to free
- system of air.
- Cylinder leaks internally. Replace seals.
- Faulty relief valve (tractor). Clean and replace relief valve.
- Loader chatters or Air leak in pump inlet line. Check, tighten or replace inlet line.
- vibrates when raising
- or lowering
- Air in hydraulic system. Cycle lift and bucket cylinders.
- Oil level too low. Add oil as required.
- *Boom delay at start Air in system. Cycle lift cylinders and bucket
- of self-level or unstable cylinders several times to free
- self-level system of air.
- *Loaded bucket dumps Unloading spool is leaking. Remove and inspect unloading
- or uncurls when control spool for damage.
- valve is in neutral
- Control linkage binding. Inspect, adjust or repair linkage.
- Cylinder seals bypassing oil. Repair or replace cylinders.
- *Insufficient self-level Set screw is out of adjustment. Readjust set screw to achieve
- proper flow split.
- Spring on unloading spool Remove plug; replace unloading
- is broken. spool spring.
- Flow divider spool is stuck Remove flow divider spool and
- towards adjustment pin side. inspect for damage.
- PROBLEM POSSIBLE CAUSE REMEDY
- *With bucket dumped, Dampening office in unloading Remove unloading spool and clean
- boom is slow in starting spool is plugged. dampening orifice.
- *Bucket does not move Set screw is screwed in all Readjust set screw to achieve
- in self-level the way. proper flow split.
- Dampening orifice in unloading Remove unloading spool and clean
- spool is plugged. dampening orifice.
- Ports A and B are plumbed Reverse hoses on ports A and B of
- backwards. self-level valve.
- *Bucket curls in self-level Ports C and D are plumbed Reverse hoses on ports C and D of
- backwards. self-level valve.
- *External leakage Damaged seals. Remove leaking component;
- replace seals.
- Excessive wear on bucket Bucket is riding on cutting edge Use boom “FLOAT” position or
- cutting edge instead of wear runners. bucket level indicator to ensure
- bucket rides on wear runners.
- *Bucket dumps faster than Set screw is out of adjustment. Readjust set screw to achieve
- boom raises. Too much proper flow split.
- self-level Flow divider spool is stuck Remove flow divider spool and
- towards port B. inspect for damage.
- Flow divider spool is installed Remove spool and install with
- wrong. internal orifice toward port B.
- *External leakage Damaged flow divider plug Remove plug and replace damaged
- o-ring. o-ring.
- Damaged plunger plug o-ring. Remove plug and replace damaged
- o-ring.
- Damaged unloading spool plug Remove plug and replace damaged
- o-ring. o-ring.
- Damaged adjustment cap o-ring. Remove adjustment cap and replace
- damaged o-ring.
- Leakage around set screw. Remove adjustment cap and replace
- damaged o-ring on set screw.
- MAINTENANCE SECTION
- Lubrication Schedule
- Daily Maintenance
- 1. Check fluid level of tractor hydraulic system before starting each day’s operation. If necessary, add hydraulic oil as recommended in your tractor operator’s manual.
- 2. After every four hours of operation, lubricate all twelve grease fittings; one at each end of lift boom arms and one at rod and base ends of each lift and bucket cylinder.
- 3. After every ten hours of operation, check all hardware and tighten where required.
- 4. Replace hoses immediately if they are damaged by a cut or scrape, extruded at the fittings or leaking. Hydraulic oil leaks should be repaired promptly to avoid loss of oil and serious personal injury from escaping oil.
- Storage
- Proper Torque for Fasteners
- RHINO
- LIMITED WARRANTY
- 1. LIMITED WARRANTIES
- 1.01. Rhino warrants for one year from the purchase date to the original non-commercial, governmental, or municipal purchaser (“Purchaser”) and warrants for six months to the original commercial or industrial purchaser (“Purchaser”) that the ...
- 1.02. Manufacturer will replace for the Purchaser any part or parts found, upon examination at one of its factories, to be defective under normal use and service due to defects in material or workmanship.
- 1.03. This limited warranty does not apply to any part of the goods which has been subjected to improper or abnormal use, negligence, alteration, modification, or accident, damaged due to lack of maintenance or use of wrong fuel, oil, or lubricants, ...
- 1.04. Except as provided herein, no employee, agent, Dealer, or other person is authorized to give any warranties of any nature on behalf of Manufacturer.
- 2. REMEDIES AND PROCEDURES.
- 2.01. This limited warranty is not effective unless the Purchaser returns the Registration and Warranty Form to Manufacturer within 30 days of purchase.
- 2.02. Purchaser claims must be made in writing to the Authorized Dealer (“Dealer”) from whom Purchaser purchased the goods or an approved Authorized Dealer (“Dealer”) within 30 days after Purchaser learns of the facts on which the claim is based
- 2.03. Purchaser is responsible for returning the goods in question to the Dealer.
- 2.04. If after examining the goods and/or parts in question, Manufacturer finds them to be defective under normal use and service due to defects in material or workmanship, Manufacturer will:
- (a) Repair or replace the defective goods or part(s) or
- (b) Reimburse Purchaser for the cost of the part(s) and reasonable labor charges (as determined by Manufacturer) if Purchaser paid for the repair and/or replacement prior to the final determination of applicability of the warranty by Manufacturer.
- 2.05. Purchaser is responsible for any labor charges exceeding a reasonable amount as determined by Manufacturer and for returning the goods to the Dealer, whether or not the claim is approved. Purchaser is responsible for the transportation cost for...
- 3. LIMITATION OF LIABILITY.
- 3.01. MANUFACTURER DISCLAIMS ANY EXPRESS (EXCEPT AS SET FORTH HEREIN) AND IMPLIED WARRANTIES WITH RESPECT TO THE GOODS INCLUDING, BUT NOT LIMITED TO, MERCHANTABILITY AND FITNESS FOR A PARTICULAR PURPOSE.
- 3.02. MANUFACTURER MAKES NO WARRANTY AS TO THE DESIGN, CAPABILITY, CAPACITY, OR SUITABILITY FOR USE OF THE GOODS.
- 3.03. EXCEPT AS PROVIDED HEREIN, MANUFACTURER SHALL HAVE NO LIABILITY OR RESPONSIBILITY TO PURCHASER OR ANY OTHER PERSON OR ENTITY WITH RESPECT TO ANY LIABILITY, LOSS, OR DAMAGE CAUSED OR ALLEGED TO BE CAUSED DIRECTLY OR INDIRECTLY BY THE GOODS INCLU...
- 3.04. NO ACTION ARISING OUT OF ANY CLAIMED BREACH OF THIS WARRANTY OR TRANSACTIONS UNDER THIS WARRANTY MAY BE BROUGHT MORE THAN TWO (2) YEARS AFTER THE CAUSE OF ACTION HAS OCCURRED.
- 4. MISCELLANEOUS.
- 4.01. Proper Venue for any lawsuits arising from or related to this limited warranty shall be only in Guadalupe County, Texas.
- 4.02. Manufacturer may waive compliance with any of the terms of this limited warranty, but no waiver of any terms shall be deemed to be a waiver of any other term.
- 4.03. If any provision of this limited warranty shall violate any applicable law and is held to be unenforceable, then the invalidity of such provision shall not invalidate any other provisions herein.
- 4.04. Applicable law may provide rights and benefits to purchaser in addition to those provided herein.
- TO THE OWNER/OPERATOR/DEALER