Servis-Rhino 60C User Manual
Operator’s manual
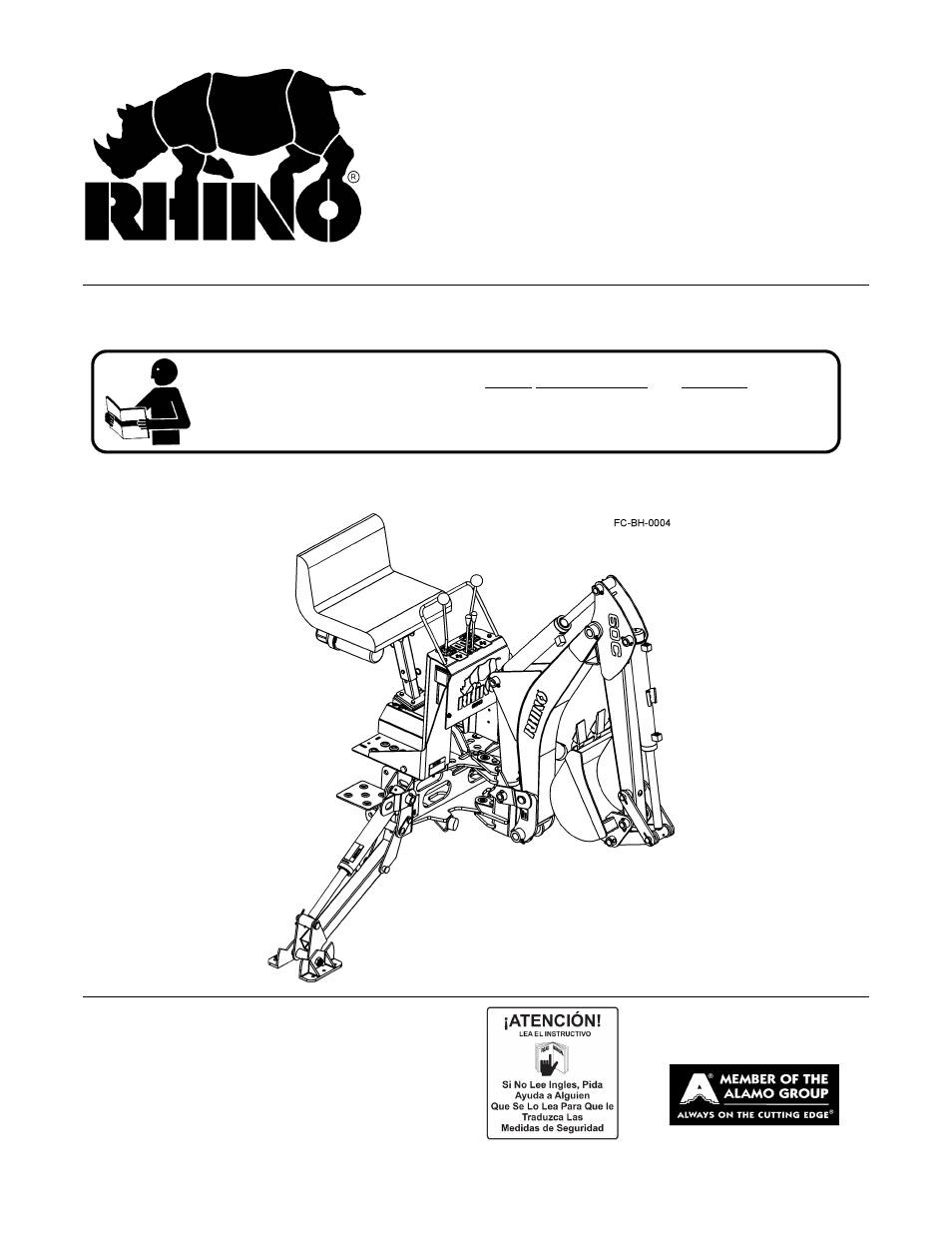
© 2011 Alamo Group Inc.
$0.00
60C
Published 01/11
Part No.
F-4139C
OPERATOR’S MANUAL
RHINO
®
1020 S. Sangamon Ave.
Gibson City, IL 60936
800-446-5158
Email: [email protected]
BACKHOE
This Operator's Manual is an integral part of the safe operation of this machine and must
be maintained with the unit at all times. READ, UNDERSTAND, and FOLLOW the Safety
and Operation Instructions contained in this manual before operating the equipment. C01-
Cover
Table of contents
Document Outline
- 60C
- OPERATOR’S MANUAL
- TO THE OWNER/OPERATOR/DEALER
- BACKHOE
- General Safety Instructions and Practices
- Connecting and Disconnecting Safety Instructions and Practices
- Equipment Operation Safety Instructions and Practices
- Transporting Safety Instructions and Practices
- Storage Safety Instructions and Practices
- Maintenance Safety Instructions and Practices
- Concluding Safety Instructions and Practices
- Decal Location
- 1. 45970 1 WARNING To Prevent Bodily Injury
- 2. 44907 1 WARNING To Prevent Instability
- 3. 44895 1 DANGER Crushing Hazard
- 4. 44896 1 WARNING To Prevent Bodily Injury
- 5. 44897 2 DANGER Crushing Hazard
- 6. 44898 1 OPERATION Boom Operation
- 7. 44899 1 OPERATION Dipperstick & Bucket Operation
- 8. 44900 1 OPERATION Left Side Stabilizer Position
- 9. 44901 1 OPERATION Right Side Stabilizer Position
- 10. 44908 1 OPERATION Boom Lock
- 11. 44909 1 OPERATION Swing Lock
- 12. 48280 1 INFORMATION Universal One Call
- 13. 54686 2 NAME Model Name 60C (Big)
- 14. 54687 1 NAME Model Name 60C (Small)
- 15. 54287 1 LOGO Rhino Logo
- 16. 54691 2 LOGO Rhino Logo
- Decal Location
- Decal Description
- Federal Laws and Regulations
- PRE-OPERATION CHECKLIST
- 1. All safety shields must be in place.
- 2. Safety and operation decals must be in place, undamaged and clean.
- 3. Hydraulic hookup must be correct and all connections tight.
- 4. All bolts and pins which attach backhoe to tractor must be in place. Check tightness of bolts and check that all pins are retained.
- 5. Tractor must be in proper operating condition.
- 6. Lubricate backhoe, see MAINTENANCE SECTION.
- 7. Controls must operate properly. See OPERATION SECTION.
- 8. Cycle all cylinders slowly to purge air from hydraulic system.
- 9. Hydraulic system oil level must be correct. Reservoir level should be 1” from top of tank.
- OPERATING DIRECTIONS
- ENGINE SPEED
- CONTROLS
- BOOM/SWING
- CROWD/BUCKET
- LEFT HAND STABILIZER
- RIGHT HAND STABILIZER
- OPERATING BACKHOE
- DUMPING BUCKET
- TRENCHING BETWEEN A BUILDING & OPEN EXCAVATORS
- SIDE SLOPE EXCAVATING OR TRENCHING
- MISCELLANEOUS
- FINISHING STRAIGHT WALLS
- BACKFILLING
- SEAT ADJUSTMENT
- PLACING THE STABILIZERS
- SWING LOCK
- BOOM LOCK
- STABILIZER LOCK
- REMOVAL FROM TRACTOR - STORAGE
- 1. Put stabilizers down and lift backhoe slightly. Rotate boom straight back.
- 2. Install swing lock pin.
- 3. Complete raise boom and lower dipperstick. Curl bucket until bottom of bucket is level with ground. Lower boom until bucket rests firmly on ground.
- 4. Remove pins which secure backhoe to tractor.
- 5. Lower front of subframe to rest on ground.
- 6. Slowly drive forward until tractor clears backhoe. Engage tractor brakes.
- 7. Lower backhoe by raising stabilizers and boom until backhoe or subframe rests on suitable blocking. Leave stabilizers touching ground.
- 8. Shut off tractor. Work handles back and forth to relieve hydraulic pressure. Disconnect hydraulic lines or pump from backhoe.
- 9. For long term storage, coat all exposed cylinder rods with grease.
- 10. Lubricate all grease fittings, stabilizer pivot pins and complete handle linkage.
- MAINTENANCE SECTION
- 1 O-RING 1
- 2 O-RING 1
- 3 VALVE BODY/RELIEF 1
- 4 PISTON 1
- 5 SPRING 1
- 6 O-RING 1
- 7 REGISTER 1
- 8 NUT, M16-1.5 1
- 9 DEFLECTOR 1
- 10 O-RING 5
- 11 CENTERING RING 5
- 12 SPRING 5
- 13 SPACER 10
- 14 SCREW 5
- 15 CAP 20
- 16 SCREW 20
- 17 SCREW 4
- 18 CIRCLIP 1
- 19 WASHER 1
- 20 BUSHING 1
- 21 SPRING 1
- 22 BALL HOLDER 1
- 23 STEEL BALL D.5 3
- 24 STEEL BALL D.7 1
- 25 CAP 1
- 26 WASHER 1
- 27 SPACER 1
- 28 SPRING 1
- 29 SPACER 1
- 30 CENTERING RING 1
- 31 O-RING 15.10 X 2.70 X 1.5 1
- 32 PLUG 4
- 33 COPPER GASKET 14 X 20 X 15 4
- 34 REGISTER 4
- 35 SPRING 4
- 36 PISTON 4
- 37 VALVE BODY/RELIEF 4
- 38 O-RING 17.17 X 1.78 4
- 39 O-RING 4
- 40 PLUG 1
- 41 O-RING 17.17 X 1.78 1
- 42 O-RING 1
- 43 PLUG 6
- 44 SPRING 6
- 45 O-RING 11.11 X 1.78 6
- 46 BODY 6
- 47 PLUG 1
- 48 LEVER 2
- 49 RUBBER BELLOWS 2
- 50 HOUSING/LEVER 2
- 51 O-RING 15.10 X 2.70 2
- 52 CENTERING RING 2
- 53 LEVER PIN 2
- 54 SCREW 8
- 55 O-RING 15.10 X 2.70 4
- 56 NUT 3
- 57 PLATE/JOYSTICK 1
- 58 SCREW 8
- 59 ASSEMBLY 2
- 60 ASSEMBLY 2
- 61 PIN 2
- 62 FLANGE 1
- 63 SCREW 6
- 64 NUT, M7 4
- 65 O-RING GASKET 2
- 66 RUBBER BELLOWS 2
- 67 SCREW 4
- 68 ARICULATION 2
- 69 NUT, M6 2
- 70 FLANGE 1
- 71 CENTERING RING 1
- 72 O-RING 15.60 X 1.78 1
- 73 PLATE/JOYSTICK 1
- 74 VALVE BLOCK 1
- 75 PLUG 1
- CYLINDER SERVICE
- CYLINDER DISASSEMBLY
- 1. Hold cylinder tube (13) stationary and pull wire ring (14) out through slot. Rotate head (6) to ease disassembly.
- 2. Pull shaft (1), with all assembled parts, out of cylinder tube.
- 3. Remove lock nut (12) from end of shaft and slide piston (8) and cylinder head (6) off shaft.
- 4. Remove piston wear ring (11), piston seal (10) and o- ring (9) from outside grooves on piston (Swing cylinders have additional steel ring between piston and nut).
- 5. Remove wiper seal (2), rod seal (3) and wear ring (7) from inside of cylinder head and o-ring (5) with backup washer (4) from groove on outside of head.
- 6. Clean all parts including cylinder tube, in a suitable cleaning solvent, then use air pressure to blow any dirt or excess solvent from all parts.
- 7. Examine all parts for wear or damage and replace, if necessary.
- CYLINDER ASSEMBLY
- 1. Place rod seal (3) into groove inside cylinder head.
- 2. Install wiper seal (2) with lip of seal facing out and flush with top of cylinder head. Install wear ring (7) inside other end of head.
- 3. Place o-ring (5) with backup washer (4) in groove on outside of head. Backup washer must be on rod side.
- 4. Remove sharp edges on outer edge of threaded end of shaft (1). Lubricate wiper seal (2) and rod seal (3) in head and carefully slide head onto shaft.
- 5. Place o-ring (9), piston seal (10) and piston wear ring (11) in grooves on outside of piston.
- 6. Slide piston onto threaded end of shaft and install lock nut (12). Swing, bucket and stabilizers cylinders; tighten lock nut (12) to 300 ft./lbs. Lift and dipperstick cylinders; tighten lock nut (12) to 375 ft./lbs. on lift cylinders.
- 7. Lubricate piston wear ring (11) and piston seal (10) on piston, o-ring (5) and backup washer (4) on head and inside of cylinder tube (13), then carefully slide piston and head into cylinder tube.
- 8. Insert wire retaining ring (14) into slot in cylinder tube (13). Apply pressure to wire ring to thread it into groove while turning cylinder head.
- CYLINDER DISASSEMBLY
- BEGINNING OF SEASON
- HYDRAULIC HOSES
- HYDRAULIC SYSTEM RESERVOIR
- BUCKET TOOTH POINTS
- TIGHTENING NUTS AND BOLTS
- LUBRICATION
- LUBRICATION CHART
- HYDRAULIC TROUBLESHOOTING
- VALVE SERVICE
- MAIN RELIEF REPLACEMENT
- 1. Use a socket to remove main relief from valve housing.
- 2. Inspect new relief to ensure seal is properly installed, and apply grease around the relief.
- 3. Ensure that pressure setting stamped on new relief matches the setting of old relief.
- 4. Install o-rings on relief.
- 5. Insert relief and torque to 60 ft./lbs.
- SPOOL SEAL INSTALLATION
- 1. Remove the mechanical joystick kit from the top of the valve and the return kit from the bottom.
- 2. Remove the old o-rings and leave spool in housing, making sure spool is in center position.
- 3. Lightly oil one seal and insert it in top of valve. Slide the seal into position in the groove in the valve body, making sure that it does not fall into the spool groove.
- 4. Lightly oil a second o-ring and insert in bottom of valve. Slide the seal into position in the groove in the valve body making sure it does not fall into the spool groove. Do not push on the spool as it may cause the first seal to come out of the ...
- 5. Reinstall the mechanical joystick kit on the top of the valve and return kit on the bottom.
- TORQUE SETTINGS
- MAIN RELIEF REPLACEMENT
- PARTS LIST
- PROPER TORQUE FOR FASTENERS
- RHINO
- LIMITED WARRANTY
- 1. LIMITED WARRANTIES
- 1.01. Rhino warrants for one year from the purchase date to the original non-commercial, governmental, or municipal purchaser (“Purchaser”) and warrants for six months to the original commercial or industrial purchaser (“Purchaser”) that the ...
- 1.02. Manufacturer will replace for the Purchaser any part or parts found, upon examination at one of its factories, to be defective under normal use and service due to defects in material or workmanship.
- 1.03. This limited warranty does not apply to any part of the goods which has been subjected to improper or abnormal use, negligence, alteration, modification, or accident, damaged due to lack of maintenance or use of wrong fuel, oil, or lubricants, ...
- 1.04. Except as provided herein, no employee, agent, Dealer, or other person is authorized to give any warranties of any nature on behalf of Manufacturer.
- 2. REMEDIES AND PROCEDURES.
- 2.01. This limited warranty is not effective unless the Purchaser returns the Registration and Warranty Form to Manufacturer within 30 days of purchase.
- 2.02. Purchaser claims must be made in writing to the Authorized Dealer (“Dealer”) from whom Purchaser purchased the goods or an approved Authorized Dealer (“Dealer”) within 30 days after Purchaser learns of the facts on which the claim is based
- 2.03. Purchaser is responsible for returning the goods in question to the Dealer.
- 2.04. If after examining the goods and/or parts in question, Manufacturer finds them to be defective under normal use and service due to defects in material or workmanship, Manufacturer will:
- (a) Repair or replace the defective goods or part(s) or
- (b) Reimburse Purchaser for the cost of the part(s) and reasonable labor charges (as determined by Manufacturer) if Purchaser paid for the repair and/or replacement prior to the final determination of applicability of the warranty by Manufacturer.
- 2.05. Purchaser is responsible for any labor charges exceeding a reasonable amount as determined by Manufacturer and for returning the goods to the Dealer, whether or not the claim is approved. Purchaser is responsible for the transportation cost for...
- 3. LIMITATION OF LIABILITY.
- 3.01. MANUFACTURER DISCLAIMS ANY EXPRESS (EXCEPT AS SET FORTH HEREIN) AND IMPLIED WARRANTIES WITH RESPECT TO THE GOODS INCLUDING, BUT NOT LIMITED TO, MERCHANTABILITY AND FITNESS FOR A PARTICULAR PURPOSE.
- 3.02. MANUFACTURER MAKES NO WARRANTY AS TO THE DESIGN, CAPABILITY, CAPACITY, OR SUITABILITY FOR USE OF THE GOODS.
- 3.03. EXCEPT AS PROVIDED HEREIN, MANUFACTURER SHALL HAVE NO LIABILITY OR RESPONSIBILITY TO PURCHASER OR ANY OTHER PERSON OR ENTITY WITH RESPECT TO ANY LIABILITY, LOSS, OR DAMAGE CAUSED OR ALLEGED TO BE CAUSED DIRECTLY OR INDIRECTLY BY THE GOODS INCLU...
- 3.04. NO ACTION ARISING OUT OF ANY CLAIMED BREACH OF THIS WARRANTY OR TRANSACTIONS UNDER THIS WARRANTY MAY BE BROUGHT MORE THAN TWO (2) YEARS AFTER THE CAUSE OF ACTION HAS OCCURRED.
- 4. MISCELLANEOUS.
- 4.01. Proper Venue for any lawsuits arising from or related to this limited warranty shall be only in Guadalupe County, Texas.
- 4.02. Manufacturer may waive compliance with any of the terms of this limited warranty, but no waiver of any terms shall be deemed to be a waiver of any other term.
- 4.03. If any provision of this limited warranty shall violate any applicable law and is held to be unenforceable, then the invalidity of such provision shall not invalidate any other provisions herein.
- 4.04. Applicable law may provide rights and benefits to purchaser in addition to those provided herein.
- TO THE OWNER/OPERATOR/DEALER