Two unit manifold installation, Operation – State TPG 150 140 NEA User Manual
Page 11
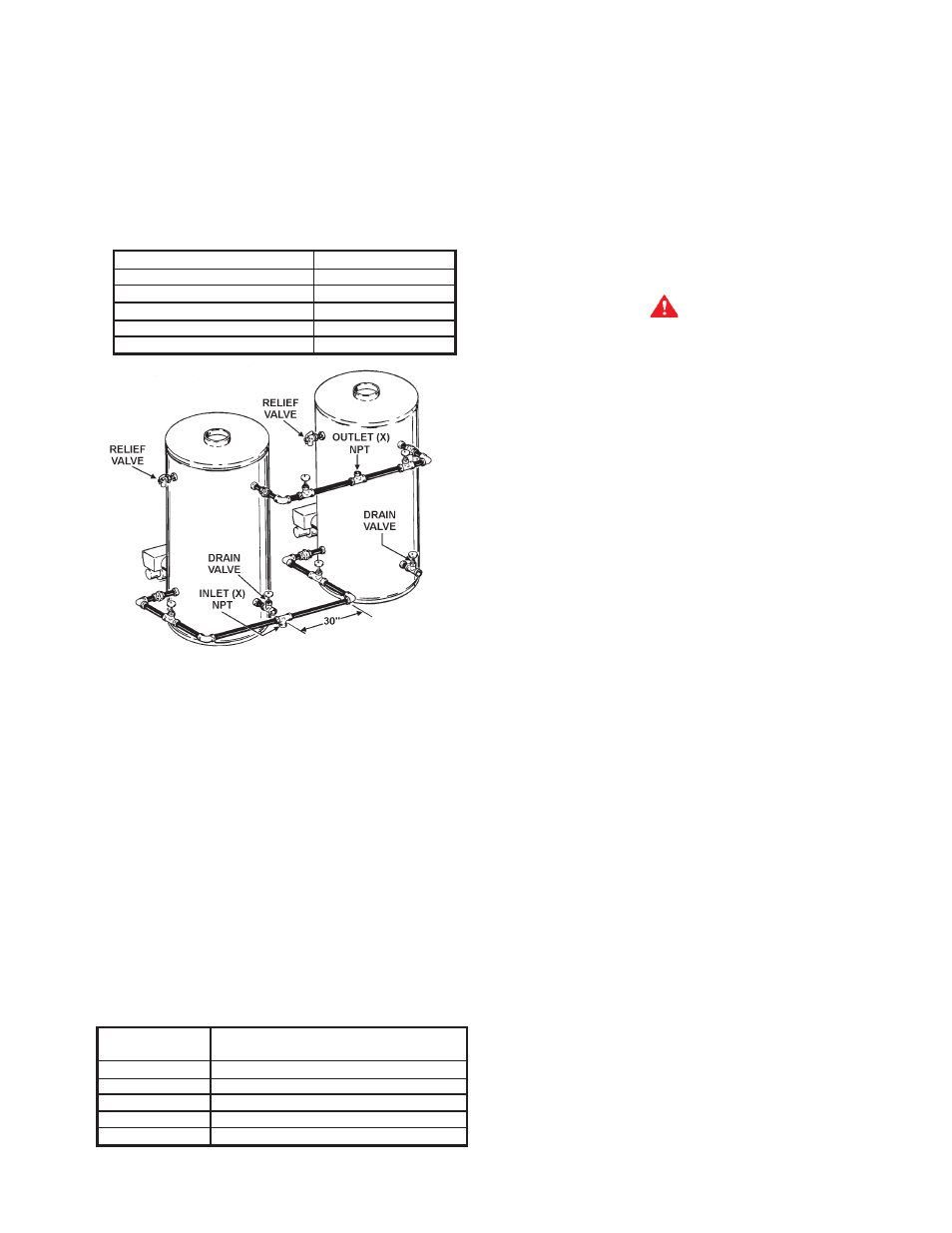
11
TWO UNIT MANIFOLD
INSTALLATION
Assure water flow balance of all units. Without this balance, the
full water heating and storage potential of the system cannot be
achieved. Otherwise, the units with the higher water flow may
have a shortened life.
Dimensions shown are for minimum space occupied by complete
assemblies. Service space in front of units must be included.
MODEL
MANIFOLD SIZE
TPX/TPG/TPO/TPD - 140
2”
TPX/TPG/TPO/TPD - 200
2 1/2”
TPX/TPG/TPO/TPD - 300
2 1/2”
TPX/TPG/TPO/TPD - 400
3”
TPX/TPG/TPO/TPD - 600
3”
OPERATION
IMPORTANT
AUTHORIZED START-UP REQUIRED. Start-up by a
State Authorized TPG/TPX/TPO/TPD Start-Up Agent is
required on the models covered in this manual. Start-up and
Operation of the units covered by this manual by other than
a State Authorized TPG/TPX/TPO/TPD Start-Up Agent will void
the warranty.
If you have not already done so, contact your local State Sales
Representative or Authorized TPG/TPX/TPO/TPD Start-Up Agent
and set-up a date for the start-up service.
The Authorized Start-Up Agent will when they come out to
start-up the unit(s) complete one of the following forms for each
unit you have and submit it to State Industries to activate your
warranty:
Start-Up
Covering Models
Form No.
09063511
TPG Models, 140 - 255 kBTUH
09063510
TPG Models, 270 - 2500 kBTUH
09063512
TPD Models, 140 - 2500 kBTUH
09063514
TPO Models, 140 - 2500 kBTUH
09063515
TPX Models, 400 - 2000 kBTUH
The time to ask any questions you may have about your unit is
when the State Authorized TPG/TPO/TPD Start-Up Agent is there.
Please do not hesitate to ask the agent any questions which you
may have regarding the units start-up, operation or maintenance.
A MAINTENANCE section is included at the rear of this manual.
Any service required should be performed by an Authorized State
Service Agent.
GENERAL
NEVER OPERATE THE HEATER WITHOUT FIRST BEING
CERTAIN IT IS FILLED WITH WATER AND A TEMPERATURE
AND PRESSURE RELIEF VALVE IS INSTALLED IN THE RELIEF
VALVE OPENING OF THE HEATER.
CAUTION
Before proceeding with the operation of the unit make sure the
water heater and system are filled with water and all air is expelled.
FILLING
1. Close the heater drain valve by turning handle clockwise.
2. Open a nearby hot water faucet to permit the air in the system
to escape.
3. Fully open the cold water inlet pipe valve allowing the heater
and piping to be filled.
4. Close the hot water faucet as water starts to flow.
5. The heater is ready to be operated.
COMBUSTION AIR REQUIREMENTS AND
SERVICE RECOMMENDATIONS
1. In order to fire correctly, the burner requires an adequate supply
of combustion air. Ventilation to the boiler room should be
provided on the basis of one square inch of free air opening
for each 1000 BTU/HR input. This excludes the requirements
for any other fired equipment in the room. The boiler room
should not become excessively hot and under no
circumstances should be under negative pressure.
2. The burner must be set up initially and serviced at regular
intervals (suggested semi-annually) by a trained serviceman
using the proper instruments. During this semi-annual service,
primary safety devices should be tested under operating
conditions. Failure to routinely test primary safety devices may
cause hazards. Suggested test procedures are listed in the
following paragraphs. Failure to maintain the correct burner
settings may result in inefficient gas consumption, premature
wear of burner components, or explosion hazard.
3. The correct test instruments are:
•
CO
2
indicator or 0
2
analyzer
•
CO indicator
•
Stack thermometer
•
Draft gauge or inclined manometer
•
U-tube manometer or calibrated 0-10” and 0-35” w.c.
pressure gauge
•
Combination volt/ammeter.