Robot calibration mode, 5. robot calibration mode – Miller Electric Auto-Axcess 450 User Manual
Page 31
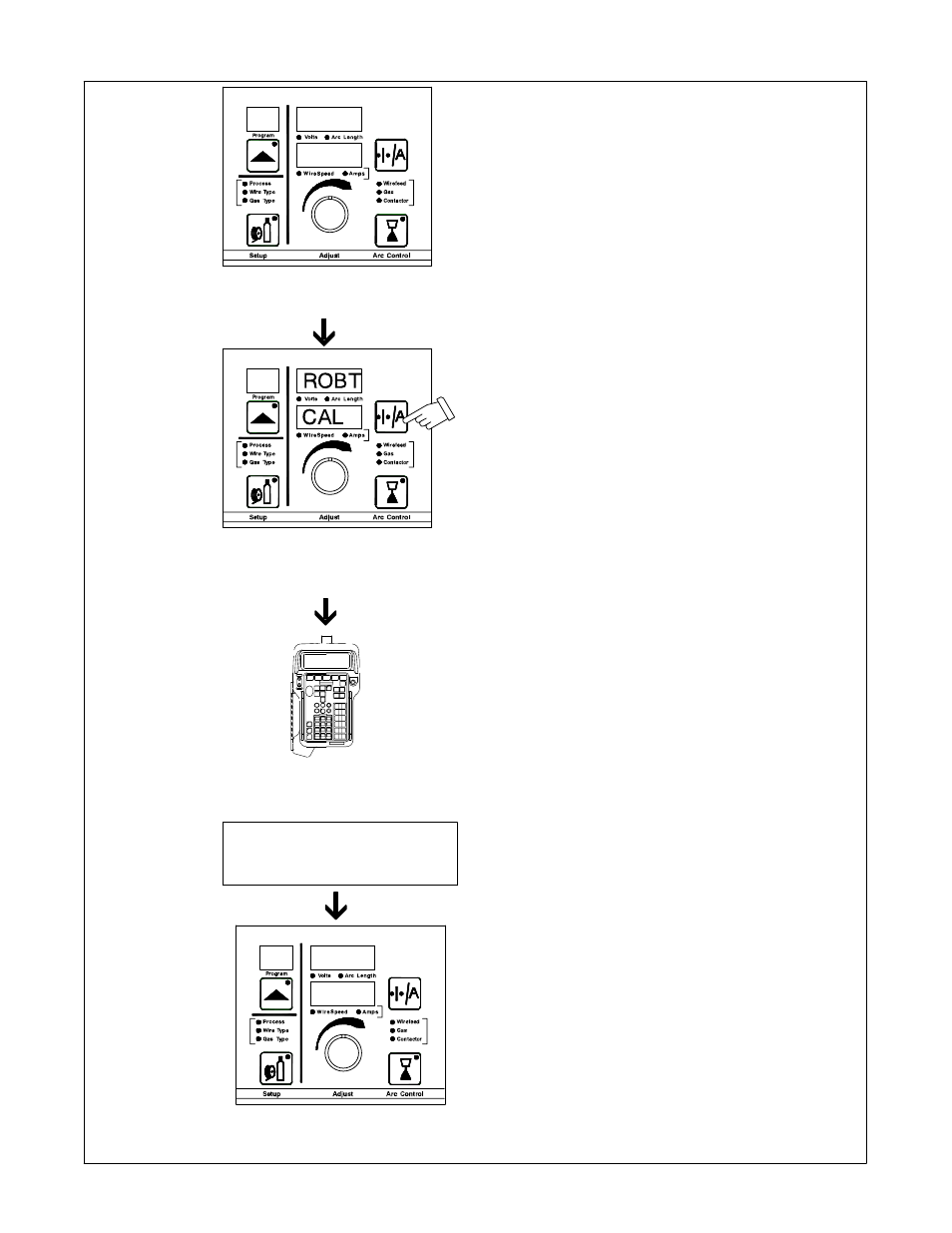
OM-210 540 Page 27
4-5.
Robot Calibration Mode
198 993
Use the robot calibration mode to
custom-calibrate the power source to
the robot command signals. This
ensures the wire speed, voltage, and
arc adjust are the same on the robot
pendant as on the power source.
.
The factory recommendation is to
perform the calibration on all
installations or code updates.
Follow this procedure if the factory
settings are not as accurate as
desired. Synchronization of the robot
and power source signals makes
installation easier and improves the
operation of the system.
.
The robot pendant must have
Weld enabled, and there can be
no start/stop crater conditions set
in the robot.
The calibration mode will execute as a
”dry run” from the operator’s
perspective. The welding power
source provides the robot with
feedback so the robot thinks a weld is
underway, yet the robot torch need not
move during the calibration.
.
If you wish to stop the calibration
procedure, turn unit input power
off and then on again.
If the calibration is performed correctly
the ROBT CAL message stops being
displayed; however, if it is performed
incorrectly, the message remains on
the display.
To start the calibration procedure over
again, turn unit input power off and
then on again following the calibration
setup steps following the calibration
setup steps.
Turn unit On. Unit displays abbreviated name of robot
detected where XXXX appears (see Table 4-2 for a list
of robot adapters that could be displayed).
To enter calibration mode while robot name appears on front panel,
press and hold wire feed/amps button until “ROBT CAL” appears on
front panel. “ROBT CAL” message will not display until after the
power-up sequence is completed (approximately 20 seconds).
Use robot pendant or other method to enter two weld schedules into the
robot. Maintain schedule 1 for at least 10 to 20 seconds minimum before
moving on to schedule 2. Maintain schedule 2 for 10 to 20 seconds
before ending the simulated weld. Schedule data is shown below:
Schedule 1
10.0 Volts
100 IPM
Schedule 2
44.0 Volts
1000 IPM
When the robot calibration mode ends, the ROBT CAL message
stops and the unit will display normal front panel information.
CIRCULER
XXXX