Faceplate turning, Spindle turning tips – Grizzly G0456 User Manual
Page 24
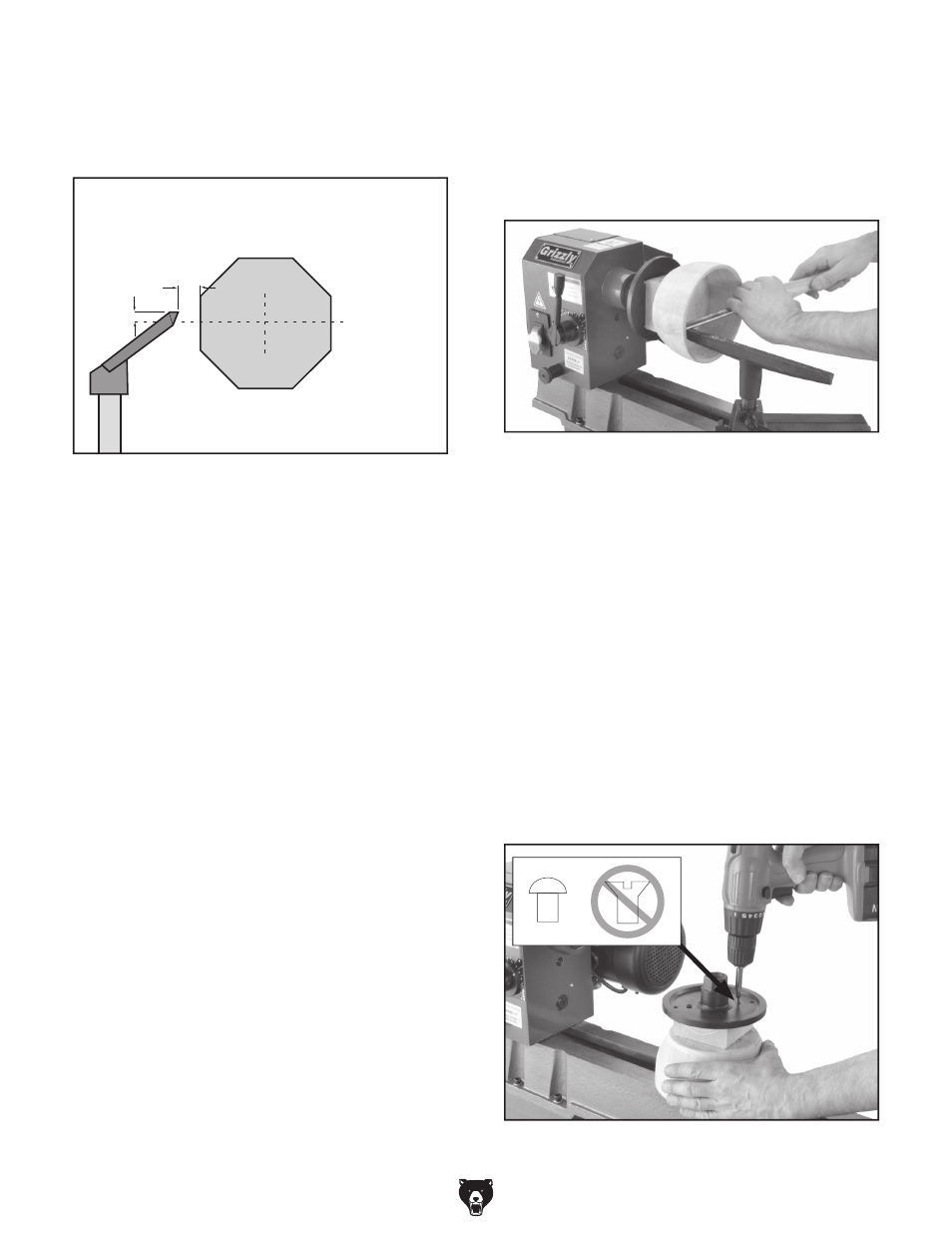
-22-
G0456 Variable Speed Wood Lathe
9. Position the tool rest approximately
1
⁄
4
" away
from the workpiece and approximately
1
⁄
8
"
above the center line, as shown in
Figure
26.
10. Test the setup by hand-turning the workpiece
to make sure there is enough clearance all
the way around before starting.
Spindle Turning Tips:
•
When turning the lathe
ON, stand to the side
of the spinning direction until the lathe reach-
es full speed and you can verify that the lathe
will not throw the workpiece.
•
Use the slowest speed when starting or stop-
ping the lathe, and when rough cutting.
•
Select the right speed for the size of workpiece
you are turning. Use slower speeds for
large workpieces (4" diameter and over); use
the middle range speeds for medium sized
workpieces (2" to 4" diameter); and use faster
speeds for small sized workpieces (under 2"
in diameter).
•
Keep the turning tool on the tool rest the
ENTIRE time that it is in contact with the
workpiece.
•
Learn the correct techniques for each tool
you will use. If you are unsure, read books or
magazines about lathe techniques and seek
training from experienced users.
���������
�����������
���������
���������
�
�
�
�
�
�
�
�
Figure 26. Tool rest set
1
⁄
8
" above the
center line and
1
⁄
4
" away from workpiece.
Figure 28. Mounting a typical faceplate to a
backing block, which is glued to the workpiece.
Figure 27. Typical faceplate turning operation.
Faceplate turning (
Figure 27) is when a workpiece
is mounted to the faceplate, which is mounted to
the headstock spindle. This type of turning is usu-
ally done with open-faced workpieces like bowls.
Faceplate Turning
To mount your workpiece to the faceplate:
1. Find the center of your workpiece in the same
manner as when spindle turning.
2. Trim corners off the workpiece with a bandsaw
to easily remove known waste.
3. Center the faceplate on the workpiece and
attach it through the faceplate holes with
screws, as shown in
Figure 28.
WARNING: USING FLAT HEAD STYLE
SCREWS INCREASES THE RISK OF
INJURY FROM THE WORKPIECE COMING
LOOSE. ONLY USE ROUND HEAD STYLE
SCREWS TO SECURE THE WORKPIECE
TO THE FACEPLATE.