Error messages, Troubleshooting guide, Problem possible cause solution – Grindmaster Insulated Decanter Brewer AMW B-Series User Manual
Page 13: Problem possible causes service check remedy, B-series page 13
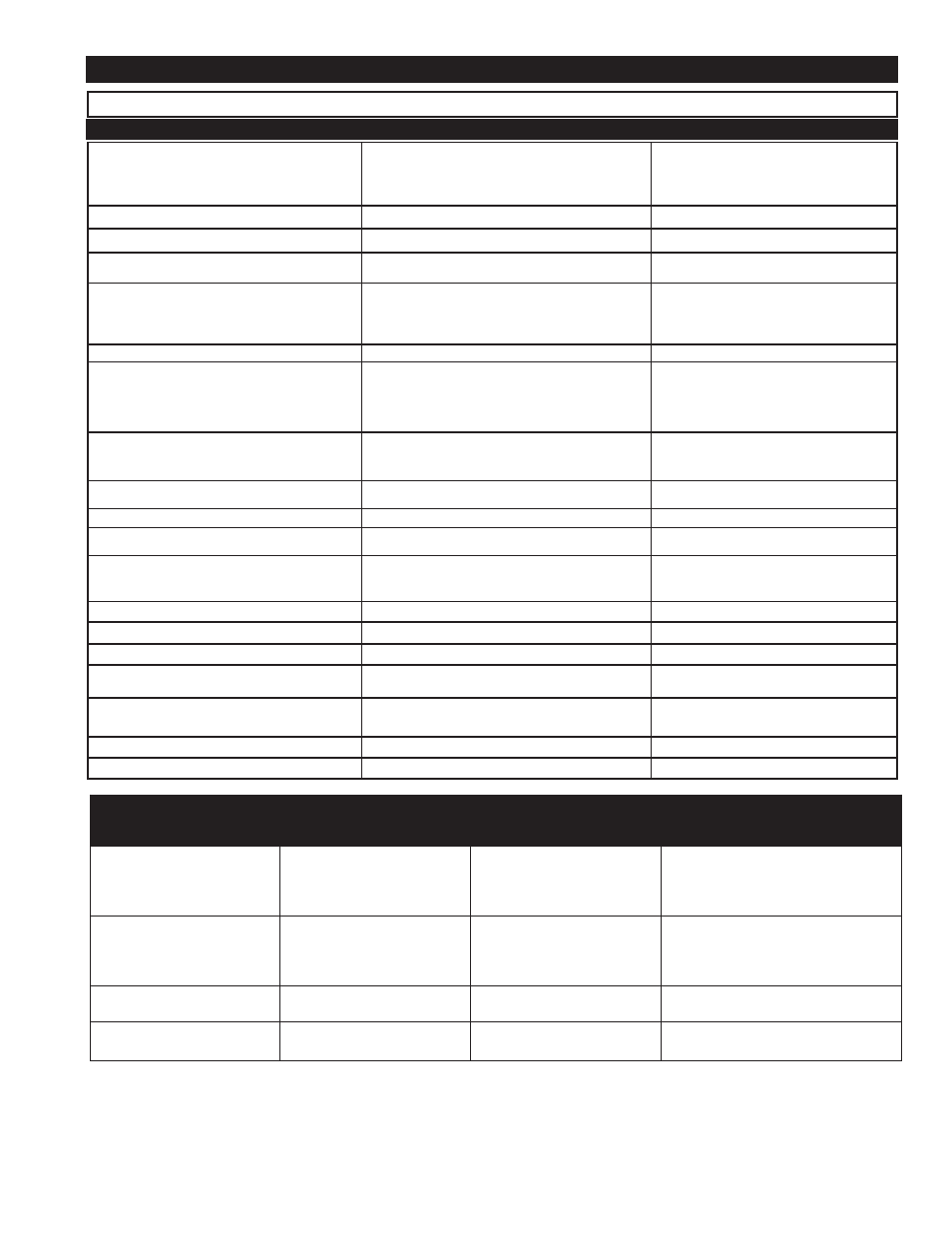
TROUBLESHOOTING GUIDE
Weak coffee
Strong coffee
Bitter coffee
Grounds in coffee
Brew basket overflowed
Unpleasant taste
Quantity of coffee dispensed
each throw is not the same
Circuit breaker trips
continuously
Control board displays “P-O”
Control board displays “ER2”
Water boiling (or steaming)
No lights are on
(including warmer lights)
Too much or not enough water in server
Spray head dripping
Hot water spigot dripping
Hot water spigot not dispensing
Warmer failure
Water solenoids not working
One indicator light will not illuminate
• Set to portion more coffee
• Readjust to finer grind
• Check spray temp; should be greater than
185°F/85°C
• Spray deflector broken or missing. Replace
• Use less coffee
• Use a coarser grind
• Use proper filter
• Position filter carefully
• Use no more than 3 1/2 oz. (100 grams) of
coffee
• Use a coarser grind
• You must dump old coffee and use fresh
new filter for each brew
• Clean, sanitize (delime)
• Delime machine
• Check hoses
• Turn screw on Dump Valve to open fully
• Check the length of time brewer runs
with watch
• Plug unit directly into outlet. Do not use
extension cord
• Designate single line for unit. Do not
use multi-outlet box
• Turn water supply on, then reset power
• Clean or replace water fill valve
• Replace if defective
• Check settings with actual temperature
• Check power at source
• Turn switch on
• Reconnect touchpad
• Readjust
• Delime unit
• Replace seal
• Delime tank
• Replace seat
• Check power source
• Replace fuse
• Replace defective heater
• Replace fuse
• Replace touchpad
• Not enough coffee used
• Grind is too coarse
• Water not hot enough
• Coffee bed has dry areas
• Too much coffee used
• Grind is too fine
• Paper filter collapsed during brewing
• Too much coffee
• Grind is too fine
• Double batching
• Water tank or brew basket needs cleaning
• Lime scale build-up
• Hose kinked
• Dump Valve not adjusted properly
• Defective timer
• Insufficient current due to
use of extension cord
• Insufficient current due to
overloaded line
• Water supply turned off
• Water fill valve on too long
• Problem with thermistor
• Temperature set too high
• Defective thermistor
• No power to brewer
• Power switch turned off
• Touch pad disconnected
• Water volume adjustment
• Lime build up in dump valve
• Faulty seal
• Tube limed up
• Defective valve seat
• Loss of power
• Bus fuse (5 Amp) on controller board is blown
• Defective warmer heater
• Bus fuse (1 Amp) on controller board is blown
• LED burned out
If you still need help, call an authorized dealer in your area or our Technical Service Department. You can reach Grindmaster Corporation’s Technical
Service Department at 800-695-4500 (USA & Canada only) or 502-425-4776 Monday-Friday, 8:00 AM - 6:00 PM EST. Please have the model and serial
number ready so that accurate information can be given.
Prior authorization must be obtained from Grindmaster Corporation’s Technical Services Department for all warranty claims.
Problem
Possible Cause
Solution
Error Messages
Problem
Possible Causes
Service Check
Remedy
ER1
• Fill valve on for over
6 min. (This occurs
during initial fill on some units –
see Initial Start-up.)
• Check system for
water leaks.
• Correct any leaks and reset controller.
ER2
• Thermistor failure or
loose connections in
thermistor circuit.
• Ensure that connector
is securely attached to controller
and that thermistor is securely
connected.
• Secure connections and reset controller. If
error reoccurs, replace thermistor.
ER3
• Thermistor is reading
out of range.
• Check tank
temperature.
• Replace thermistor.
ER4
• No heating is detected
• Verify power to heating element
and high limit operation
• Repair as needed.
B-SERIES
Page 13