Operations – Grizzly Extreme Series Jointer G9953ZX User Manual
Page 39
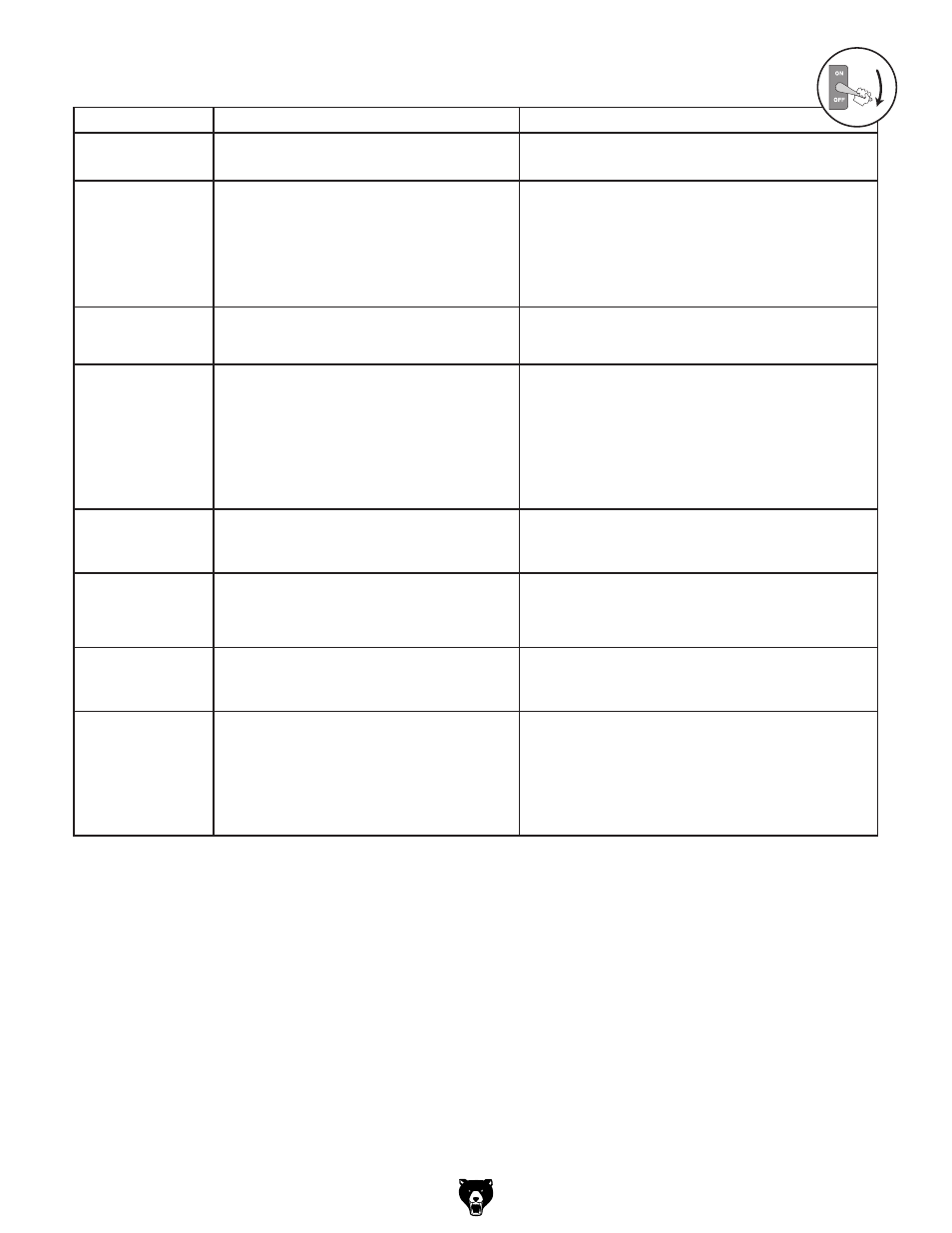
Extreme series Jointer (Mfg. since 9/11)
-37-
Operations
symptom
possible Cause
possible solution
tables are
hard to adjust.
1. table lock is engaged.
2. table stop bolts blocking movement.
1. loosen the table lock.
2. adjust table stop bolts (
page 46).
Excessive
snipe or
gouge in the
workpiece end
that is uneven
with the rest of
the cut.
1. outfeed table is set too low.
2. too much downward pressure on
workpiece end.
1. align outfeed table height with cutterhead tdC
(
page 44).
2. reduce downward pressure on that end of the
workpiece.
Workpiece
stops in the
middle of the cut.
1. outfeed table is set too high.
1. align outfeed table height with cutterhead tdC
(
page 44).
Chipping or
stuttering
patterns in
workpiece.
1. Knots or conflicting grain direction in stock.
2. Nicked or chipped knife or insert.
3. Feeding workpiece too fast.
4. depth of cut too much.
5. poor dust collection, chips not being
cleared from workpiece.
1. inspect workpiece for defects, cut with grain
(
page 26).
2. replace/rotate knives/inserts (
pages 38–39).
3. reduce feed rate.
4. reduce the depth of cut.
5. Check dust collection for proper operation;
clear blockages; reconfigure ducting system.
Fuzzy grain
left in workpiece.
1. Wood moisture too high.
2. dull knives or inserts.
1. stock moisture content should be less than
20%; sticker and let dry if necessary.
2. replace/rotate knives/inserts (
pages 38–39).
long lines or
ridges along
the length of
workpiece.
1. Nicked or chipped knife or insert.
2. loose or incorrectly installed insert.
1. replace/rotate knives/inserts (
pages 38–39).
2. remove/replace insert and install properly
(
page 38).
Wavy finish or
chatter marks.
1. Feed workpiece too fast.
2. Knives set unevenly.
1. reduce feed rate.
2. Check/adjust all knives for correct installation
and height (
page 39).
Workpiece
surface is
concave/
convex after
jointing.
1. Board not held with even pressure
during cut.
2. stock has excessive bow or warp.
3. insufficient number of passes.
1. Maintain even downward pressure on workpiece
during operation.
2. surface plane one face to use against the
jointer fence.
3. increase number of passes until the workpiece
face is flat.