Safety opera tion maintenance setup – Harbor Freight Tools 67847 User Manual
Page 17
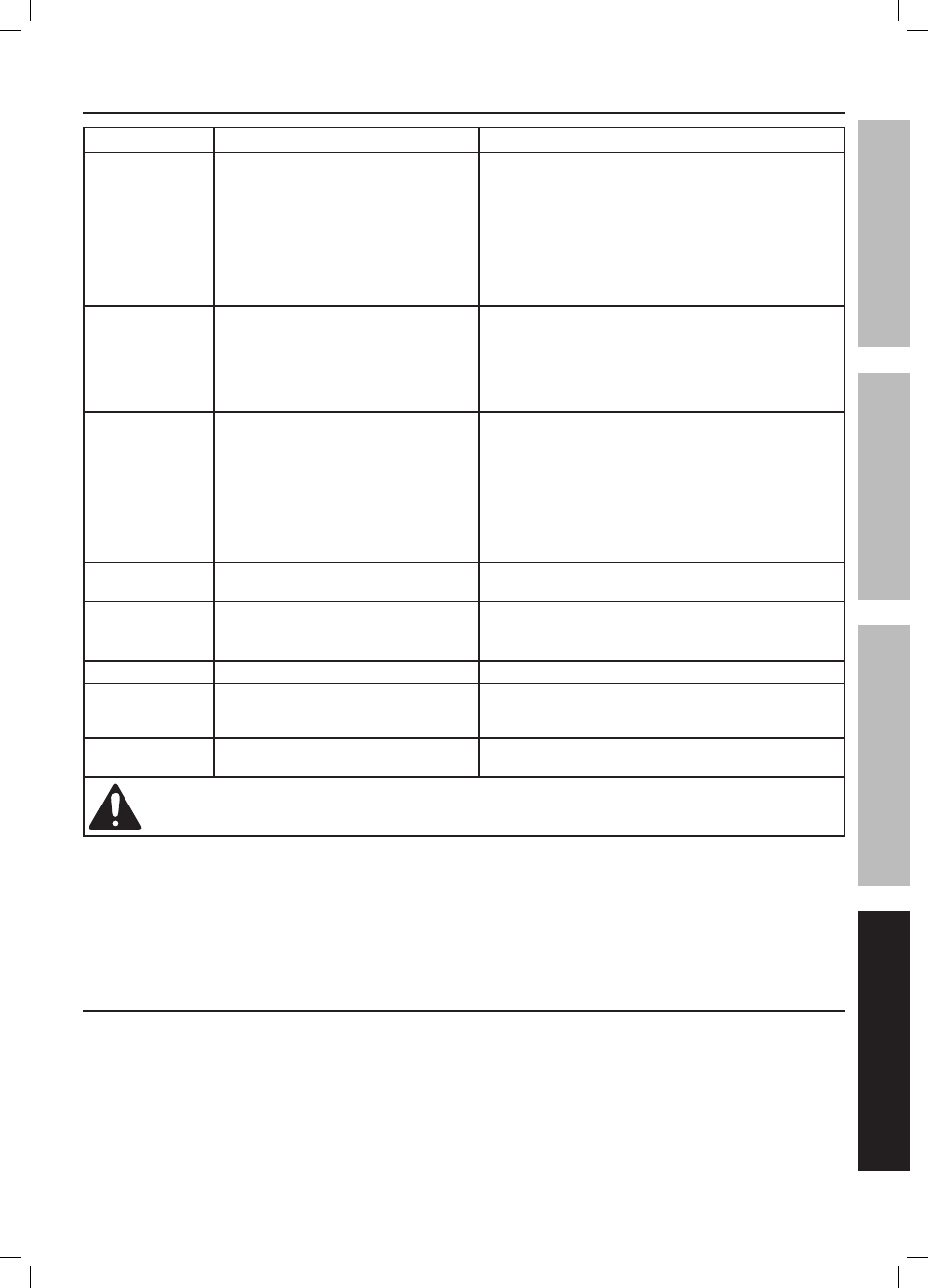
Page 17
For technical questions, please call 1-800-444-3353.
Item 67847
Problem
Possible Causes
Likely Solutions
Overheating
1. Air filters need cleaning/replacing.
2. Crankcase oil too thin or incorrect type.
3. Crankcase oil level too low.
4. Unusually dusty environment.
5. Extension cord used.
6. Unit not on level surface.
1. Check inlet and outlet filters.
Clean and/or replace as needed.
2. Drain oil and refill to proper level with recommended oil.
3. Add oil to proper level, check for leaks.
4. Clean and/or replace filters more often or
move unit to cleaner environment.
5. Eliminate extension cord.
6. Reposition unit on a level surface.
Compressor
starts and stops
excessively
1. Loose fittings.
2. Compressor not large enough for job.
1. Reduce air pressure, then check all fittings with a soap
solution for air leaks and tighten as needed.
Do not overtighten.
2. Check if accessory CFM is met by Compressor.
If Compressor doesn’t reach accessory
CFM, you need a larger Compressor.
Excessive noise
1. Crankcase overfilled with oil or oil
is incorrect thickness or type.
2. Crankcase oil level too low.
3. Loose or damaged belt guard.
4. Loose fittings.
5. Unit not on level surface.
1. Drain oil and refill to proper level with recommended oil.
2. Add oil to proper level, check for leaks.
3. Replace belt guard.
4. Reduce air pressure, then check all fittings with a soap
solution for air leaks and tighten as needed.
Do not overtighten.
5. Reposition unit on a level surface.
Moisture in
discharge air
Too much moisture in air.
Install inline air filter/dryer, and/or relocate
to less humid environment.
Oil in discharge air
1. Crankcase oil too thin or
crankcase overfilled with oil.
2. Crankcase vents clogged.
1. Drain oil and refill to proper level with recommended oil.
2. Clean Crankcase vents.
Safety Valve “pops” Safety valve needs service.
Pull on test ring of safety valve. If it still pops, replace.
Air leaks from
pump or fittings
Loose fittings.
Reduce air pressure, then check all fittings with a soap
solution for air leaks and tighten as needed.
Do not overtighten.
Air leaks from tank
Defective or rusted tank.
Have tank replaced by a qualified technician.
Drain moisture from tank daily to prevent future corrosion.
Follow all safety precautions whenever diagnosing or servicing the compressor.
Disconnect power supply before service.
Troubleshooting (cont.)
PLEASE READ THE FOLLOWING CAREFULLY
THE MANUFACTURER AND/OR DISTRIBUTOR HAS PROVIDED THE PARTS LIST AND ASSEMBLY DIAGRAM
IN THIS MANUAL AS A REFERENCE TOOL ONLY. NEITHER THE MANUFACTURER OR DISTRIBUTOR
MAKES ANY REPRESENTATION OR WARRANTY OF ANY KIND TO THE BUYER THAT HE OR SHE IS
QUALIFIED TO MAKE ANY REPAIRS TO THE PRODUCT, OR THAT HE OR SHE IS QUALIFIED TO REPLACE
ANY PARTS OF THE PRODUCT. IN FACT, THE MANUFACTURER AND/OR DISTRIBUTOR EXPRESSLY
STATES THAT ALL REPAIRS AND PARTS REPLACEMENTS SHOULD BE UNDERTAKEN BY CERTIFIED AND
LICENSED TECHNICIANS, AND NOT BY THE BUYER. THE BUYER ASSUMES ALL RISK AND LIABILITY
ARISING OUT OF HIS OR HER REPAIRS TO THE ORIGINAL PRODUCT OR REPLACEMENT PARTS
THERETO, OR ARISING OUT OF HIS OR HER INSTALLATION OF REPLACEMENT PARTS THERETO.
SAFETY
OPERA
TION
MAINTENANCE
SETUP