Troubleshooting, Safety opera tion maintenance setup – Harbor Freight Tools 67847 User Manual
Page 16
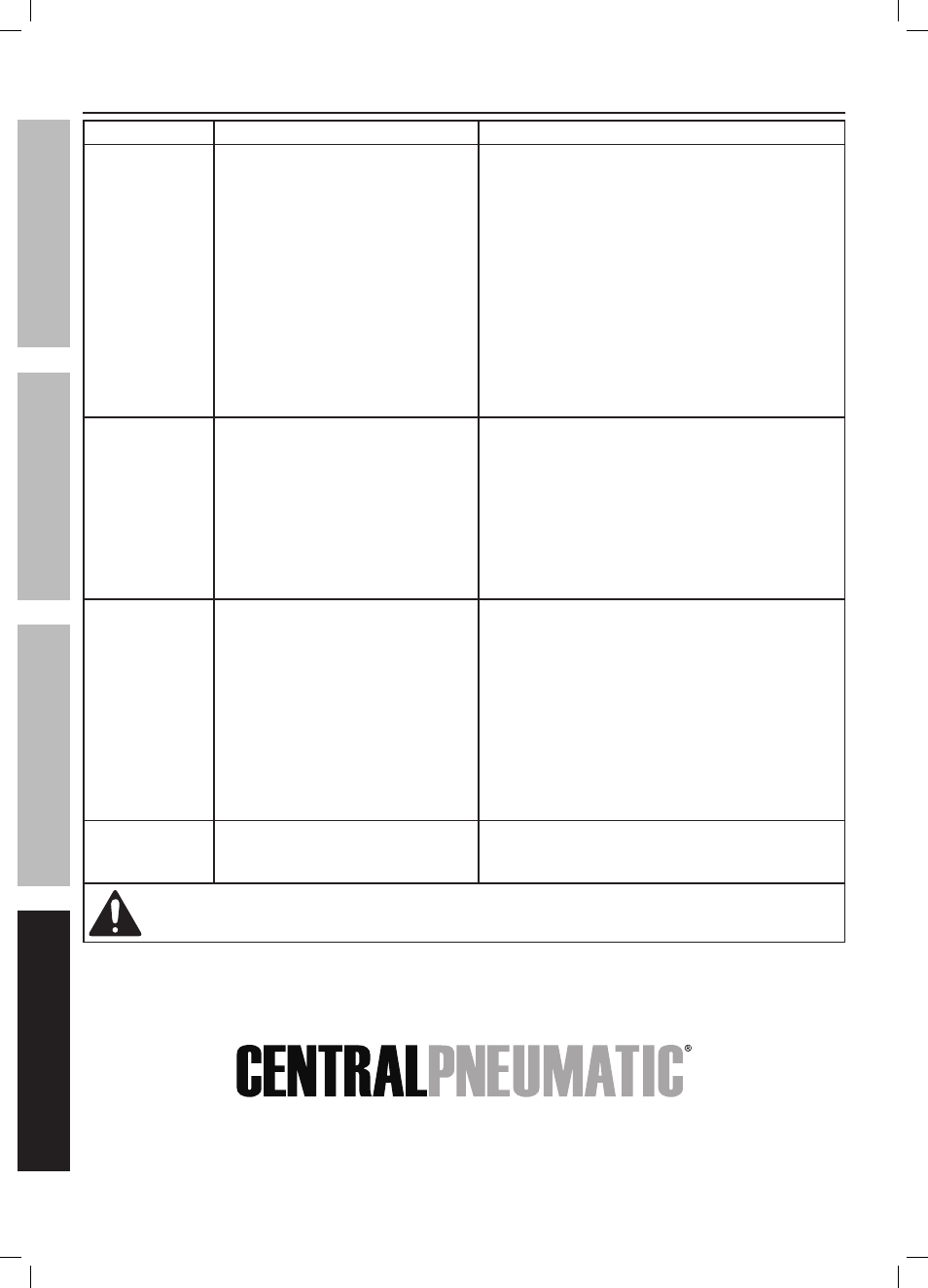
Page 16
For technical questions, please call 1-800-444-3353.
Item 67847
Troubleshooting
Problem
Possible Causes
Likely Solutions
Compressor does
not start or restart
1. Tank(s) already pressurized.
2. Power cord not plugged in properly.
3. Incorrect power supply.
4. No power at outlet.
5. Thermal overload switch tripped.
6. Building power supply circuit tripped or
blown fuse.
7. Cord wire size is too small or cord is too
long to properly power compressor.
8. Compressor needs service.
1. No problem. Compressor will start when needed.
2. Check that cord is plugged in securely.
3. Check that circuit matches compressor requirements.
4. Reset circuit breaker, or have outlet
serviced by a qualified technician.
5. Turn off Compressor and wait for it to cool down.
Press reset button. Resume operation.
6. Reset circuit or replace fuse. Check for low voltage
conditions. It may be necessary to disconnect
other electrical appliances from the circuit or
move the compressor to its own circuit.
7. Use larger diameter or shorter extension cord or
eliminate extension cord. See Recommended Wire
Gauge for Extension Cords in Safety section.
8. Have unit inspected by a qualified technician.
Compressor builds
pressure too slowly
1. Incorrect power supply.
2. Crankcase oil overfilled or oil too thick.
3. Working environment too cold.
4. Safety valve leaking.
5. Loose fittings.
1. Check that circuit matches compressor requirements.
2. Drain oil and refill to proper level with recommended oil.
3. Move compressor to a warmer location.
Check that recommended oil is in crankcase.
4. Listen for air leaking from valve.
If leaking, replace with identical valve with same rating.
DO NOT SEAL OR TAMPER WITH SAFETY VALVE.
5. Reduce air pressure, then check all fittings with
a soap solution for air leaks and tighten as needed.
Do not overtighten.
Compressor not
building enough
air pressure
1. Air filters need cleaning/replacing.
2. Check Valve needs service.
3. Compressor not large enough for job.
4. Loose fittings.
5. Hose or hose connections too narrow.
6. Crankcase oil too thick.
7. High altitude reducing air output.
1. Check inlet and outlet filters.
Clean and/or replace as needed.
2. Have technician clean or replace, as needed.
3. Check if accessory CFM is met by Compressor.
If Compressor cannot supply enough air flow (CFM),
you need a larger Compressor.
4. Reduce air pressure, then check all fittings with
a soap solution for air leaks and tighten as needed.
Do not overtighten.
5. Replace with wider hose and/or hose connections.
6. Drain oil and refill to proper level with recommended oil.
7. Higher altitudes require compressors with greater output.
High Oil
Consumption
1. Crankcase oil too thin.
2. Unit not on level surface.
3. Crankcase vent clogged.
1. Drain oil and refill to proper level with recommended oil.
2. Reposition unit on a level surface.
3. Clean Crankcase vent.
Follow all safety precautions whenever diagnosing or servicing the compressor.
Disconnect power supply before service.
SAFETY
OPERA
TION
MAINTENANCE
SETUP