Assembly, Installation, Safet y m aintenan c e parts list setup – Harbor Freight Tools 67697 User Manual
Page 7
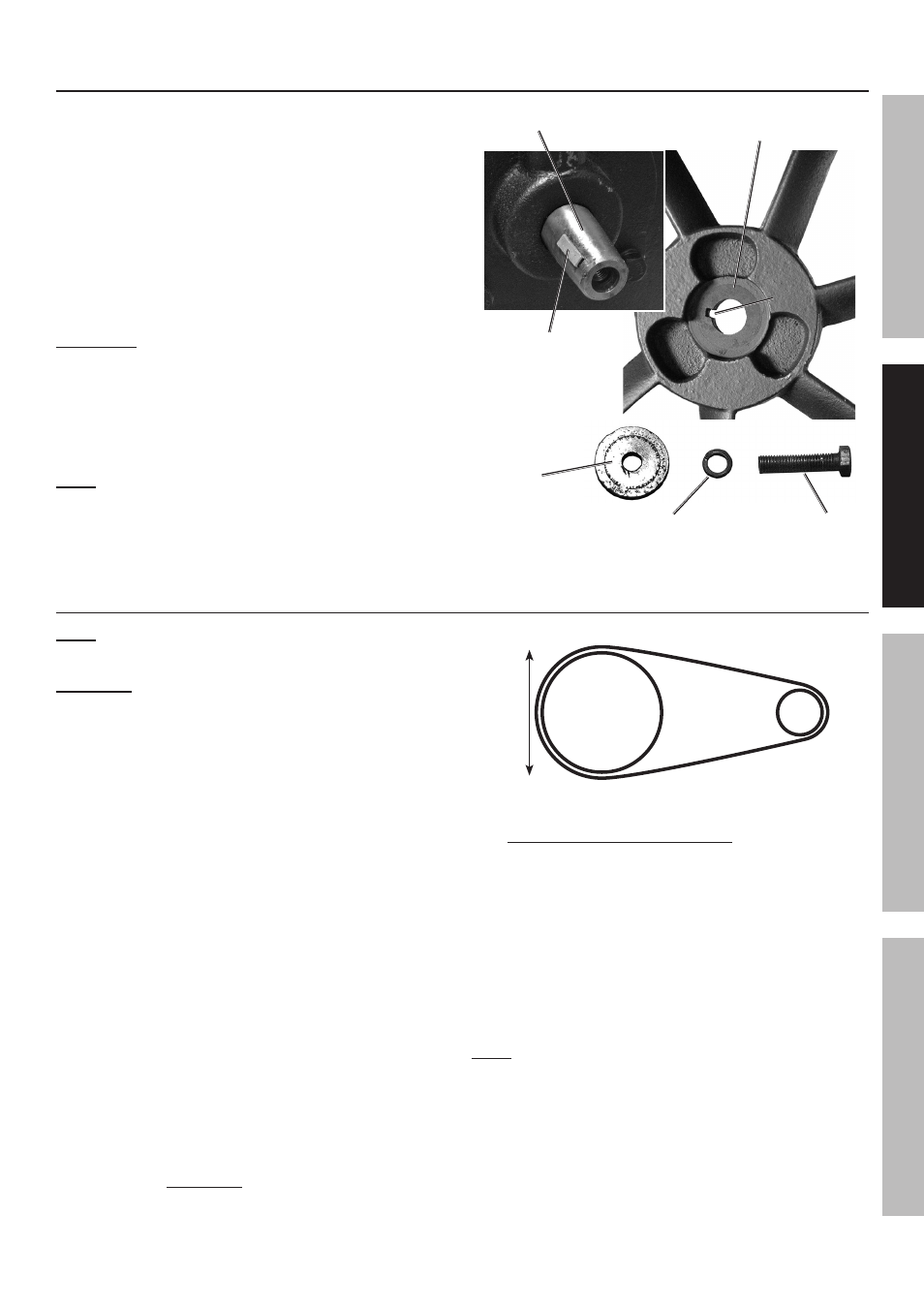
Page 7
For technical questions, please call 1-800-444-3353.
Item 67697
SAFET
y
M
AINTENAN
c
E
PARTS LIST
SETUP
Assembly
1. Place a small amount of grease in the slot at
the tapered end of the Crankshaft (51) and
insert the Woodruff Key (52) into the slot.
2. Make sure that the center hole and the
keyway on the Pump Pulley (59) are clean
and free of burrs and rough edges.
3. Apply a thin layer of grease to the hole and keyway.
With the indented side of the Pulley center facing
out, align the keyway with the Woodruff Key and
slide the Pump Pulley over the Crankshaft.
WARNING! Do not force or hammer the
Pump Pulley onto the crankshaft.
4. Slide the Pulley Washer (60) and Spring Washer
(61) onto the Bolt (62) and insert the Bolt through
Pump Pulley and thread counterclockwise into the
Crankshaft. Tighten using a wrench (not included).
Note: The Bolt has a left-hand thread. To
tighten, turn Bolt counterclockwise.
Insert Pump Pulley (59)
with this side facing out.
Woodruff Key (52)
crankshaft (51)
Spring Washer (61)
Bolt (62)
Pulley
Washer
(60)
Keyway
Figure A: Pump Pulley Assembly
Installation
Note: Depending on your level of expertise, you may wish
to have a qualified technician perform this installation.
cAUTION: Avoid damage to the Air Compressor
Pump and other equipment. The Compressor Pump
mounting platform should be flat, level, and strong
enough to support the combined weight of the Pump,
electric motor or engine, and related hardware and
equipment. It must also be capable of withstanding
the vibration and tension of the drive belt.
1. Place the Air Compressor Pump on the mounting
surface at the same level as the 3 HP motor used
to drive it. Pump positioning must incorporate
easy access to the Oil Drain Plug (48).
2. Use a motor with the appropriate size pulley to
achieve the needed Pump RPM. To calculate
the motor and motor pulley needed to power
the pump, multiply the Pump Pulley diameter
(12.5") times the pump working RPM (1050)
which equals 13,125, then divide by the motor
RPM. This will determine the motor pulley
diameter (in inches) needed to run the unit.
For example: To calculate the pulley diameter
needed for a 1725 RPM motor, multiply 12.5
by 1050, then divide by 1725, which equals
a motor pulley size of 7.6 inches. Use
the pulley size closest to this figure.
13,125
1725
= 7.6"
Motor Pulley
Pump Pulley
Pump Pulley Dia.
12.5"
(12.5" Pump Pulley Dia. x 1050 Pump RPM)
Motor RPM
13,125
=
Motor
Pulley
Dia.
Figure B: calculation for Motor Pulley
3. The Pump Pulley (59) must be in perfect alignment
with the motor pulley (not included). Misalignment
between the Motor and the Pump can cause
damage to both the motor and the compressor
pump. Use a straight edge, such as a yardstick,
to check and adjust alignment as needed.
Note: Ensure the Pump Pulley is installed
for counterclockwise rotation when facing
the pulley side of the Pump.
4. Verify that the Pump Pulley turns freely where
it overhangs the mounting surface.
5. Place a V-groove belt (not included) over
the Pump Pulley and the motor pulley.