Installation instructions, Stationary fifth wheel installation, Bracket with mounting angle – SAF-HOLLAND XL-FW484 FW33 and XA-331 LowLube Series Fifth Wheels User Manual
Page 4: Bracket for angle mounting, Figure 1c, Figure 1b (side view) figure 1a (end view)
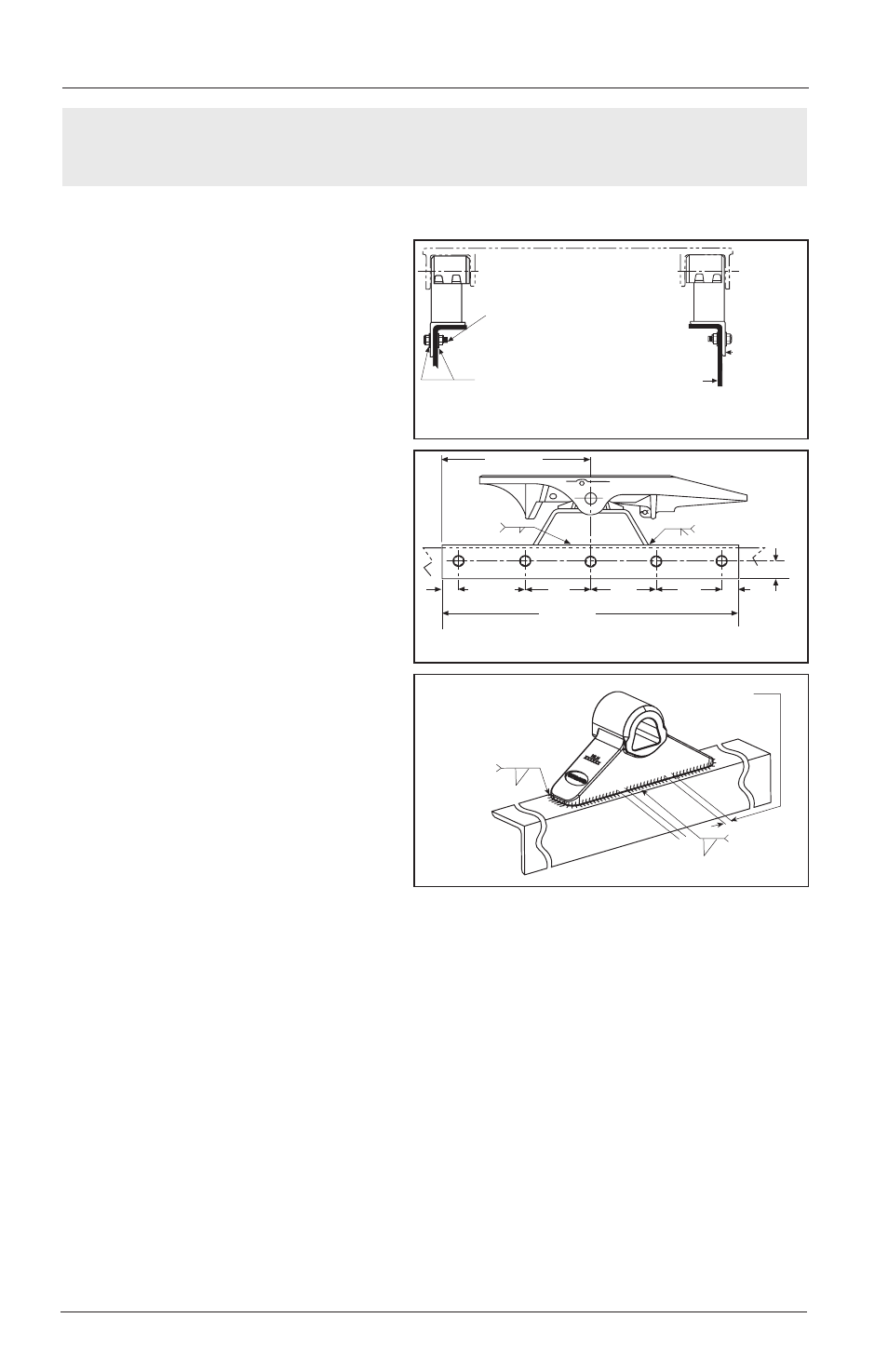
4
SAF-HOLLAND, Inc. XL-FW484 Rev E
INSTALLATION INSTRUCTIONS
continued
NOTE: The full length of the fifth wheel mounting angle should seat flush on the
truck frame to prevent flexing of mounting angle and to give uniform
weight distribution along truck frame rail.
Stationary Fifth Wheel Installation
Prior to proceeding with the installation
of the stationary fifth wheel assembly,
carefully review the “General Safety
Information” section on page 2.
Bracket with Mounting Angle
(see Figure 1A, 1B, and 1C):
1. Holland brackets with mounting
angle are provided with the bracket
welded in the center of a 36˝ long
angle with a 4˝ minimum horizontal
and 3-1/2˝ minimum vertical leg
size, and to a specific tractor frame
width. Verify that the bracket and
tractor frame width are the same.
2. In addition to the information
given in “Installation: General
Recommendations” on page 3,
follow the recommendations in
FIGURE 1.
Bracket for Angle Mounting
(see Figure 1A, 1B, and 1C):
1. Holland brackets for angle
mounting are intended to be
welded to mounting angles at the
time of installation.
2. See “Installation: General
Recommendations” on page 3, for
angle thickness and material (use
4˝ minimum horizontal and 3-1/2˝
minimum vertical leg size). The
recommended length of each mounting angle is 36˝. It is recommended that each
angle extend a minimum length of 18˝ forward of the fifth wheel pivot point, and
not less than 12˝ to the rear. If angles shorter than 36˝ are required, the special
recommendations of the tractor manufacturer should be obtained.
3. In addition to the information given in “Installation: General Recommendations,”
follow the recommendations given in FIGURES 1A, 1B, and 1C. The following
sequence is suggested for both fabricated and cast brackets:
A. Securely position the mounting angle to the tractor frame.
B. Bolt the angles to the tractor as shown in FIGURES 1A and 1B.
C. Position the brackets on the angles and verify the correct spacing to mount
the fifth wheel.
D. For fabricated brackets (a welded asssembly), weld the bracket to the mounting
angle with 1/4˝ fillet welds on both sides, and 1/2˝ groove welds on both ends,
as shown in FIGURES 1A and 1B. The welds should be continuous around the
bracket and joined at the corners.
E. For cast brackets (single piece), weld with 5/16˝ fillet weld, as shown in
FIGURE 1C. The welds must be continuous around the bracket ends.
5/8˝ diameter Grade 8 bolts
minimum size, tightening torque
to bolt manufacturer charts
Hardened steel washers or flanged
lock nuts (5/8˝ diameter Grade "C"
lock nuts).
HDN. STEEL WASHERS
TRUCK FRAME RAIL
See Table 1
for minimum
mounting
angle
thickness
18.00˝ MIN.
36.00˝ MIN.
1.00˝ MIN.
DOUBLE PASS MIN.
BOTH ENDS
8.00˝ MAX. TYP.
(50.8mm)
2.00˝
(203.2mm)
1/4˝
BOTH SIDES
8.00
˝
(203.2mm)
(203.2mm)
8.00
˝
(203.2mm)
8.00˝
(914.4mm)
2.00˝
(50.8mm)
1/2˝
(457.2 mm)
5/16˝
Both ends
continuous
GAP
1/4˝ - 1/2˝
in 4 places
5/16˝ 3 Both sides
center of
bracket
FIGURE 1C
(Cast Brackets Only)
WELDING DETAILS
FIGURE 1B (Side View)
FIGURE 1A (End View)