704u calibration procedure, Remote auto-manual switch and, Ttl option – Watson-Marlow 704U User Manual
Page 5: 12 remote auto-manual switch and ttl option
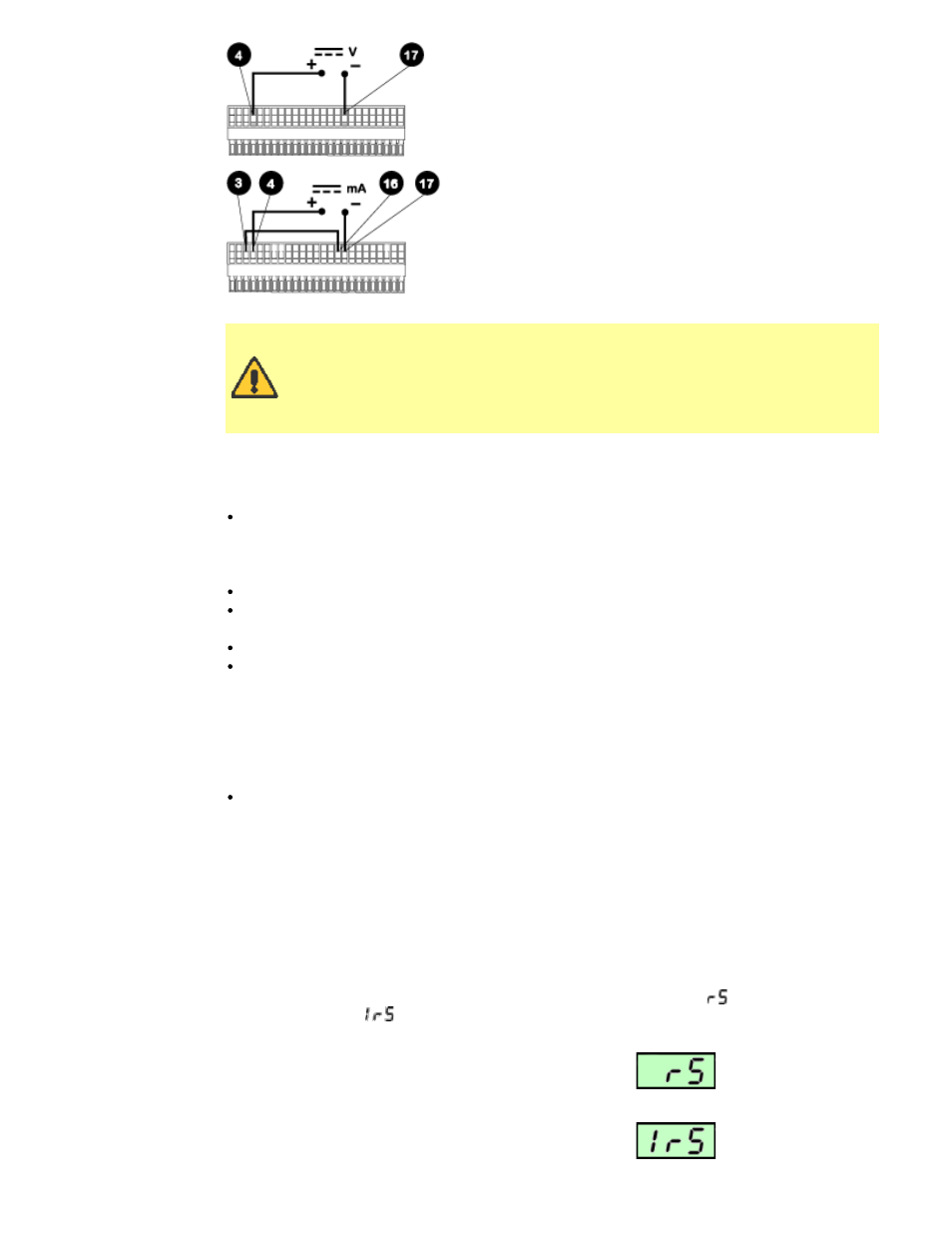
Watson-Marlow Bredel E-Manuals
http://www.watson-marlow.it/pdfs-global/m-704su-gb-03.htm[10/07/2012 14:21:14]
be used in conjunction with a DC voltmeter, (max 30V DC).
(Refer to the 25 pin terminal strip wiring detail as an
example of control circuitry.) Circuit impedance 100kOhms.
Polarity set for non-inverted response. Reverse polarity for
inverted response.
For current modes the same DC source can be used in
conjunction with a DC milliampere meter, (maximum
32mA). (See 25 pin terminal strip detail.) Circuit
impedance 250Ohms. Polarity set for non-inverted
response. Reverse polarity for inverted response.
Never apply mains voltage across any pins on the 25-pin cage clamp
connector. Up to 30V may be applied across pins 4 and 17, and 5V TTL
on pins 7 and 5, but no voltage should be applied across other pins.
Permanent damage not covered by warranty may result. Do not use the
mains power switch to control the 704U pump for a high repetition of
stop/starts. The auto-control facility should be used.
11 704U Calibration procedure
Turn the signal offset potentiometer (20 turn potentiometer) clockwise until the slider
traverse limit is reached and is signified by a clicking noise. Now turn the potentiometer
10 turns counter-clockwise. Repeat for the signal range potentiometer. This ensures
correct potentiometer set-up for calibration.
Set the process signal offset.
Turn the signal offset potentiometer clockwise to set the pump shaft speed to the
desired minimum.
Set the process signal at its upper range limit (not exceeding 30V or 32mA).
Turn the signal range potentiometer (marked "Range" on back panel) clockwise to set
the drive shaft speed to the desired maximum.
If the process signal or pump speed are set above their designated maximums the pump
will be overloaded which is signified by the signal overload indicator illuminating. The Aut
symbol will flash on the keypad. This is an indication of the limiting control and speed
levels of the drive. Reset to operate within these levels.
Repeat the procedure until pump response coincides exactly with the process signal.
12 Remote auto-manual switch and TTL option
Stop/Start
Connect remote switch between pins 7 and 15 of the 25-pin cage clamp connector.
Alternatively a TTL compatible logic input (Low 0V, High 5V) may be applied to pin 7. Low
input stops the pump, high input runs the pump. With no connection, the pump will default
to running. To invoke either remote stop or inverted remote stop, when switching power to
the pump using the pump on/off switch, press Stop and CW/CCW keys simultaneously.
The pump will indicate its current mode of switching for 2 seconds.
indicates standard
remoted switching,
indicates inverted remote switching.