Specification – Watson-Marlow 403U User Manual
Page 6
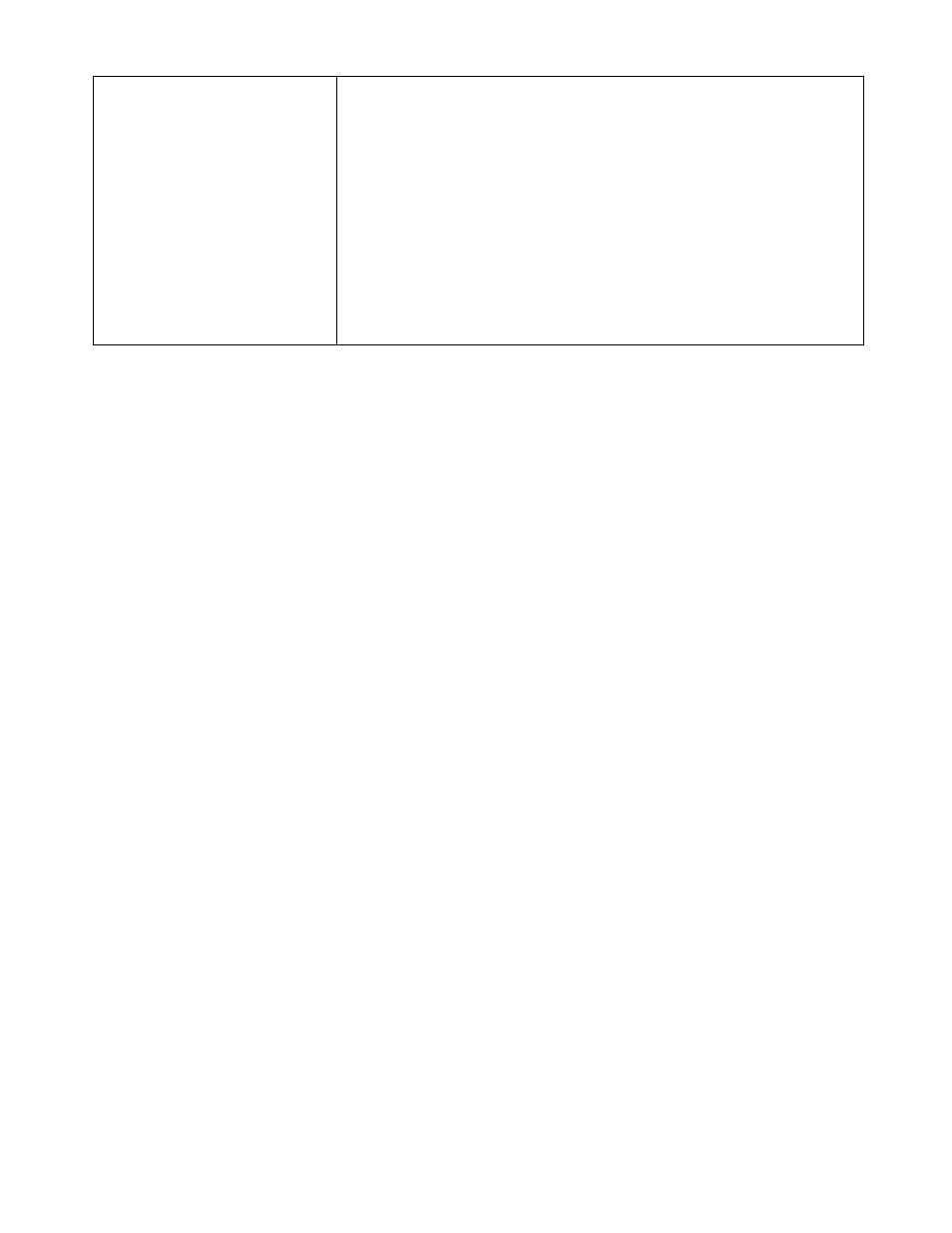
6
Specification
Maximum rotor speeds for 403U
10rpm, 50rpm
Maximum rotor speeds for 405U
200rpm
Voltage/frequency 040.****.**U 240V
50/60Hz
Voltage/frequency 040.****.**E 240V
50/60Hz
Voltage/frequency 040.****.**A 110V
50/60Hz
403U control range
20:1
405U control range
10:1
Operating temperature range
5 to 40C
Storage temperature range
-40C to 70C
Noise
<70 dBA @ 1m
Standards
IEC 335-1, EN60529 (IP21)
Machinery Directive 2006/42/EC
EMC Directive 2004/108/EC
400R1, 400L & 400L2 and 400VM2, 400VM3 & 400VM4 pumpheads
Performance against pressure
The pressure and the suction height can be increased by compressing the spring in the track occlusion pin. A smaller
gap between the rollers and track will give better performance against pressure but will reduce tube life.
Other factors that will influence tube life in peristaltic pumps are pump speed (roller impacts/minute), chemical
compatibility of the duty fluid and viscosity of the duty fluid.
It is the pressure capability of the tubing that limits the operating pressure of the pump. The maximum pressure you
can obtain is dependent on the wall thickness, tube bore and hardness of the tubing. Normally the maximum pressure
is 2 bar.
Key Safety Information
When fitting a new tube in the pumphead
Ensure that there is no pressure, liquid or gas in the pipeline.
Disconnect the pump from the mains to prevent the pump from starting unexpectedly.
Always replace any protective guard after tube changeover.
If a tube failure has occurred, ensure that any fluid in the pumphead has been allowed to drain to a safe area
Ensure that protective clothing and eye protection is worn if aggressive fluids are being pumped.
400R1 pumphead set-up
The 400R1 pumphead is designed to accept 1.6mm wall standard laboratory tubing up to 6.4mm bore. Care should
be taken to establish the normal tube life experienced within a set of operating parameters. Subsequent tubing
replacement should be scheduled within the normal expected life of a tube. This will avoid unnecessary tube failure
and unplanned pump maintenance.
Tube loading (Pictures 1-9)
Remove the transparent guard.
Release the track by disengaging the track occlusion pin.
Before tube loading, make sure that enough suction and delivery tubing is available to connect into the remaining
pipeline or to reach the suction reservoir and delivery point.
Locate the tubing into the suction side tube clamp. Feed the tubing in around the rotor, maintaining reasonable
tube tension so that the tube sits around the rotor, and locate into the delivery side tube clamp. Make sure that
there are no twists or kinks in the tubing after loading as this will adversely affect tube life.
Ensure the tube is lined up centrally in the track correctly secured at each clamp.
Re-position the track over the rotor and fix by slotting the track occlusion pin back into the track slot.
Re-attach the transparent guard.
Compressing the spring on the track occlusion pin (picture 10) will increase the suction height and performance
against back pressure.