Operation – Smithco Spray Star 1010 Aug 2013 Operator Manual User Manual
Page 15
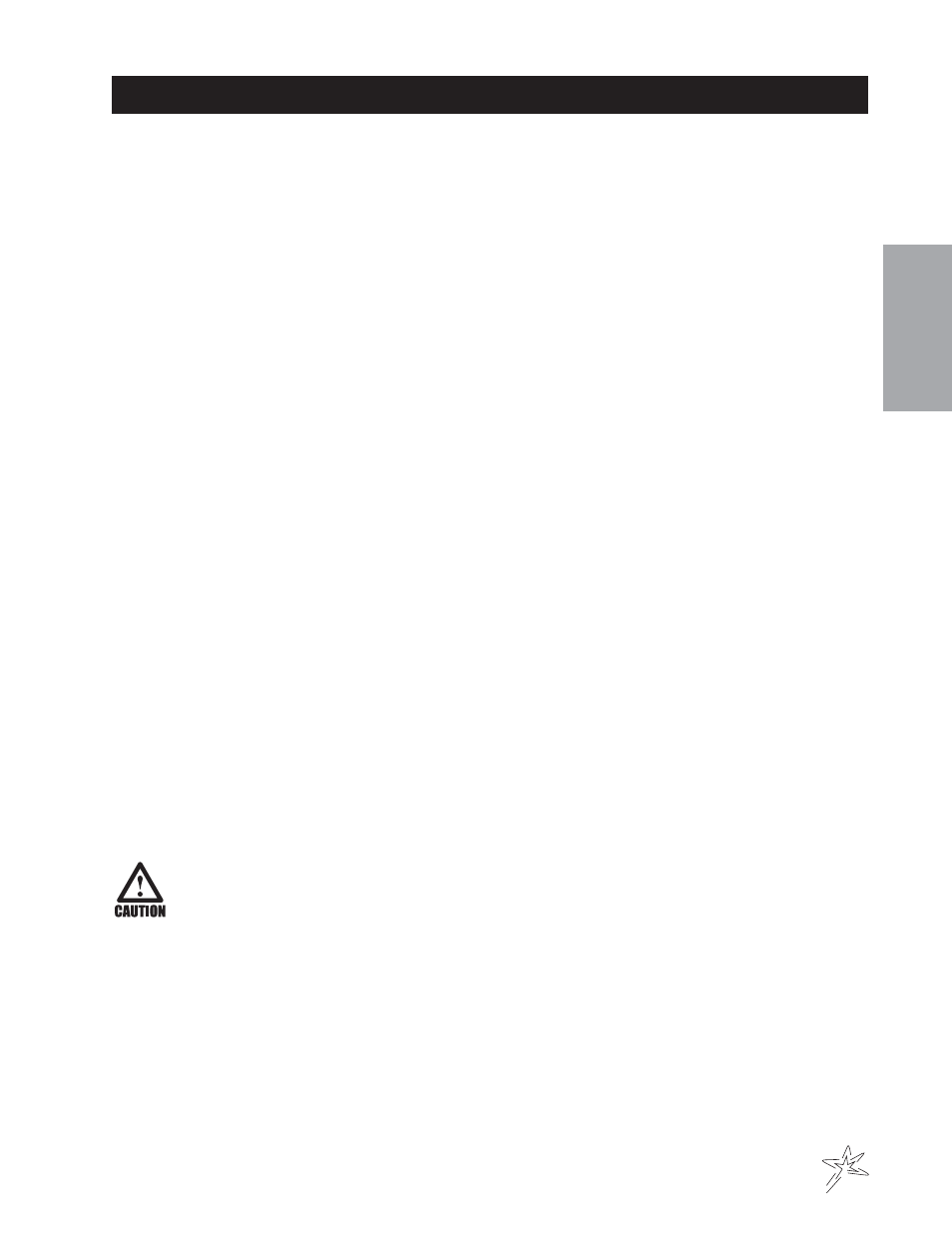
13
Operation
PARTS MANUALS AVAILABLE ONLINE AT smithco.com
OPERATION
If your Spray Star is fitted with a hose reel, there is a third ball valve on the discharge system to supply material
to the hose reel.
The Quadrajet agitation system operates with four venturi jets in the tank bottom. These jets have replaceable
orifice discs which discharge the following amounts of spay material.
Input to
Input to
Agitator
Agitator
Agitator
Agitator
Nozzle
Agitator
Agitator
Pressure Pressure
Output
Output
Diameter
in gpm
in L/min
in psi
in bar
in gpm
in L/min
1
/
8
"
1.9
7.2
25
1.7
6.3
23.8
1
/
8
"
2.7
10.2
50
3.4
10.0
37.9
1
/
8
"
3.8
14.4
100
6.9
15.0
56.8
5
/
32
"
2.8
10.6
25
1.7
7.6
28.8
5
/
32
"
4.2
15.9
50
3.4
12.2
46.2
5
/
32
"
5.5
20.8
100
6.9
17.5
66.2
3
/
16
"
3.6
13.6
25
1.7
9.1
34.4
3
/
16
"
5.6
21.2
50
33.4
14.3
54.1
3
/
16
"
7.9
29.9
100
6.9
18.7
70.8
You can change orifice disc sizes to enhance spray system performance. Smaller discs reduce amount of agita-
tion (desirable in some foaming materials) and make more dischargeable liquid available for nozzles. Larger (or
none) discs increase amount of agitation and make less dischargeable liquid available for nozzles.
SPRAY OPERATION (After Proper Setup and Calibration)
1. Add
1
/
2
the amount of water required for the spray operation to tank using air gap filler.
2. Start engine, set engine speed below 2000 RPM, and engage pump after taking all previously described
safety and operation precautions.
3. Open agitator valve.
4. Add chemicals (taking all precautions described in this manual and by the chemical manufacturer).
a. Liquids may be poured directly into tank.
b. Wettable powder chemicals must be pre-mixed with water in a container to form a slurry. The mixture
is then added to the tank through the fillwell strainer.
c. Chemical in soluble packs are place into the fillwell strainer basket and dissolved by adding water
through the basket.
The balance of the water required for the spray operation is added to the tank through the fillwell strainer,
using the air gap filler. This will wash any undissolved chemical into the tank.
5. Transport to sprayer site with and agitator operating.
6. Set Engine speed between 2000-3200 RPM.
7. (Optional) Engage ground speed control.
8. Obtain desired spraying speed before activating spray with switches on spray control console.
Review the capacity of nozzles being used. Total capacity of all nozzles plus agitation
system must not exceed pumping system capabilities refer to Spraying Procedure section of
this manual. FLUSH PUMP AFTER USE
Shut-Off 20GPM 40GPM 60GPM 80GPM 100GPM
120psi
100psi
80psi
60psi
30psi
10psi
100psi
95psi
76psi
52psi
26psi
5psi
80psi
75psi
62psi
45psi
21psi
-
60psi
55psi
40psi
25psi
5psi
-
To determine the correct performance data for your application, first shut off all flow on discharge side of pump and
detemine the shut-off pressure at the pump. Use this Shut-Off pressure to determine which line of data applies.