Straight line cutting – Mathey Dearman MiniMag XM User Manual
Page 10
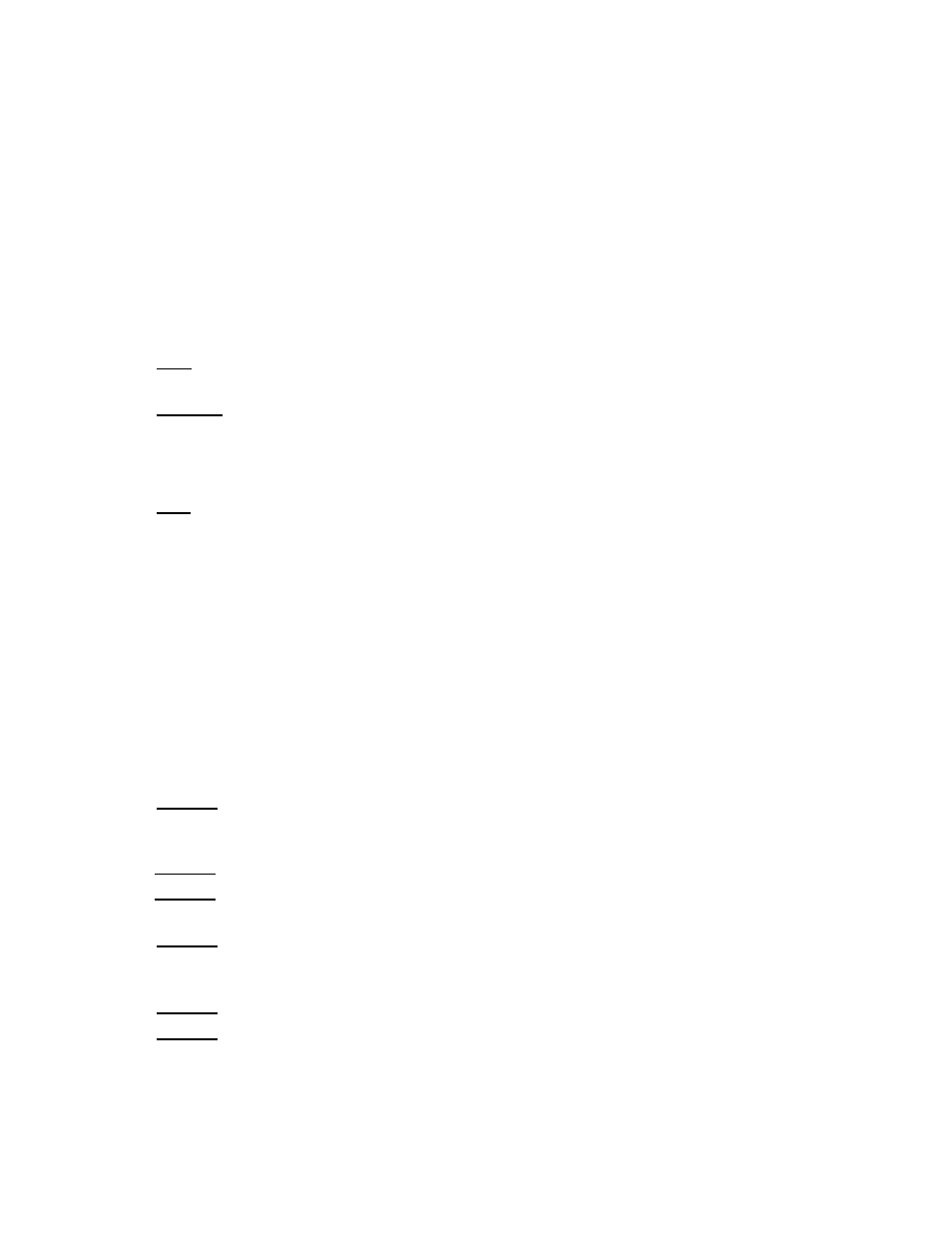
other debris and remove it with the Brush provided in the Storage Box.
5. Install Sliding Support (7) on to Torch Arm (B) until it is at the middle of the Torch Arm (10) flush
with the end of the Torch Arm.
6. Use a 3/16‐inch Allen Wrench furnished with the MiniMag XM to tighten the Setscrew (C) in the
Sliding Support (7).
6.
Install the Torch Holder Assembly (6) on Sliding Support (7) and turn the Ratchet Handle (M)
clockwise, until the Torch Holder Assembly is held in a fixed position on the Torch Support
7.
Make certain the Unit Directional Control Switch (F) is in center or OFF position.
8.
Make sure the Unit Speed Control Rheostat (G) is in the "0" position.
9.
Connect the Cord with Connector Plug (J) to the Female Connector (20) on the Base Unit.
10.
Connect Power Cord (K) of the Motor Control Box into 110vac 50 or 60 hertz power source.
Note: The MiniMag XM can be used with a 230–110 VAC Step‐down Transformer (23) for 230vac
operation.
Warning: The MiniMag XM Motor Control Box is not designed for use with a 110‐vdc Power
Source.
11. Move the FORWARD‐STOP‐REVERSE Switch (F) in the direction you want the MiniMag XM to
travel.
Note: Before changing Drive Motor Direction the Unit Directional Control Switch (F) should always
be moved to the STOP position for at least one full second. (G) Rotate the Unit Speed Control
Rheostat to the desired position. If this is the first time that the MiniMag XM is used, rotate the
Unit Speed Control Rheostat to the Number 4 position. Adjust the Rheostat until the desired
speed is achieved.
12. Once the desired speed is achieved move the Unit Directional Control Switch (F) to the STOP or
center position.
13. The machine is now ready for operation.
Straight line Cutting
1.
Make sure the plate or pipe surface is free from obstruction, slag and other debris.
2.
Set the MiniMag XM on the pipe or plate and move the machine in a twisting motion until all
Wheels are in full contact with the pipe or plate.
Warning: When cutting pipe with a welded seam running parallel to the pipe axis, place the
welded seam between the 11:00 and 1:00 o’clock
position. Place the MiniMag XM on the pipe so it
will cross the welded seam just prior to finishing the cut.
Warning: The MiniMag XM is not designed for use on non‐magnetic or wrapped pipes or plate.
Warning: The MiniMag XM is not designed for use on spiral welded pipe as it will lose contact
with the pipe surface.
Warning: If at all possible start the cutting operation with the Machine between the 3:00 through
the 9:00 O’clock position on the pipe or plate. The piece being cut off may separate the MiniMag
XM from the surface of the material causing damage to the Machine.
Warning: Never place the Machine on the piece of pipe or plate that is being cut off.
Warning: The MiniMag XM will lose contact with the surface of the pipe or plate if it does not
contact the weld at a 90‐degree angle. The weld should not be over 3/16 of an inch high.
3.
Attach the Safety Snaps (18) to the MiniMag XM at points (P & Q).
4.
Attach the Safety Cable (18) provided with the MiniMag XM to the Safety Snaps (17).