Herrmidifier Load Calculator User Manual
Page 15
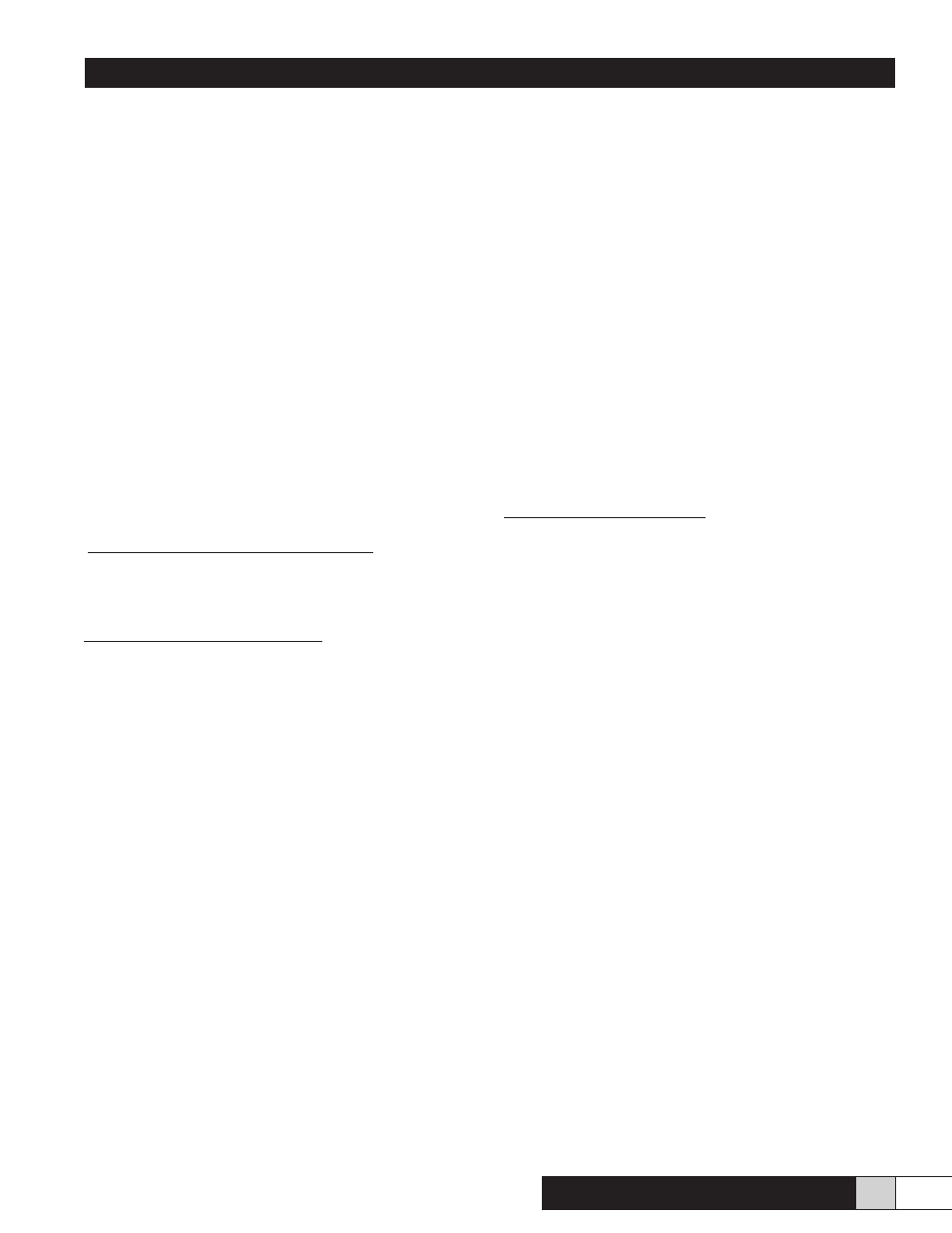
L o a d C a l c u l a t i o n G u i d e
L o a d C a l c u l a t i o n G u i d e
15
w w w. h e r r m i d i f i e r- h v a c . c o m
Air temperature drop across the coils can be considerably
less than 15°F and must be known to accurately calculate
the humidification demand load for cooling. Also, the CFM
air flow across the coils is high and combined with the small
temperature drop, across the coils, will result in less mois-
ture being condensed out of the air onto the coils. Generally,
its safe to figure the exit R.H. at about 90%-95% R.H. The
“OFF” cycle for defrosting is a definite and planned period
during each 24 hours and is usually expressed as “Runs 16
hours out of 24.” You should NOT correct for the “OFF” cycle
in this case since the equipment runs continuously for 16
hours and will remove moisture that must be replaced, con-
tinuously.
Example:
Design Conditions: 34°F 95% R.H.
Cooling Capacity: 30 Tons
24,000 CFM across coils
10°F Air temperature drop
Room Air:
34°F 95% R.H. = 2.29x.95(%) = 2.18 gr./CF
-Exit Air:
24°F 90% R.H. = 1.50x.90(%) = 1.35 gr./CF
Moisture removed by Cooling = .83 gr./CF
Using humidification demand load formula:
24,000 CFM x 60 min./hr.x.83 gr./CF = 170 lbs/hr. water
7,000 gr./lb.
Therefore, a humidification system designed to handle this
demand must be able to supply a maximum of 170 lbs. water
per hour. The above factors are for illustration. The individual
factors must be determined for each special application. It is
helpful to consult a humidification expert who, no doubt, has
had prior experience with these special applications.
Herrmidifier has had extensive experience in all fields of low
temperature humidification, including cold storage as low as
34°F. For a list of previous installations or sizing and recom-
mendations for your own application consult your Herrmidi-
fier Representative.
The Herrmidifier dual-pneumatic atomizing system is partic-
ularly adaptable to cold storage humidification applications.
It has been used successfully to maintain levels as high as
95% R.H. at temperatures as low as 34°F without wetting of
floors.
Product Load
Many products made of or containing hygroscopic materials
will absorb or give up moisture and as such will need to be
conditioned to the proper Regain for shipment. This load only
occurs as a viable factor in the overall MAXIMUM HUMIDI-
FICATION DEMAND LOAD when large amounts of products
are being conditioned rapidly, such as textiles. The proce-
dure for determining the product load is relatively simple if
you observe the following steps.
Step 1. Determine the MAXIMUM change in Regain of the
material during processing, using Table I-C to determine the
Regain of the material before and after conditioning and find
their difference.
Example:
A plant processing 40 tons/hour of product received at 4%
Regain and shipped at 5% Regain will need to add 1% gain
as follows:
Shipping Regain = 5.0%
-Regain when received = 4.0%
Gain = 1.0%
Step 2. Determine the MAXIMUM amount of product, in
pounds, to be processed in any one hour.
Example:
40 tons/hr. x 2,000 lbs/ton = 80,000 lbs. hr.
Step 3. Calculate the MAXIMUM PRODUCT LOAD by tak-
ing the maximum amount of product processed per hour
times the gain needed.
Example:
80,000 lbs./hr.x.01 (% gain) = 800 lbs. water/hour
Therefore, any humidification system designed for this ap-
plication will have to have a maximum capacity of 800 lbs.
water per hr. IN ADDITION to any heating or cooling load.