Introduction, Storage, Maintenance – Flowserve CE Series Automax CENTURA User Manual
Page 2: Installation
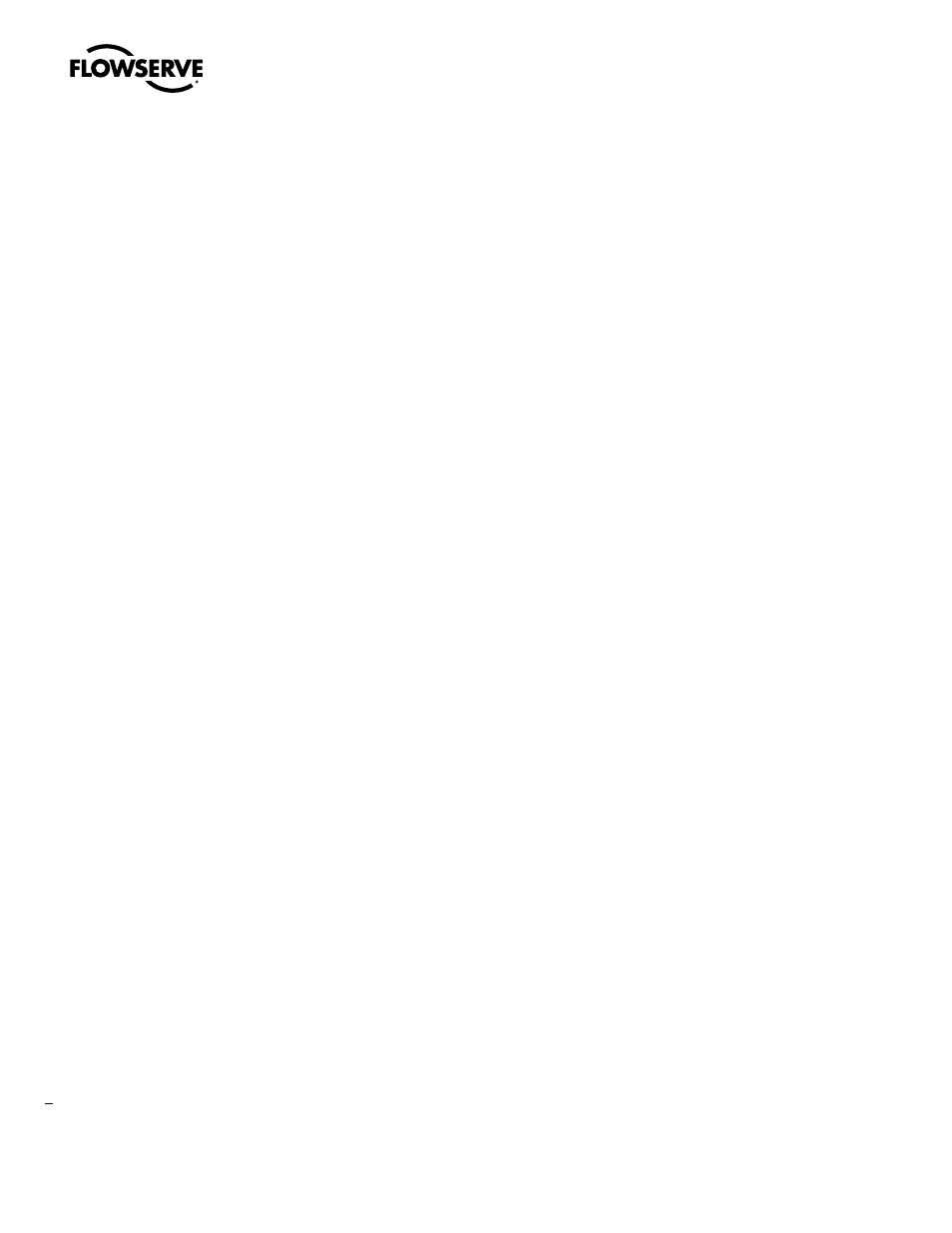
Automax CENTURA™ CE Series FCD AXENIM0037-01 – 12/05
2
Introduction
The Centura electric actuator is a rotary valve actuator with output
torques from 250 to 1,500 in-lbs. It has been designed for NEMA 4, 4X,
7, 9 and can come with a 4-20 mA card for modulating service.
Storage
For short and long term storage refer to short and long term storage
conditions CE Actuator.
Maintenance
Centura Series actuators contain a permanently lubricated, precision
cut, heat treated gear train for long, reliable cycle life. There is no need
to change gear train grease; however, should it become necessary to
refill, use a multi-purpose grease such as DuBois MPG-2.
Permanent split capacitor gearmotors have been equipped with thermal
protectors. After many operations, especially in warm environments,
the motor will heat up. To guard the motor against overheating, the
thermal cut-out blocks power to the motor and maintains this state
until the motor’s temperature drops to a satisfactory level. This thermal
protection means that the actuator will not move when overheated.
Consideration must be given to the duty cycle requirements of the
actuator.
When replacing the cover, the machined joints must be clean and clear
of any obstructions. The integrity of the explosion-proof rating depends
on the care of these joints.
Installation
1. This section of the instruction sheet applies to the on-off units. For
instructions on Modulating units, please see the ESP3 Electronic
Servo Positioner Instructions.
2. Manually open and close valve to ensure freeness of operation.
a
Caution: To prevent ignition of hazardous atmospheres,
keep unit tight while circuits are alive. Disconnect supply
circuit before opening.
3. Be sure valve and Automax actuator rotate in the same direction
and are in the same position (i.e., valve closed, actuator closed). If
not sure, electrically operate the actuator to determine its operating
range, taking note of any explosion safety requirement. The electric
actuators are factory set for 90 degree operation.
a
Caution: Use heavy duty brake option ‘K’ for rubber lined
butterfly valves & dampers or applications that may back
drive the unit.
4. Mount Automax actuator to valve with Automax provided mounting
hardware to ensure proper alignment. Use mounting hardware
that has 11/2 times bolt length engagement. (Do not use the manual
override to align actuator shaft to valve shaft, as this could drive the
actuator out of its operating range).
notE: Some valves have manual stops; remove if appropriate or
set actuator to operate within those travel stops).
5. Care should be taken to align valve stem properly with Automax
actuator output shaft (misalignment will cause premature failure of
assembly).
6. To connect power to terminal strip of actuator, remove the cover
and locate the terminal wiring schematic inside the cover.
7. Connect power to terminal strip according to schematic diagram
(power should be fused with a 5 amp slow-blow fuse). The actuator
should be wired and grounded in accordance with Local and
National Electrical Codes.
a
Caution: Consult factory when wiring multiple actuators
in series or parallel. Serious damage may result. User must
isolate unused winding.
8. Before replacing cover, actuate valve and check to see if it opens
and closes to preferred positions. If valve does not perform
correctly, adjust cams to set actuator travel properly.
9. Drive actuator to desired open position. The cams are adjusted in
two ways. Simply depress the splined “Quick-Set” cam against the
spring and rotate to desired location. Or, for very precise applica-
tions, turn the screw inside the cam to move the tip into the leaf of
the micro switch.
10. To adjust closed position, repeat step 9 with actuator in desired
closed position.
11. Operate the unit several times and recheck position. If unit is still
out of adjustment, reset the cams by following steps 9 and 10.
12. Installation in hazardous areas requires that the electrical leads be
sealed within 18 inches of the enclosure in accordance with Local
and National Electrical Codes.
13. Open conduit entries must be closed up after installation is
complete using a close-up plug engaging at least five full threads
and approved for use in hazardous locations.