Flowserve 25 75 Motor Module Kit 120/240 VAC User Manual
Installation, operation and maintenance, Description, Motor module removal
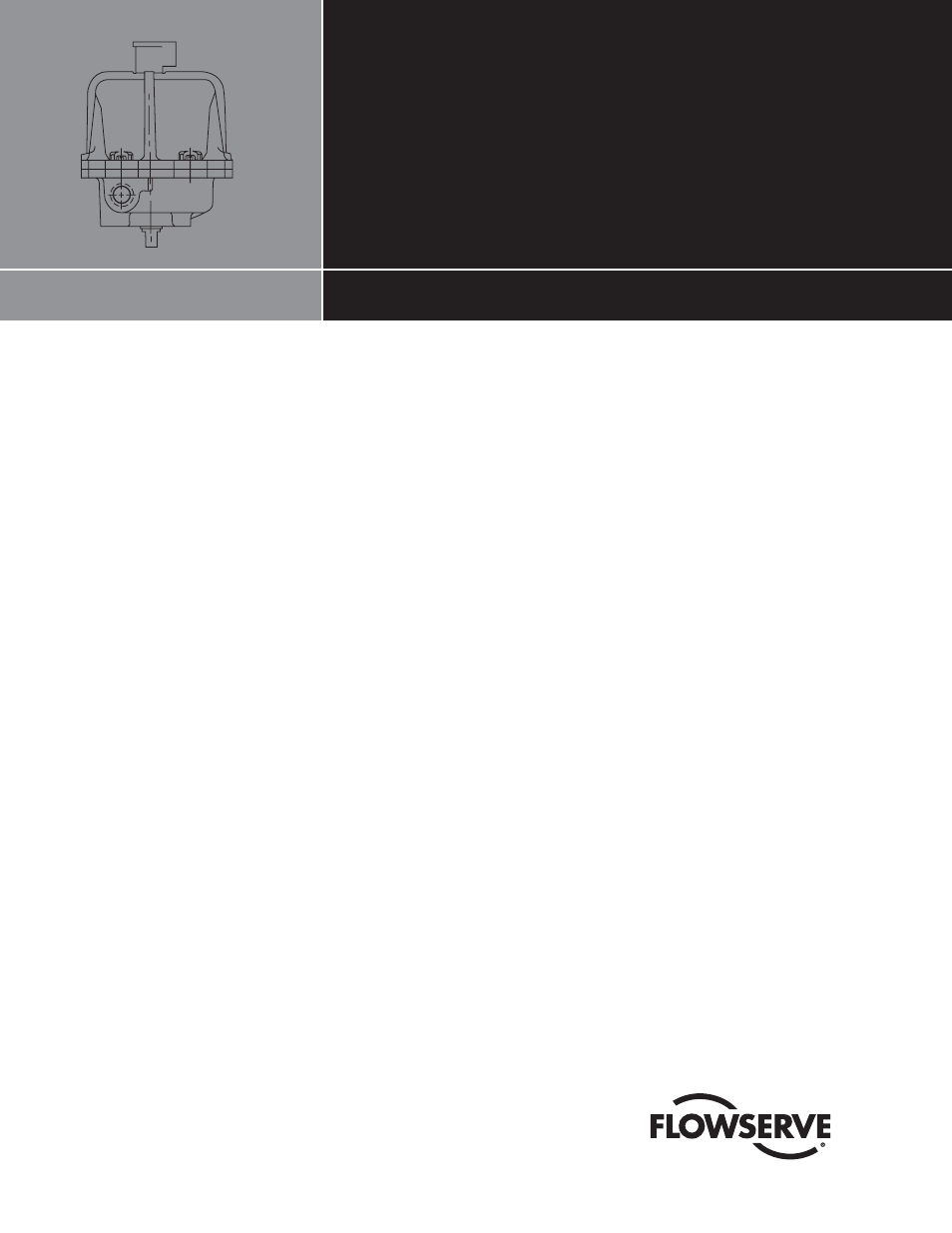
25/30 75 Motor
Module Kit 120/240 VAC
Installation, Operation and Maintenance
FCD WCAIM2065-00 (Part 06228)
Description
Motor module kits are intended as repair kits for 25/30 75 electric
actuators. Attached diagrams show typical installation of these kits,
which should be installed exactly as the motor modules they are
replacing.
Prior to replacing motor module: Be sure actuator is disconnected
from any power source.
Verify that the replacement capacitor and motor have the proper
voltage rating.
Motor Module Removal
1. Disconnect all power to the actuator.
2. Cut cable ties (9). (Replacement ties are provided.)
3. Remove white motor wire from terminal of the actuator’s
terminal strip. Remove all input wiring from terminal strip.
4. Disconnect wires from capacitor. (Note location of wires on
diagram.)
5. Cut capacitor tie (13) or remove capacitor O-ring, whichever is
present.
6. Remove cams (10) from sensing shaft (4). (Note position of
cams.)
7. Remove retaining ring (11) from sensing shaft (4).
8. Remove fi ve 10-32 socket head cap screws (7) and capacitor
bracket (14) (if present) from motor support plate (1).
NOTE: If capacitor is mounted on top of motor support plate,
it is not necessary to remove capacitor in order to replace motor
module.
9. Lift out motor support plate (1).
10. Remove plastic fan (5).
11. Loosen set screw (6) on pinion gear (3) and remove pinion gear
from sensing shaft (4).
12. Remove four 10-32 socket head cap screws (7) and lockwash-
ers (8) holding motor (2) to motor support plate (1).
Motor Module Replacement
1. Replace motor to motor support plate, making sure that lead
wires are facing capacitor. Center motor to hole in motor
support plate and securely tighten cap screws.
2. Replace pinion gear. Locate gear .96" from motor support
plate (see Figure 1) and securely tighten gear set screw onto fl at
of shaft.
3. Replace motor support plate with motor on actuator.
4. Replace motor support screws. Replace capacitor bracket (if
present and removed); turn motor shaft extension back and
forth. Backlash between the motor pinion and mating gear is
allowed, but should be minimal. Move the motor support plate
in proper direction to minimize backlash, then tighten motor
support plate screws.
5. Replace retaining ring in groove on sensing shaft.
6. Replace cams on sensing shaft. (These will be reset later.)
7. Replace capacitor with new capacitor and secure with new
capacitor tie (do not reuse O-ring), and connect all motor and
capacitor leads. If capacitor has metal retaining ring, insulating
fi ber washer must be used.
8. Replace plastic fan on top motor shaft. (Do not permit fan to
touch motor.)
8PSDFTUFS"DUVBUJPO4ZTUFNT