Valve disassembly and replacement of plug – Flowserve PlugSeal User Manual
Page 10
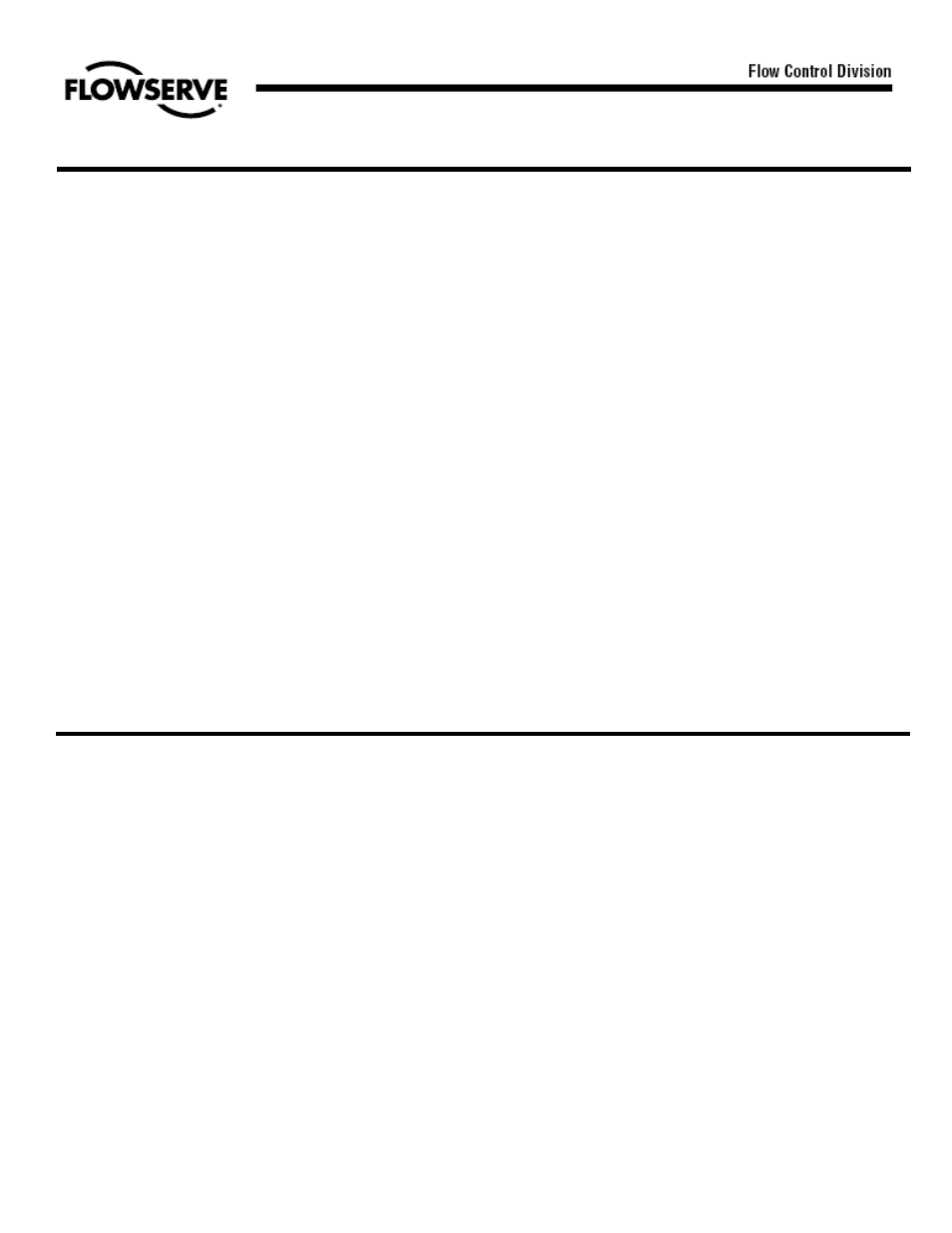
7
SECTION IV.
OPERATING / MAINTENCE INSTRUCTIONS
Maintenance requirements for Plugseal valves may vary
due to operating conditions of the process. Factors such
as operating temperature, pressure, solids content, and
frequency of cycling can influence valve performance
and maintenance requirements. Seal wear is
compensated by adjusting appropriate parts. For
Plugseal valves, there are three possible leak paths:
1. Top
Cap
(bonnet)
2. Stem
3. Line
(through)
Corresponding adjustments for each leak path are as
follows:
Note: Refer to Figure 1 for parts identification.
1. Top Cap (bonnet)
Leakage due to thermal or pressure cycling is
eliminated by snugging the top cap fasteners (Part
10) in a criss-cross pattern. This adjustment is most
effective when the valve is not pressurized. It is
important that the top cap fasteners not be tightened
excessively and that torque values applied remain
within industry standard for fasteners.
2. Stem
Leakage due to wear of the diaphragm, and/or wear
to the sleeve (primary seal) is eliminated by
tightening the adjuster fasteners (Part 11) in 1/4 turn
increments. It is recommended that the adjuster
fasteners be tightened evenly. The valve should be
operated between adjustments to assure that the
plug properly seats itself into the body. If leakage
persists after repeated adjustments, the plug and
diaphragm will require replacement as covered in
SECTION V.
3. Line (through)
Through leakage due to wear of the primary seal
can be eliminated by tightening the adjuster
fasteners (Part 11) in 1/4 turn increments. It is
recommended that the fasteners be tightened
evenly. The valve should be operated during
adjustments to prevent excessive operating torque.
Should leakage persist after repeated adjustments,
the plug will require replacement as covered in
SECTION V.
SECTION V.
VALVE DISASSEMBLY AND REPLACEMENT OF PLUG
RECOMMENDED PRECAUTIONARY MEASURES:
1. Valves must be relieved of process product and
pressure prior to disassembly.
2. Personnel performing disassembly must be suitably
trained, protected and alert for emission of
hazardous process product.
DISASSEMBLY STEPS
NOTE: Refer to Figure 1 for parts identification.
REMOVAL OF TOPWORKS SIZES 1” – 4”
1. Note the orientation of the wrench relative to the
body for proper reassembly.
2. Loosen the set screw securing the wrench and
remove the wrench (Part 15) from the stem.
3. Lift retainer spring (Part 17) and top cap lock (Part
16) off of the stem.
REMOVAL OF TOPWORKS SIZES 6” – 16”
1. Alignment marks should be noted to assure correct
orientation when reassembled. This may best be
accomplished by making matching marks on the
plug stem and operator housing with no burrs made
on the plug stem.
2. Remove handwheel and gear by removing fasteners
between gear and bracket.
3. Lift coupler off stem and remove bracket by
removing fasteners between bracket and valve.
VALVE DISASSEMBLY
4. Gradually loosen adjuster fasteners (Part 11) - DO
NOT REMOVE.
5. WARNING: Do not loosen or remove top cap
fasteners (Part 10) when removing an operator.
Remove the operator by unfastening it from the
bracket and removing the bracket from the valve.