I. valve, Worcester controls – Flowserve 51 Series Fire-Safe Valves User Manual
Page 2
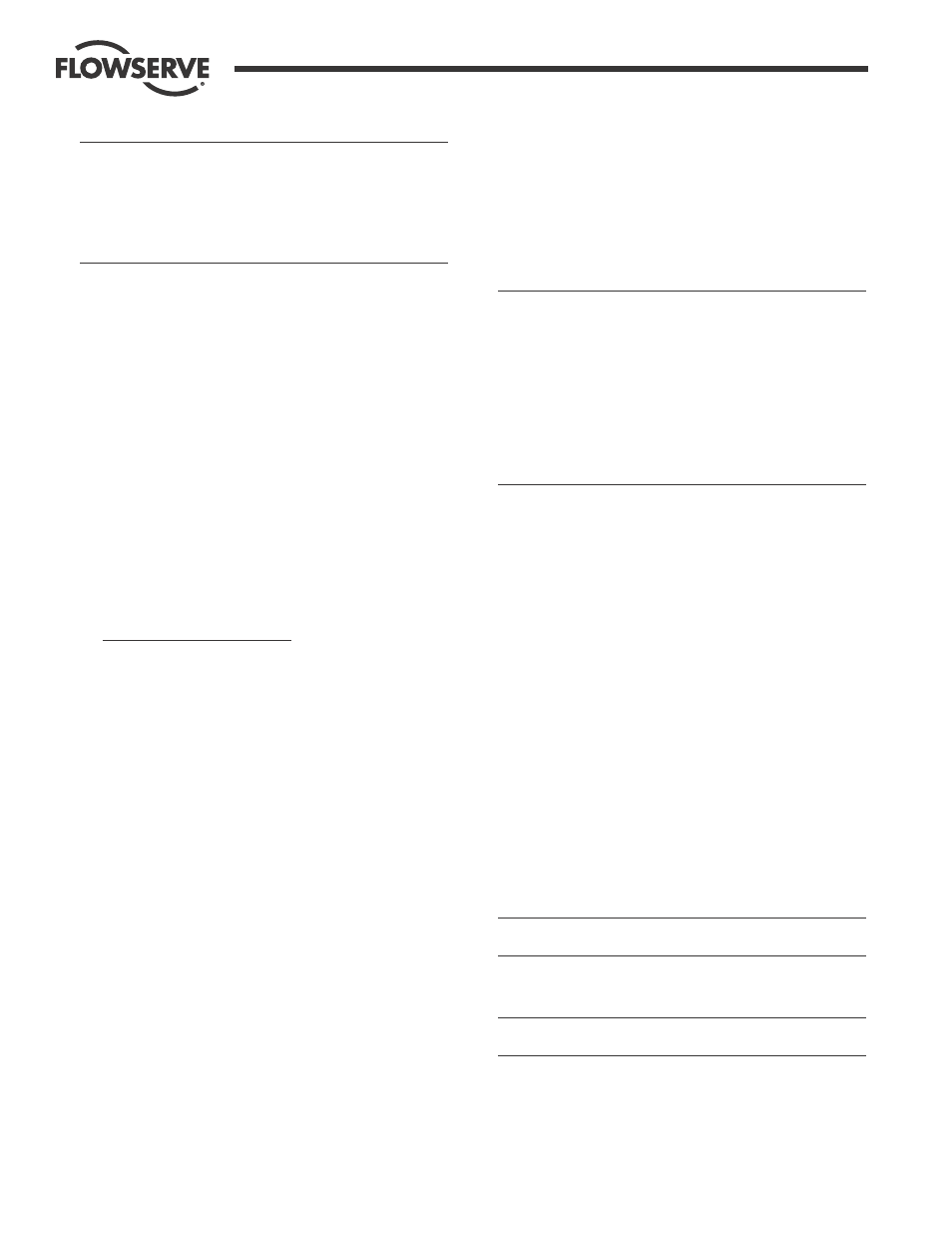
2
19406-H
Flow Control Division
Worcester Controls
CAUTION: Flowserve recommends that all product which must
be stored prior to installation be stored indoors, in an
environment suitable for human occupancy. Do not store
product in areas where exposure to relative humidity above
85%, acid or alkali fumes, radiation above normal background,
ultraviolet light, or temperatures above 120°F or below 40°F
may occur. Do not store within 50 feet of any source of ozone.
I. VALVE
A. Installation
1. Valves may be installed for flow in either direction. Use care
to exclude pipe sealants from the valve cavity. Note that the
maximum pressure rating for these valves is 125 psig.
2. When installing, certain line flange bolts and gaskets are
specifically required in order to be in conformance with FM
requirements.
a. Flange bolts shall be: ASTM A193, Gr. B7; Nuts: ASTM
A194, Gr. 2H.
b. Flange gaskets shall be Spirotaulic, or equivalent.
3. Install valve into pipe line and secure all flange bolts evenly.
Tighten the bolts to the following recommended torque
values:
Bolt Size
Torque
1
/
2
-13
87 Ft.-Lbs.
5
/
8
-11
178 Ft.-Lbs.
3
/
4
-10
253 Ft.-Lbs.
B. Operation
1. The operation of the FM fire valve depends upon the
attachments and options included with the valve.
a. For actuated fire valve with Series 39 actuator only, refer
to Section II of this manual.
b. For actuated fire valve with Series 39 actuator and end
mounted limit switches, refer to instruction sheet that
comes with the switches.
c. For control valve, refer to PM15 instruction manual.
d. For manual operated valves with handles, refer to the next
paragraph.
2. The operation of the manually operated valve consists of
turning the handle
1
/
4
turn clockwise to close and
1
/
4
turn
counter-clockwise to open. When the valve is closed, the
handle points across the line, providing position indication.
3. These valves will provide bubble-tight shutoff when used in
accordance with the Worcester pressure/temperature chart.
4. It is not good practice to leave ball valve partially open
(throttling operation) without knowledge of the pressure drop
and flow at that position.
5. As shipped from the factory, valves contain a silicone based
lubricant. This is for break-in and may be removed (by
disassembling and solvent washing) if it is objectionable for a
particular application. Lacquer thinner will remove the
lubricant.
6. Media which can solidify, crystallize, or polymerize should not
be allowed to stand in ball valve cavities.
CAUTIONS:
7. The fluoropolymer body seal makes an excellent seal.
However, some points of caution in its use need emphasizing.
a. No fluoropolymer part (except seals) is reusable. Upon
disassembly of the valve, they should be discarded and
replaced with new parts.
b. Care must be taken to avoid scratching the fluoropolymer
during installation. Light lubrication can help to prevent
damage.
C. Maintenance
It is possible that, under certain circumstances, there could be
some seepage past the stem seals. If this should occur, simply
tighten the retaining nut, for 3" -4" valves only,
1
/
6
of a turn at a
time, until the seepage stops. (Do not overtighten. This can cause
higher torque and adversely affect the stem seal life.) For
1
/
2
"-2"
valves only, adjust as follows:
For Valves with two stem nuts and a lockwashwer (with or
without handle):
1. Tighten retaining nut (lower nut) until Belleville washers are
flat, the nut will “bottom”.
2. Back off retaining nut
1
/
6
turn.
3. Tighten handle nut securely to lock retaining nut in place.
For valves with self-locking stem nut (and four Belleville
washers):
4. Tighten self-locking stem nut until Belleville washers are flat,
the nut will “bottom”.
5. Back off nut
1
/
3
turn.
CAUTION: The self-locking stem nut is difficult to tighten, and
must fully flatten Belleville washers before backing off.
D. Rebuilding
WARNING: BALL VALVES CAN TRAP PRESSURIZED FLUIDS IN
BALL CAVITY WHEN CLOSED
If the valve has been used to control hazardous media, it must be
decontaminated before disassembly. It is recommended that the
following steps are taken for safe removal and disassembly.