Unpacking, Installation – Flowserve Valtek Mark One and Mark Two Control Valves User Manual
Page 5
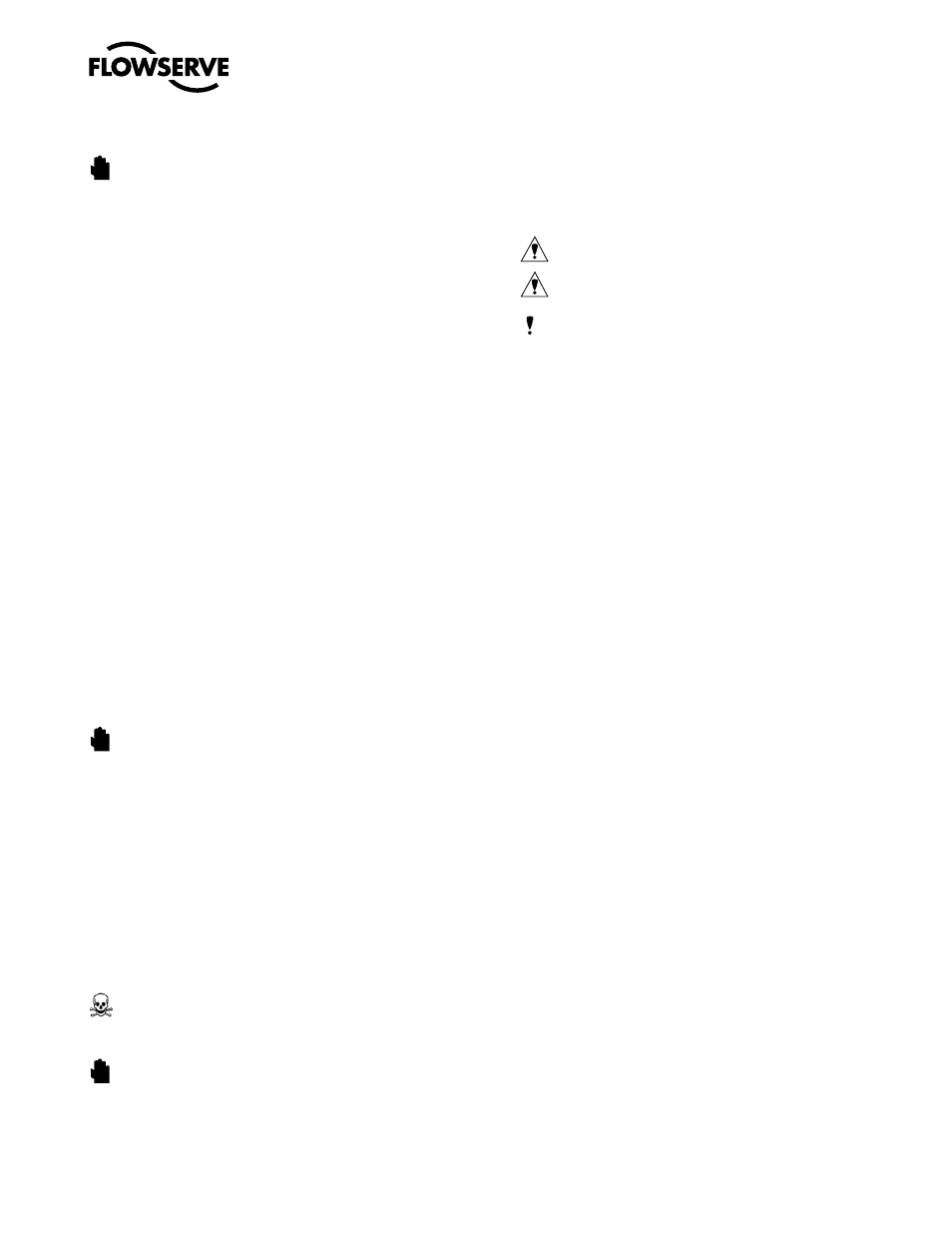
5
®
Valtek Mark One and Mark Two Control Valves FCD VLENIM001-01-AQ - 8/14
WARNING: Before products are returned to Flowserve for
repair or service, Flowserve must be provided with a cer-
tificate that confirms that the product has been decontami-
nated and is clean. Flowserve will not accept deliveries if a
cleaning certificate has not been provided. Return authoriza-
tion is also required before parts are returned. Contact your
local Flowserve representative to obtain return authorization.
1.8. Storage
In many cases, Flowserve products are manufactured from
stainless steel. Products not manufactured from stainless
steel are provided with an epoxy resin coating. This means
that Flowserve products are well protected from corrosion.
Nevertheless, Flowserve products must be stored adequate-
ly in a clean, dry environment. Plastic caps or plywood pro-
tectors are fitted to help protect the flange faces and prevent
the ingress of foreign materials. These caps should not be
removed until the valve is actually mounted into the system.
2. Unpacking
2.1.
While unpacking the valve, check the packing list against the
materials received. Lists describing the valve and accesso-
ries are included in each shipping container.
2.2.
When lifting the valve from shipping container, use straps
through the yoke legs, or the lifting lugs attached to the
body bolting for valves over four inch, or the adjusting
screw for valves four inch and under. Take care to position
lifting straps to avoid damage to the tubing, mounted acces-
sories, or stroke plate.
WARNING: When lifting a valve be aware that the centre of
gravity may be above the lifting point. Therefore, support
must be given to prevent the valve from rotating. Failure to
do so can cause serious injury to personnel and damage to
the valve and nearby equipment.
2.3.
Contact your shipper immediately if there is shipping dam-
age.
2.4.
Should any problem arise, call your Flowserve representa-
tive.
3. Installation
DANGER: Before installation check the purchase order num-
ber, serial number, and/or the tag number to ensure that the
valve and actuator being installed are correct for the intend-
ed application.
WARNING: The maximum air supply for most Valtek cylin-
der actuators is 150 psi (10.3 bar). In some cases, the air
supply must be limited to less than 150 psi (10.3 bar). This
is indicated on a sticker found near the upper air port on
the actuator cylinder. An air regulator should be installed
to ensure the supply pressure does not exceed the actuator
design pressure indicated on the sticker.
CAUTION: Do not insulate extensions that are provided for
hot or cold services.
CAUTION: On valves equipped with air filters, the air filter
must point down to perform properly.
NOTE: Selecting the proper fastener material is the responsi-
bility of the customer. Typically, the supplier does not know
what the valve service conditions or environment may be.
Flowserve‘s standard body bolting material is B7/2H. B8/8
(stainless steel) is optional for applications more than 800°
F / 425° C and with stainless steel or alloy body valves. The
customer therefore must consider the material‘s resistance
to stress corrosion cracking in addition to general corrosion.
As with any mechanical equipment, periodic inspection and
maintenance is required. For more information about fas-
tener materials, contact your Flowserve representative.
3.1.
Pipelines must be correctly aligned to ensure that the valve
is not fitted under tension.
3.2.
Fire protection must be provided by the user.
3.3.
Before installing the valve, clean the line of dirt, welding
chips, scale and other foreign material.
3.4.
Whenever possible, the valve should be installed in an
upright position. Vertical installation permits easier valve
maintenance. This is also important for cryogenic applica-
tions to keep the packing isolated from the flowing medium,
permitting the packing temperature to remain close to am-
bient temperature.
3.5.
Be sure to provide proper overhead clearance for the ac-
tuator to allow for disassembly of the plug from the valve
body. Refer to the appropriate actuator User Instructions for
proper clearances. Actuator User Instructions are available
at www.flowserve.com.
3.6.
Double-check flow direction to be sure the valve is installed
correctly. Flow direction is indicated by the arrow attached
to the body.
3.7.
If welding the valve into the line, use extreme care to avoid
excess heat buildup in the valve.
3.8.
If the valve has separable end flanges, verify that the half
rings are installed on the valve body before bolting the valve
into the line.
STOP!
STOP!
STOP!