Repair procedures, Cont.) – Flowserve V-378 R1 Edward Equiwedge Gate Valve User Manual
Page 10
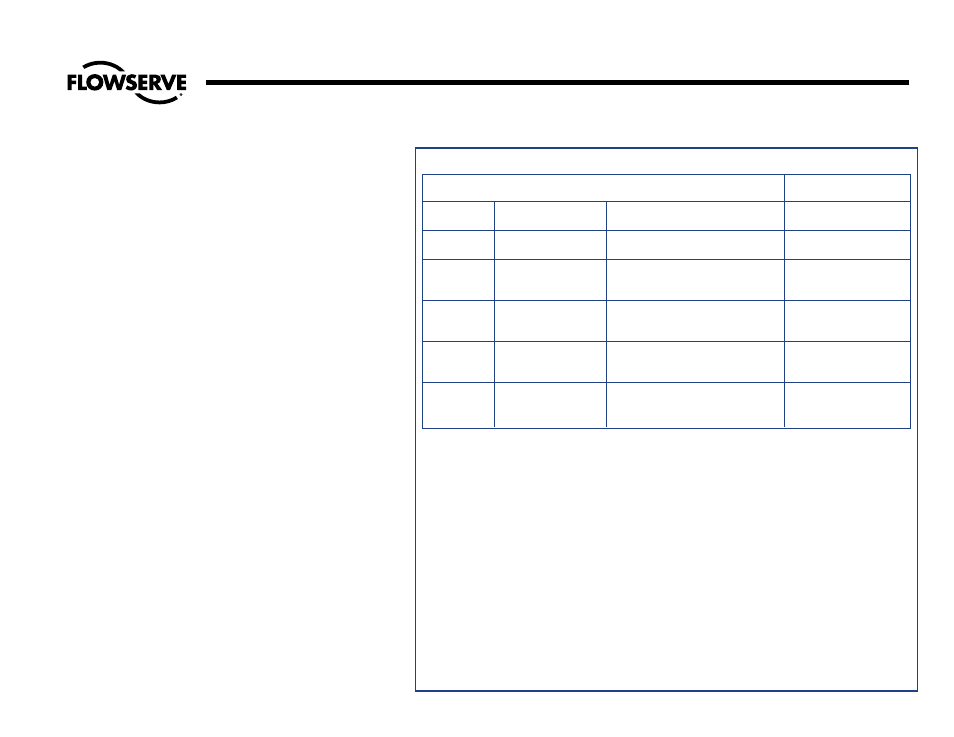
10
Flow Control Division
Edward Valves
It is best that a new pressure-seal
gasket be used upon reassembly.
Body Wall Repairs
There are five basic steps in repairing a
casting defect:
1. Cut out to sound metal. Attempting to
weld over the defect will only leave a
notch that may re-introduce the defect.
Cutting may be done by chipping,
grinding or flame gouging. The amount
of metal removed should be held to a
minimum to avoid distortion during sub-
sequent welding.
2. Preheat, using the minimum temperature
specified by the material specification
and/or the design code. Use at least
400F on WC9 or C5 material, 300F
on WC6. Although cast carbon steels
such as WCB or WCC do not require
preheat, it may be advantageous to
remove any moisture or other contami-
nants from the area to be welded. This
may also identify any leak paths. There
are also disadvantages to preheat,
especially localized preheat, that must
be considered when working in areas
of the casting with finish machined
dimensions. Distortion may result in
more damaging problems than those
concerns created by the original defect.
Lower preheats and the control of inter-
pass temperature are two methods used
to minimize distortion.
3. Welding should be done by qualified
welders, using qualified procedures and
weld material of a chemistry matching
the casting (see Table 3 for welding rod
recommendations). The final weld
TABLE 3 – WELDING ROD RECOMMENDATIONS
MATERIAL TO BE WELDED
WELD ROD
RECOMMENDATIONS
ASME IX
Material
ASTM Grade
AWS Classification
P-Numbers
P-1
Carbon Steel
1. ASTM A216, Grade WCB
AWS 5.1
2. ASTM A105
E7018
P-4
1-1/4% Chromium,
1. ASTM A217, Grade WC6
AWS 5.5
1/2% Molybdenum
2. ASTM A182, Grade F11
E8018-B2
Low Alloy Steel
P-5
2-1/4 Chromium,
1. ASTM A217, Grade WC9
AWS 5.5
1% Molybdenum
2. ASTM A182, Grade F22
E9018-B3
Low-Alloy Steel
P-8
18% Chromium,
1. ASTM A351, Grade CF8M
AWS 5.4
8% Nickel
2. ASTM A182, Grade F316
E316
Stainless Steel
P-8
18% Chromium,
1. ASTM A351, Grade CF8C
AWS 5.4
8% Nickel
2. ASTM A182, Grade F347
E347
Stainless Steel
Repair Procedures
(cont.)
WELDING EDWARD VALVES IN-LINE
When welding a valve in line, the installer
should apply the specific technical rules
imposed by the jurisdictional authority of the
area where the valve is installed, In the
absence of such rules, following are
suggested practices for welding Edward
Valves in line:
1. Welding should be done using procedures
and personnel qualified in accordance
with ASME Section IX. Rules for preheat
and postheat are stated in Chapter V of
ASME B31.1 (Power Piping).
2. The valve should be welded in line, one
end at a time, in a closed position
(approximately a half-turn after the seat in
the body comes in contact with the disk).
This is suggested to preclude warpage
between seating surfaces caused by tem-
perature induced stresses during welding
or subsequent heat treat. It also protects
the seat from weld spatter that might coat
the lapped seat and disk. When postweld
heat treat is required, each weld end
should be heat treated one at a time, to
minimize impact of heat on valve internals.
Do not heat treat an Edward Valve with a
piping attached as a unit in a furnace, as
warpage of parts may occur. After weld-
ing, open the valve and flush the line to
clean out all foreign matter.