Flowserve SLM-6200 User Manual
Page 11
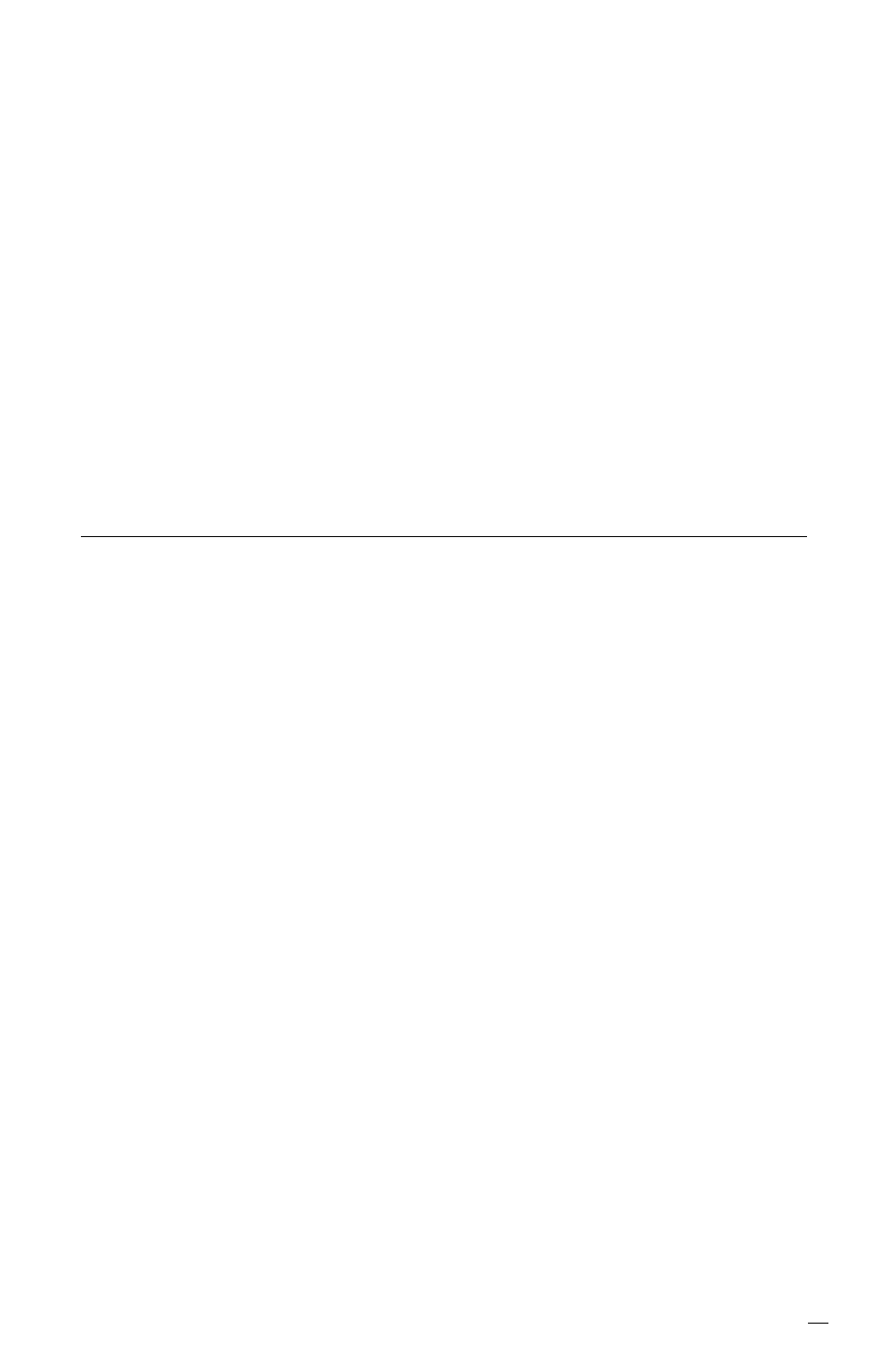
11
7.2 Connect the seal gland barrier outlet (BO) port to the return side of the external
system. 3/4” tubing is recommended for the seal circulation piping on both outlet and
inlet runs. Piping runs should be smooth, with a minimum number of turns. Turns
should be accomplished by large radius bends rather than elbow fittings.
7.3 Connect the seal gland barrier inlet (BI) port to the supply side external system.
7.4 Connect a regulated pressure source and and pressure gages to monitor the barrier
pressure. Barrier fluid temperature must be kept below 79°C (175°F).
7.5 Your SLM-6200 Mechanical Seal is now ready for operation.
Warning:
To ensure that the mechanical seal does not run dry, leave motor v-belts or
drive coupling off the pump until the motor has been tested for rotation.
Note: For any subsequent impeller or bearing adjustment, reverse steps 6.1, and 6.2.
If any problems arise during installation, Do not try to force anything, contact your
nearest Flowserve Sales and Service Representative or Authorized Distributor.
8 Start Up and Shut Down Procedures for the SLM-6200
Slurry Seal
The SLM-6200 seal incorporates its own operating environment. To insure the proper
conditions in this environment, observe the following procedures for pump operation:
8.1 Pump Start-Up
8.1.1 Pressurize the water barrier fluid system to 2 bar (30 psi) above the
maximum expected seal chamber pressure and be sure it is flowing.
8.1.2 Open the valve on the suction line to ensure that the pump is fully flooded
with product.
8.1.3 A pump flooded with liquid must be ensured, before starting. If possible, open
washout/bleed venting valve to release any air that may be trapped in the
piping. Close the valve after a steady stream of liquid flows from it. If little or
no liquid appears, do not start the pump. This means that part of the piping
system is blocked with product.
8.1.4 Partially open the discharge valve to ensure that water hammer or cavitation
does not occur at start-up.
8.1.5 After start up, slowly open the discharge valve. This will keep a false/artificial
head/back-pressure on the pump until the line fills.
8.2 Pump Shut-Down
8.2.1 Stop the pump.
8.2.2 Close the discharge valve.
8.2.3 Close the suction valve.
8.2.4 Before depressurizing the water barrier system, drain all product from the
pump seal chamber or flush with clean water or process fluid to prevent
solids in the slurry (either free solids or dissolved solids that will precipitate
out when temperature is reduced during standby) from settling in the seal
chamber or volute. This also prevents product from contaminating the barrier
system when barrier pressure is released.