7 testing of turbine with seals – Flowserve GTS Series User Manual
Page 9
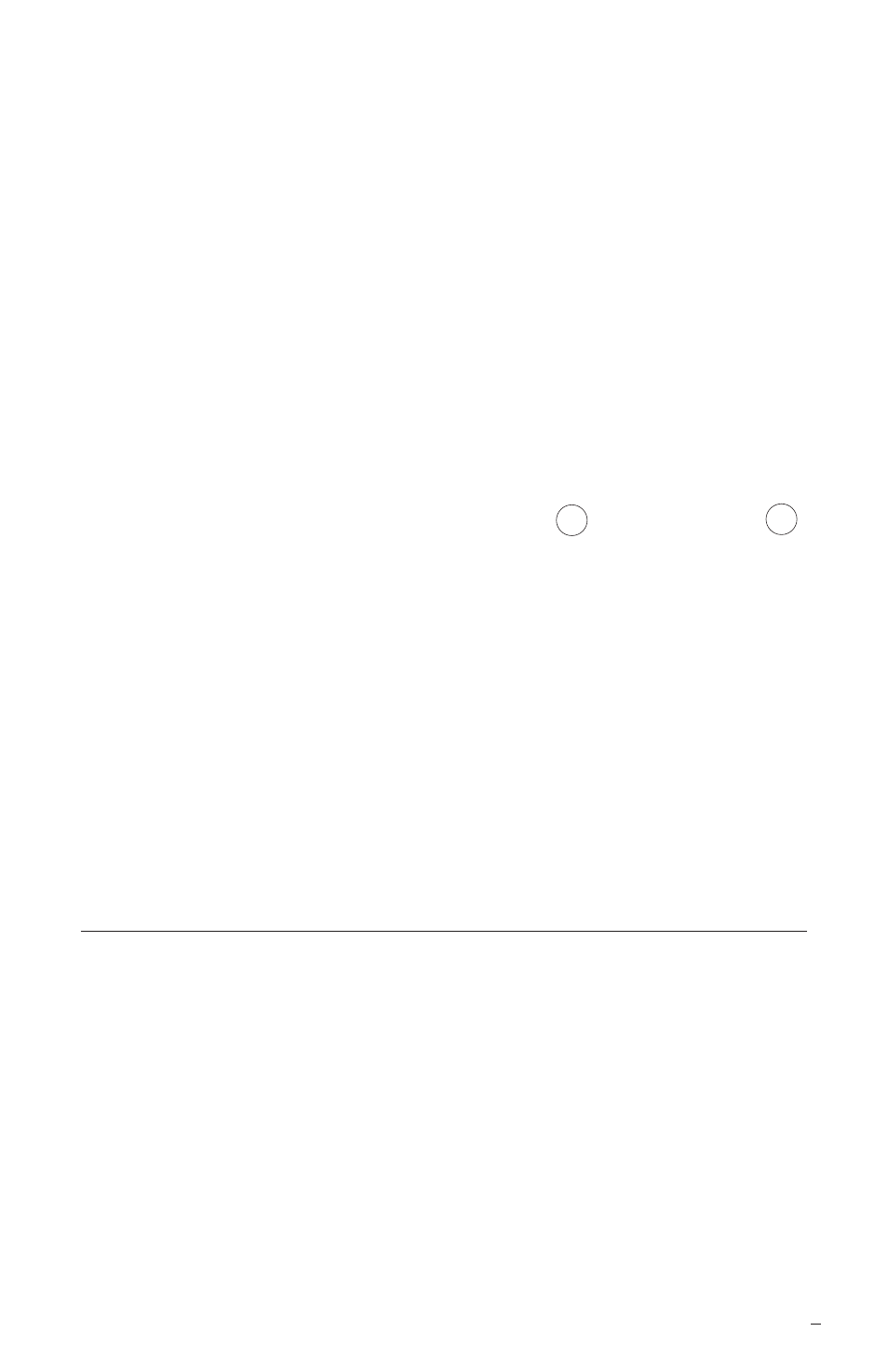
6.3 Lower the rotor into the bottom half of the turbine case and onto the journal
bearings. Make sure the seals are located in the correct groove in the
turbine case. The thrust bearing should axially locate the rotor correctly
in the case. Verify that the nozzle clearance meets the manufacturers
specification.
6.4 Use machinist’s blue or a scribe to mark the location of the sleeve end
nearest the wheel (setting plate side of the seal, opposite the drive collar).
If seals were installed using Method 1, marking the location of the sleeve
end as described here will simplify reinstallation.
6.5 Remove the rotor from the case.
6.6 At least one threaded hole, usually #8-32, is provided in the end of the
sleeve in addition to the one required to screw the setting plate to the
sleeve. Find a #8-32 set screw and use this hole to secure the end of the
sleeve to the shaft at the location marked in step 6.4.
6.7 Tighten the sleeve gasket compression screws 40 and the set screws 57 .
Make sure the seal stays in the correct location. The drive collar should
draw up on the sleeve. It is usually much easier and faster to tighten these
screws when access is not restricted by the case, as is the situation with
Method 1. Also, it is possible to measure the torque used to tighten the
sleeve gasket compression screws.
6.8 Remove the screw installed in 6.6 to hold the seal in the proper location.
Steam corrosion could cause the screw to seize. Also, if later forgotten
during disassembly damage to the shaft could occur during disassembly.
6.9 Build up the rotor and install it into the turbine.
6.10 Remove the setting plates and finish assembly of the turbine.
7 Testing of Turbine with Seals
After installing GTS seals in a turbine, static and dynamic testing under air or
steam pressure is recommended. Safety precautions for pressurized equipment
should be followed at all times. Note that if GTS seals are exposed to a slug of
water they will leak more until the water has dissipated.
7.1 Seal the turbine case exhaust and inlet with flanges rated for at least 50
psig (345 kPa) or the desired back pressure. Connect a pressure source
and provide a pressure indicator rated for 344 kPa (50 psig) or the desired
back pressure.
7.2 Pressurize the turbine case to 344 kPa (50 psig) with no shaft rotation to
test static leakage. GTS seals faces lift off with pressure so some leakage
9