Energy management, Dc link, Operating modes of the ax5021 – BECKHOFF AX5021 User Manual
Page 7: Braking power diagnosis
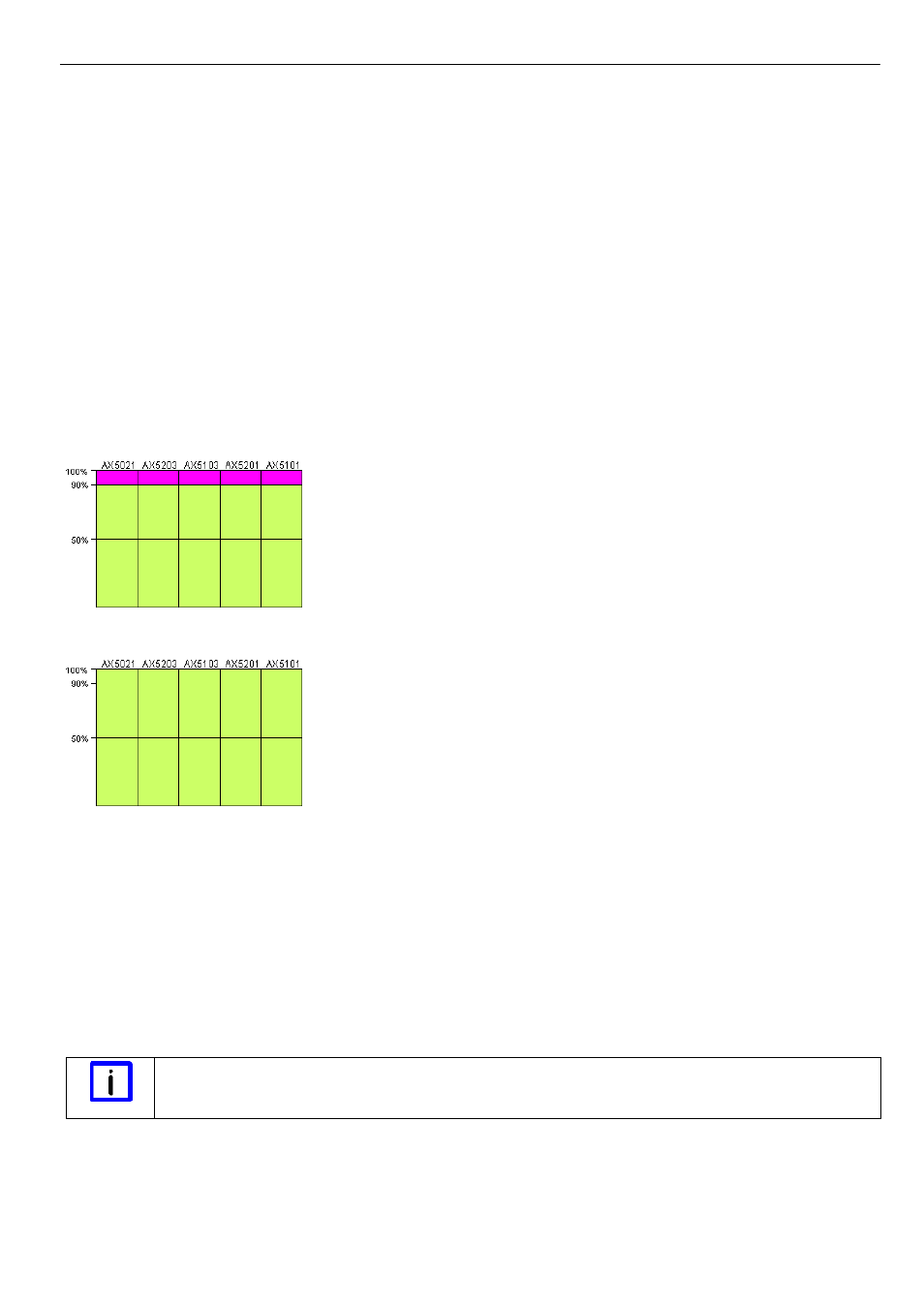
BECKHOFF
Drive Technology
Brake module AX5021 – Version: 1.2
Page 7/8
Energy management
Intelligent energy management ensures that energy is distributed evenly to the DC links and the internal brake resistors when devices are used
commonly in the drive system. This reliably prevents the undesirable permanent load of only one device.
DC link
The connected servomotors are supplied with energy from the DC link. It serves as an energy storage and first needs to be charged up after
switching the device on, before it can supply the servomotors. The DC link is designed such that it can take up and store a certain degree of surplus
energy from the motor (brake energy) and subsequently supply the motor again with this stored energy. If the upper limit of the energy storage is
reached, the brake chopper feeds any further brake energy into the internal or external brake resistor, where it is converted into heat; it is then no
longer available for the further operation of the motor. The voltage is taken and evaluated as the indicator for the current energy level of the DC link.
As soon as the brake resistors have also reached their energy limit, the error ‘FD4C, DC link – overvoltage’ appears and the energy flow to and from
the motor is interrupted, i.e. the motor makes uncontrolled movements.
In a drive system, the DC links of the individual devices are connected so that the energy level of all devices is the same, regardless of which motor
the brake energy is currently being fed back from. In many cases these feedbacks do not happen at the same time, and without a DC link system,
for example, a device would be at the limit and would already have to ‘destroy’ energy in a brake resistor, even though other devices could still store
energy in the DC link. The energy could be saved in a DC link system, because the DC links of all connected devices are charged up first, before
the energy is converted into heat in the brake resistors.
Operating modes of the AX5021
It can be assumed that a brake module is used only if the brake energy cannot be dissipated despite a DC link system and internal brake resistors.
The brake module can be operated in 2 different operating modes, which have a direct influence on the energy management. The operating modes
can be selected when using the external brake resistor. The following sketches show the storage capacity of the DC link of the individual devices in
relation to the operating modes.
Standard operating mode 1 Ext. brake resistor enabled (system / standard)
In this operating mode the capacity of the DC link of the brake module is reduced by approx. 10%.
At 90% DC link load the brake chopper then directs the generated braking energy to the external
brake resistor and, when this has reached its capacity limit, into the internal brake resistor.
This operating mode is set as the default, because no further configuration of the devices in the DC
link system is necessary apart from the basic configuration of the brake module. If the external
brake resistor of the brake module is mounted outside the control cabinet, then the thermal load in
the control cabinet is also lower.
Operating mode 2 Ext. brake resistor enabled (standalone brake chopper)
In this case the capacity of the DC links is fully utilised; however, the internal brake resistors of the
servo drives should be deactivated, so that the surplus energy is only taken up by the brake
module.
This operating mode must be selected and, apart from the basic configuration of the brake module,
the internal brake resistors of the devices in the DC link system should be deactivated, as otherwise
the thermal load in the control cabinet will also increase. In order to reduce the thermal load further,
it is a good idea to mount an external brake resistor on the brake module outside the control
cabinet.
Braking power diagnosis
The current continuous output of the brake resistor can be read via the IDNs P-0-0209 (int. brake resistor) and P-0-0210 (ext. brake resistor). The
unit is watts. Loads above 90% of the continuous output of the brake resistor should be avoided. The IDNs can be read cyclically as process data.
The current impulse energy load of the brake resistor can be read via the IDNs P-0-0218 (int. brake resistor) and P-0-0219 (ext. brake resistor). It is
specified in % with one decimal place. Loads above 90% should be avoided. The IDNs can be read cyclically as process data.
The maximum energy values since the last reset are stored in IDNs P-0-0220 (int. brake resistor) and P-0-0221 (ext. brake resistor). The values can
be reset by entering zero. Duty cycle corresponds to 100 seconds. The energy values are monitored at the specified intervals (100 ms, 1 s, 10 s, 20
s, 40 s and 100 s). The values for 100 s correspond to the continuous output. The maximum values should be approx. 10% below the resistor limits
(P-0-0207 or P-0-0208). If a current energy value exceeds the limit value of a brake resistor, this brake resistor is not enabled. In a drive systems or
in a configuration with active internal chopper the other brake resistors have to absorb the energy. If this is not possible the DC link voltage will
continue to increase until an overvoltage error occurs, followed by disabling of the axes with "Torque off". It is therefore important to ensure that
adequate braking power is available in the systems, in order to avoid uncontrolled movements of the axes. The diagnostics should cover the whole
system. If not enough reserve capacity is available, an external brake resistor with a higher output should be selected. If the performance limit is still
reached, several AX5021 may be used.
Note
Energy balance!
The energy balance is affected positively whenever an axis requires energy and another axis produces generative energy
(braking energy). This rule should be observed in all applications.